- 2024/05/10
-
円筒研磨とは?難しい?芯出しや揺れ止め・メーカー紹介
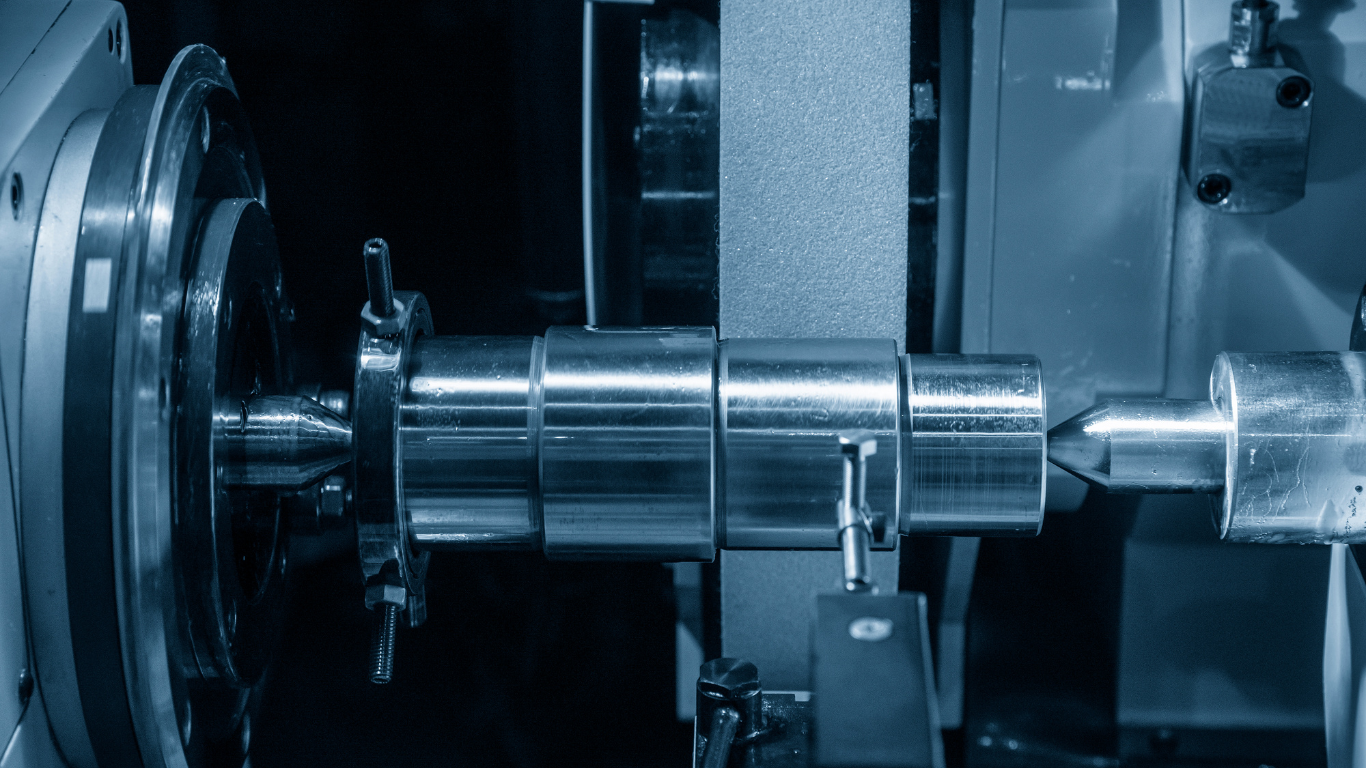
円筒研磨は精密部品の製造で不可欠な加工技術です。本ブログでは、円筒研磨の基本から、高難度の「芯出し」や「揺れ止め」などのテクニック、さらにセンタレス研磨との違いについて詳しく解説します。
また、円筒研磨機を提供する有名メーカーもご紹介します。初心者からプロまで知識が深まる内容ですので、ぜひ最後までお読みください。
目次 [hide]
円筒研磨(研削)とは
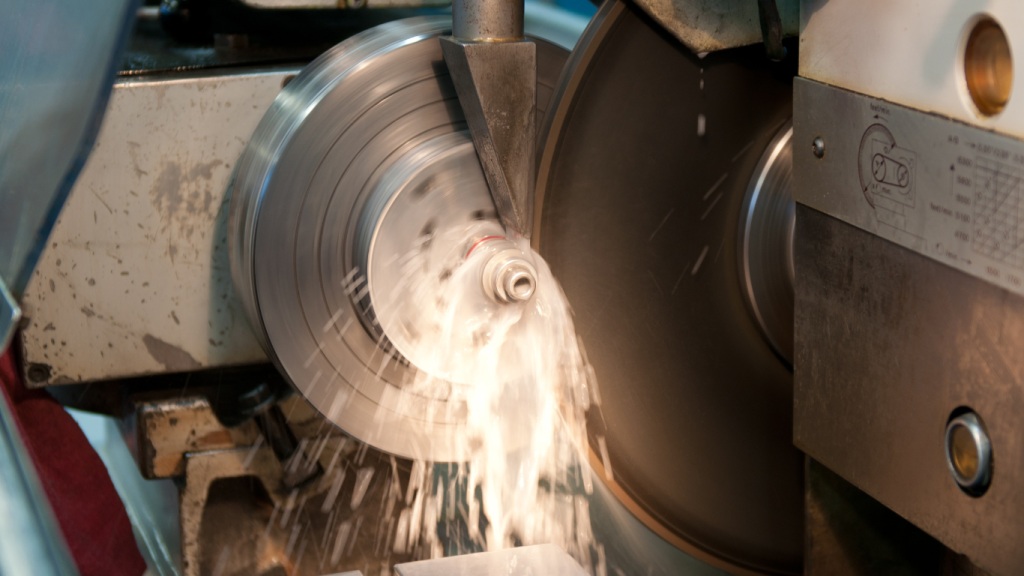
円筒研磨(えんとうけんま)とは、金属などの材質の円筒形状を持つ部品の外周表面を磨く技術のことです。作業は精密機械加工の一環として行われ、非常に高い精度で仕上げられるため、機械部品の製作に欠かせない工程です。
この技術は、外径や内径の寸法精度を確保するために重要であり、また表面の粗さを低減する目的でも使用されます。円筒研磨は、円筒形状の維持が求められる自動車部品や航空機部品の製造において特に重要です。
円筒研磨の芯出し
円筒研磨の芯出しは、精密加工において重要なプロセスの一つです。円筒形の部品を研磨する際には、部品の中心軸が研磨機の回転軸と完全に一致するように設定する必要があります。これにより、均一な研磨が可能となり、製品の品質を保証することができます。
芯出しの基本手順
- 測定: 最初に、部品の実際の中心位置を精密測定器を使用して測定します。この測定には、ダイヤルゲージやレーザー測定器が用いられることが一般的です。
- 調整: 測定結果を基に、部品を機械に取り付ける際の位置を調整します。このとき、機械のスピンドルやチャックに部品を固定し、必要に応じて微調整を行います。
- 確認: 調整後、再度中心軸が正確に位置しているかを確認します。この確認作業を通じて、部品の芯が正しく出ているかを検証します。
使用ツールとその特徴
- ダイヤルゲージ: 機械の動きを利用して微細な位置のずれを測定する。高い精度が要求される場合に適しています。
