- 2024/08/10
-
長物加工を成功させるためのプロの技術とコツを紹介
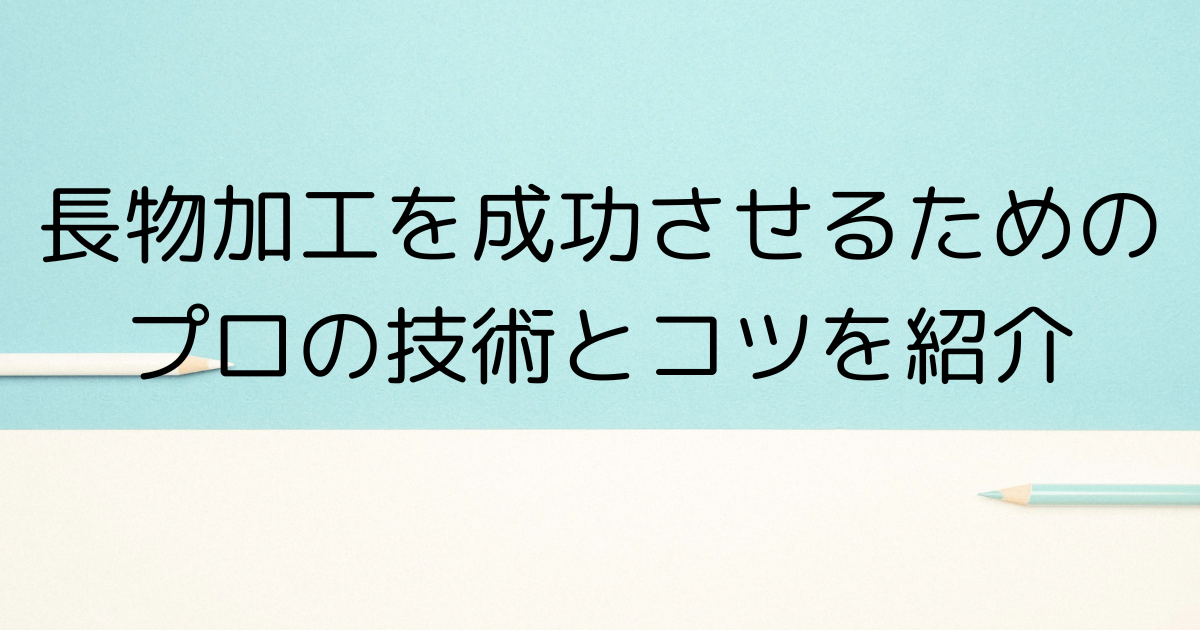

長物加工を成功させるためには、その基本概要とポイントを押さえることが大切です。この記事では、旋盤を使った長物加工の基本技術や刃物選定の重要性、具体的な切削条件の設定方法など、プロの技術とコツを詳しく紹介します。最適な旋盤の選び方からトラブルシューティングまで、長物加工の実践的なノウハウを学び、加工の精度と効率を向上させましょう。
1. 長物加工の基本概要とポイント

長物加工とは、長くて細い物を正確に切ったり磨いたりする技術です。この加工は、金属やプラスチック、木材などさまざまな素材に対応できます。重要なポイントは、加工の精度や仕上がりの品質でしょう。加工の過程では、高精度の機械を使用し、細心の注意を払って作業を行うことが求められます。特に、長物の寸法や形状を正確に保つためには、熟練した技術が必要になります。
1.1. 長物加工の特徴とは
長物加工の特徴は、その長さと細さにあります。このため、加工には特別な技術や機器が必要となります。例えば、長物は折れやすいので、慎重に取り扱わなければなりません。そして、高精度の機械を使用して、微細な寸法の調整を行うことが求められます。さらに、これらの加工は、しばしば高速で行われるため、作業のスピードと正確さの両立が重要です。
また、長物加工には熟練した技術者の経験と知識が求められます。彼らは、加工の際に発生する様々な課題に対処する方法を知っています。例えば、加工中に発生する振動や熱をコントロールする技術が必要です。そして、それらの問題を解決しながら高品質な仕上げを行います。最終的には、こうした技術と知識が製品の品質を決定します。
1.2. 長物加工の主な用途
長物加工は、幅広い分野で活用されています。例えば、自動車産業では、エンジン部品やシャフトの加工に使用されます。これらは高い強度と精度が求められるため、長物加工の技術が不可欠です。また、航空機産業でも多くの部品にこの加工方法が使われています。これにより、飛行機の安全性が確保されます。
さらに、日常生活の中でも、さまざまな製品が長物加工で作られています。例えば、家具の脚やインテリア製品のフレームなどが挙げられます。これにより、製品のデザインや耐久性が向上します。そして、医療機器や精密機器の分野でも、この加工技術が重要な役割を果たしています。これらの用途により、長物加工の重要性はますます高まっています。
2. 旋盤を使った長物加工の基本技術

旋盤は、金属加工において非常に重要な機械です。その特に、長物加工には欠かせない存在となります。長物加工とは、長い部品や素材を正確に削り出したり、ねじ切りしたりする技術です。これには、旋盤の基本操作や選び方、設置方法などの知識が必要です。この章では、旋盤を使った長物加工の基本技術について詳しく説明していきます。
2.1. 旋盤の選び方と設置方法
旋盤を選ぶ際には、まず加工する素材や部品のサイズを考慮する必要があります。旋盤には、さまざまなサイズや種類があり、それぞれの用途や目的に適したものを選ぶと効率的です。また、設置場所の確保も重要です。旋盤は大型機械になるため、十分なスペースが必要です。
設置場所を選定する際には、床の耐荷重性も確認しましょう。重さに耐える床でなければ、安全に作業を行えません。さらに、通気性の良い場所を選ぶと、熱の発散も容易になります。
最後に、旋盤のメンテナンス方法についても考慮します。定期的な点検を行うことで、機械の寿命を延ばし、安定した加工精度を維持することができます。これらの要素を踏まえて、適切な旋盤を選び、設置場所を決定しましょう。
2.2. 長物加工における旋盤のメリット
長物加工において旋盤は非常に優れた性能を発揮します。一つ目のメリットは加工精度の高さです。旋盤を使うことで、微細な寸法調整が可能であり、高精度な加工が実現できるのです。また、旋盤はさまざまな素材に対応できる柔軟性があります。
次に、旋盤は効率的な作業を可能にします。手作業では難しい大きな素材も、旋盤なら短時間で正確に加工できます。そのため、時間を大幅に短縮できるのです。また、旋盤は安定した性能を維持するため、品質のばらつきが少ないという利点もあります。
さらに、旋盤を使うことで、さまざまな形状の加工が可能です。円柱形のものから複雑な形状まで、多様な部品を作り出せるのです。これにより、多様なニーズに柔軟に対応できるようになります。
2.3. 基本的な旋盤操作手順
旋盤の基本操作手順を理解することは、効率的で安全な加工を行うために非常に重要です。最初に、加工する素材を旋盤に固定します。固定が不十分だと、加工中に素材が動いてしまう危険がありますので、確実に固定しましょう。
次に、加工条件を設定します。回転速度や切削の深さなど、素材に適した条件を設定することが重要です。これにより、きれいな仕上がりを実現することができます。そして、実際に加工を開始します。
最後に、加工終了後は、素材を取り外し、仕上げ作業を行います。バリ取りなどの細かい作業も丁寧に行うことで、完成度の高い製品が得られます。このような基本操作手順を守ることで、安全で精度の高い長物加工が可能になります。
3. 刃物選定の重要性と選び方

刃物を選ぶことは、仕事の効率と仕上がりに大きな影響を与える重要な作業です。選定を誤ると、切れ味が悪く作業が進まないだけでなく、道具や素材にまで悪影響が及ぶことがあるのです。適切に選ぶためには、作業内容や素材に応じた刃物を選定することが求められます。このように、刃物を正しく選ぶことが成功への第一歩と言えるでしょう。
3.1. 刃物選定の基本的な考え方
刃物を選ぶ基本的な考え方として、使用目的に応じた素材選びが重要です。例えば、硬い素材を切る場合は、高硬度の刃物が必要です。また、耐久性も考慮すべき要素です。耐久性が低い刃物は、頻繁に交換が必要となり、コストが増えるためです。さらに、刃物の形状も選定時には大切な要素となります。
刃物の形状は、用途によって異なります。直線切りには直刃が適しており、曲線切りには曲刃が良いでしょう。加えて、持ちやすさや重さも作業の効率に大きく関わってきます。
刃物選定では、これらの要因を総合的に考慮する必要があります。そうすることで、最適な刃物を選び、作業効率を最大化することができるでしょう。
3.2. 長物加工に適した刃物の種類
長物を加工する際には、特定の刃物が適しています。例えば、バンドソーは長いものの切断に非常に適しています。長物を安定して切るためには、刃物の歯間(はま)が広いタイプが良いです。また、ハンドソーも手軽で便利です。これも刃間が広いタイプを選ぶと切れ味が持続します。
次に、電動工具を使う場合の刃物についてです。テーブルソーは長物を正確に切断するのに優れています。刃先が鋭く、かつ耐久性のある素材のものを選ぶことで、長期間にわたり高品質な加工が可能です。