- レーザー測定器: 非接触で測定を行うため、高速かつ正確な測定が可能です。大型の部品や複雑な形状の測定に適しています。
円筒研磨の芯出しは、部品の精度や機能性に直接影響するため、非常に重要です。正確な芯出しが行われないと、部品の不均一な摩耗、寿命の短縮、または性能不足の原因となります。そのため、芯出し作業には専門的な知識と熟練した技術が求められます。
円筒研磨の揺れ止め
円筒研磨の振れ止めは、細長い工作物を旋盤や円筒研削盤で加工する際に使用される重要な器具です。この装置は、工作物の曲がりや振動を防ぎ、加工精度を向上させるために用いられます。振れ止めには大きく分けて「固定振れ止め」と「移動振れ止め」の二種類があります。
- 固定振れ止め: これは機械のベッドに固定され、加工中の工作物を支える役割を果たします。固定された位置で一定の支持を提供することで、工作物の振動を抑え、加工の精度を保ちます。
- 移動振れ止め: 移動振れ止めは、機械のサドルに取り付けられ、工具や砥石と共に移動します。これにより、工作物の全長にわたって均一な支持を提供し、特に長い工作物の加工において振動を効果的に防ぐことが可能です。
どちらのタイプも、精密加工において非常に重要な役割を担い、工作物の振れや曲がりを最小限に抑えることで、高品質な製品を製造するために不可欠です。また、振れ止めの選定や設定は、加工される材料の特性や機械の性能に適したものを選ぶことが重要であり、適切な振れ止めの使用は製品の品質を大きく左右します。
センタレス研磨(研削)との違い
円筒研磨のセンタレス研磨(研削)と他の研磨方法との違いについて解説します。
センタレス研磨(研削)
センタレス研磨は、工作物をセンタリングピンやチャックに固定せずに研磨する方法です。これにより、工作物に支持センターを必要とせず、円筒形の部品を迅速かつ効率的に加工することができます。主に次のような特徴があります:
- 支持センターが不要:工作物を特定の位置で固定する必要がないため、セットアップ時間が短縮され、生産効率が向上します。
- 高い生産性と柔軟性:小さな部品から比較的大きな部品まで、幅広いサイズの工作物に対応可能です。
- 高精度の仕上がり:工作物を均一に加工できるため、精度の高い仕上がりを実現します。