最後に、刃物の保管と手入れも忘れてはいけません。長物を加工する刃物は大型なものが多いため、適切な方法で保管することが重要です。また、使用後は必ず清掃し、次回の作業に備えるのが良いでしょう。
3.3. 刃物メンテナンスのポイント
刃物のメンテナンスとして、まずは定期的な清掃が欠かせません。使用後には必ず刃に付いた切りくずやオイルをきれいに拭き取ります。そうすることで、錆びの発生を防ぎます。また、刃の研ぎ直しも定期的に行うことが重要です。研ぎ直しを適切に行うことで、切れ味を長持ちさせることができるでしょう。
さらに、保管方法もメンテナンスの一環です。湿気の多い場所や直射日光が当たる場所は避けて保管します。そのための専用ケースやカバーを使うと効果的です。
これらのメンテナンスを怠ると、刃物の寿命が短くなります。その結果、新しい刃物を購入するコストが増えてしまうでしょう。ですから、日常的なメンテナンスを心掛けることが大切です。
4. 切削条件の設定方法

切削条件を正しく設定することは、加工の精度と効率に大きな影響を与える重要なポイントです。まず、素材の特性や加工内容に基づいて、適切な切削速度やフィードレートを設定します。次に、切削液の選定と使用方法についても考慮しなければなりません。さらに、実際の加工中に切削条件を微調整することで、最良の結果を得ることが可能です。このように切削条件の設定を細心の注意を払って行うことが、成功の鍵なのです。
4.1. 最適な切削速度とフィードレートの設定
最適な切削速度とフィードレートを設定するためには、まず加工材の性質を理解することが必要です。硬度や熱伝導率、材質の種類などが重要な要素となります。これらを基にして、切削速度を決定します。例えば、硬度の高い材料には低速の切削速度が適しています。次に、フィードレートも慎重に設定しましょう。フィードレートは、工具の切削量を調整する重要な要素です。
フィードレートが高すぎると良好な表面仕上げが得られません。逆に、低すぎると加工時間が長くなります。したがって、適切なバランスを見つけることが重要です。さらに、切削速度とフィードレートは、鋼またはアルミニウム等の具体的な素材に応じて微調整する必要があります。具体的な切削速度とフィードレートの設定値は、加工条件や使用する機械によります。
4.2. 切削液の選定と使用方法
切削液の選定と使用方法も、切削条件の重要な要素です。切削液は、潤滑や冷却の役割を果たし、工具の寿命を延ばす効果があります。まず、使用する加工材や工具に最適な切削液を選定します。鉱油系や合成系など種類がありますが、それぞれの特性を理解することが重要です。次に、切削液の供給方法についても考慮しましょう。
例えば、スプレー方式やフラッディングなど、適した方法を選びます。適切な量と供給方法を維持することで、効果的な切削が可能です。また、切削液は定期的に交換し、清潔な状態を保つことも大切です。それにより、工具や加工物への影響を最低限に抑えることができます。これが、精度の高い加工を実現するための基本です。
4.3. 切削条件の調整による加工精度向上
切削条件の調整は、加工精度を向上させるための重要な要素です。最初に選んだ条件が必ずしも最適であるとは限らないため、加工中に微調整を行います。例えば、切削速度とフィードレートの見直しは、加工精度を高めるための一般的な方法です。また、工具の状態を定期的にチェックすることも大切です。
工具が摩耗すると、加工精度が低下しますので、定期的に交換や調整をします。さらに、温度や振動なども加工精度に影響を与えるため、これらの環境条件も確認しましょう。加工中に常にモニタリングし、変化があれば速やかに対応します。こうした細やかな調整と管理が、高精度な加工を保証するための鍵なのです。これにより、より良い結果が得られるでしょう。
5. 加工におけるトラブルシューティング

加工中に発生するトラブルは生産効率を大きく低下させる原因となります。そうしたトラブルを未然に防ぐためには、問題の早期発見と迅速な対応が重要です。そのためには、加工プロセスを詳細に把握し、問題が発生しやすい箇所を特定することが求められます。また、トラブル発生時には迅速に適切な対策を講じることで、大きな問題に発展するのを防ぐことができます。
5.1. 加工中の一般的なトラブルとその対策
加工中に最も一般的に発生するトラブルとして、工具の摩耗や破損、材料の熱変形、加工面の不良などが挙げられます。工具の摩耗を防ぐためには、適切な工具選びと定期的な交換が必要です。さらに、材料が熱変形しやすい場合は、冷却水の使用を検討するとよいでしょう。
次に、加工面の不良は、使用する工具の種類や加工条件が適切でないことが原因となります。加工条件の見直しや、より高品質な工具の採用で改善できます。また、加工プロセス全体を定期的に点検し、問題箇所を特定することも重要です。
これらの対策を講じることで、加工中の一般的なトラブルを大幅に減少させることができます。そして、トラブルが発生した場合には迅速に対応することで、生産効率を維持することが可能です。
5.2. 振動や騒音の抑制方法
振動や騒音は加工精度や作業環境に悪影響を与えるため、抑制することが重要です。まず、機械自体のメンテナンスを定期的に行い、振動源を特定します。特に軸受けや回転部分の点検は必要です。次に、振動を吸収するためのダンパーや防振材を適切に配置すると効果的です。
さらに、作業中に発生する騒音を抑制するためには、防音材の導入や機械の設置場所を工夫することが有効です。作業場全体のレイアウトを見直し、騒音が外部に漏れないように設計することで、作業環境の改善が期待できます。
これらの対策を総合的に行うことで、振動や騒音を効果的に抑制することができます。結果として、加工精度の向上と作業員のストレス軽減につながるでしょう。
5.3. 加工面の品質不良の改善策
加工面の品質不良は、生産品質に大きな影響を与えるため早期に対策を講じる必要があります。まずは加工条件を詳細に見直し、適切な切削速度や送り速度を設定することが重要です。さらに、適切な冷却剤を使用することで、加工面の温度を管理しやすくなります。
次に、使用する工具の選定も重要です。工具が摩耗している場合や適していない場合、加工面に不良が発生しやすくなります。高品質な工具を選び、定期的に交換することが求められます。また、工具の設定角度や取り付け方法にも注意が必要です。
最後に、加工機械自体の精度を維持することも重要です。定期的なメンテナンスを実施し、機械の精度を確認することで、加工面の品質不良を防ぐことができます。これらの改善策を実行することで、加工品質の向上が期待できるでしょう。
お問い合わせ
弊社製品、加工についてのお問い合わせは、こちらで受付しております。
各部門のスペシャリストが、ご質問にお応えします。
電話
0574-54-2231
(平日 8:15~17:15)
FAX
0574-54-2235