円筒研磨
円筒研磨では、工作物を機械の回転軸に合わせてセンターやチャックで固定します。この方法では、工作物の両端を支持する必要があり、次のような特徴があります:
- センタリングが必要:工作物を正確にセンタリングする必要があるため、セットアップに時間がかかります。
- 振れ防止:長い工作物を加工する場合、センタリングが不十分だと加工中に振れが発生しやすくなります。
- 高い精度:適切にセットアップされた場合、非常に高精度な加工が可能です。
用途の違い
センタレス研磨は、特に大量生産に適しており、迅速な加工が求められる場合や、セットアップ時間を短縮したい場合に有効です。一方、従来の円筒研磨は、高精度が必要な精密部品の加工や、工作物の長さがセンタレス研磨で対応できない場合に選ばれます。
円筒研磨(研削)のメリットデメリット
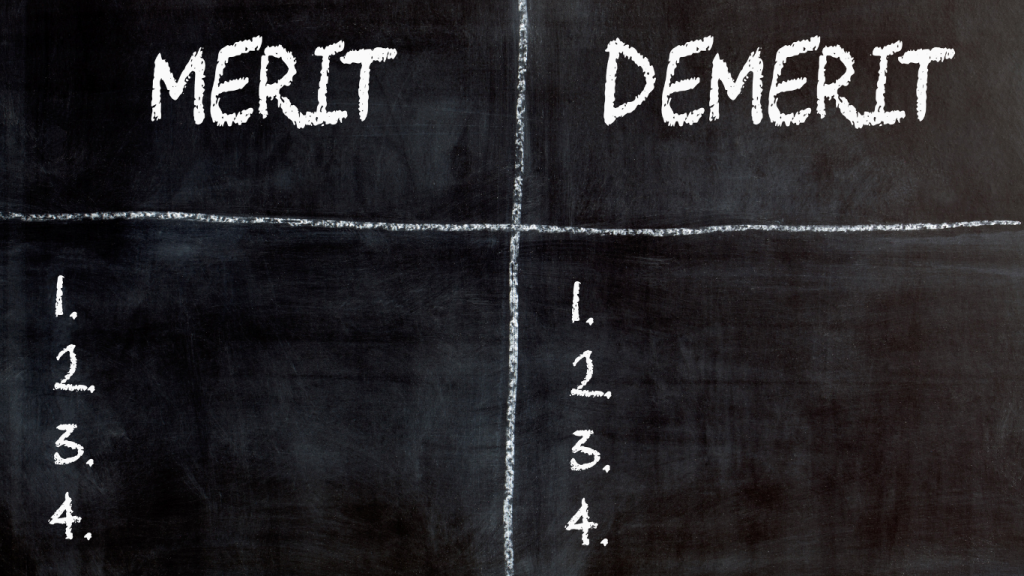
円筒研磨によって非常に高精度な加工が可能である一方で、加工の難易度やコストも考慮する必要があります。これから、円筒研磨の具体的なメリットとデメリットについて詳しく説明していきます。
円筒研磨(研削)のメリット
円筒研磨(研削)のメリットです:
- 高精度の加工が可能:
- 円筒研磨は、非常に高い精度で部品を加工できます。これにより、要求される公差と表面粗さを満たすことができ、組み立てや後工程での問題を最小限に抑えることが可能です。
- 表面品質の向上:
- 研磨プロセスは、部品の表面を滑らかにし、鏡面のような仕上がりを実現します。これは、摩擦を減少させ、部品の耐久性を向上させる効果があります。
- 複雑な形状の加工:
- 円筒研磨機は、円筒形部品だけでなく、テーパーや複雑なプロファイルがある部品の加工も可能です。これにより、さまざまな工業製品の製造に対応することができます。
- 生産効率の向上:
- 自動化された円筒研磨機を使用することで、手作業による加工よりも速く、効率的に大量生産が可能です。これにより、生産コストの削減にもつながります。
- 多様な材料への適用性:
- 円筒研磨は、金属はもちろんのこと、プラスチックやセラミックなど、様々な材料に適用可能です。これにより、幅広い産業での需要に応じることができます。
円筒研磨は、これらのメリットにより、自動車部品、航空宇宙部品、精密機械部品など、高精度が求められる多くの分野で重宝されています。
円筒研磨(研削)のデメリット
円筒研磨(研削)のデメリッを挙げてみましょう:
- コストが高い:
- 円筒研磨機は高価であり、また研削盤のメンテナンスや砥石の交換にも費用がかかります。これにより、特に小規模生産ではコスト効率が悪くなることがあります。
- 加工時間が長い:
- 精密な仕上がりを求めるためには、研磨プロセスに時間がかかります。特に高品質の表面仕上げを実現するためには、複数回のパスが必要になることもあり、生産効率に影響を与えることがあります。
- 熱による影響:
- 研磨プロセス中に摩擦熱が発生しやすく、これが部品に熱影響を与えることがあります。過剰な熱は材料の変形や焼けを引き起こす可能性があり、精度に悪影響を及ぼすことがあります。
- 材料の制約:
- 特定の材料は研磨に適していないか、または特別な処理が必要になることがあります。特に軟質材料や非常に硬い材料では、研磨プロセスを適切に調整する必要があります。
- スキル依存:
- 高度な技術を要する操作であり、熟練したオペレーターが必要です。操作者のスキルによって仕上がりの質が左右されるため、人材育成には時間とコストがかかります。
これらのデメリットを理解し、適切に対処することで、円筒研磨(研削)の効果を最大限に引き出すことができます。
円筒研磨(研削)の方法3つ
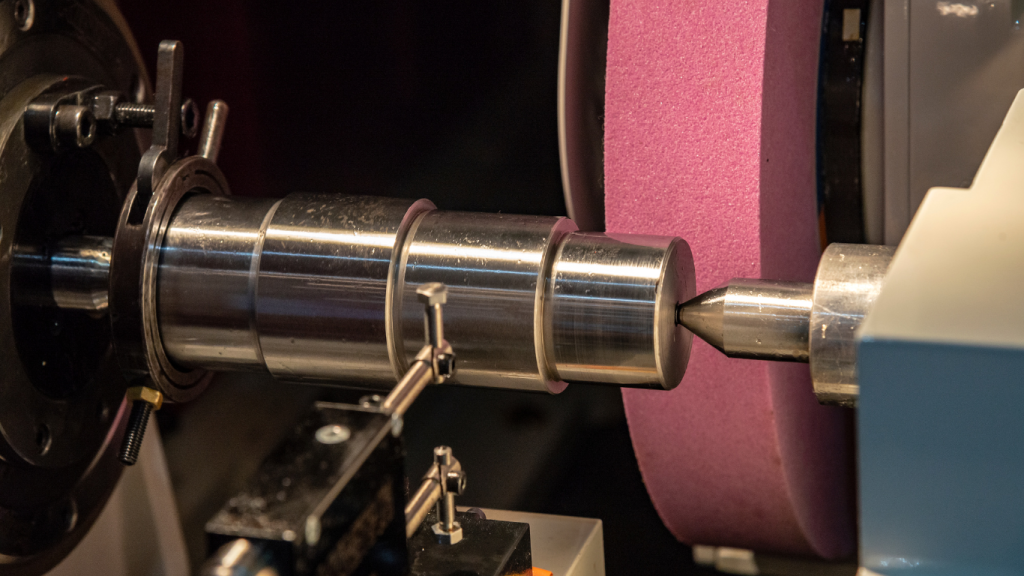
円筒研磨(研削)は、主に丸い部品を高精度に仕上げるための重要な加工法です。まず、研削盤に部品をセットし、回転させながら研削工具で表面を削ります。
この工程では、高精度な寸法や表面の平滑さが求められるため、微細な調整が必要です。使用する研削方法により、加工精度や仕上がりが変わるのが特徴です。次に、代表的な研削方法について説明します。
アンギュラ研削
アンギュラ研削は、研削方法の一つで、砥石を傾けて工作物の端面や斜面を研削する技術です。この方法では、砥石が傾斜しているため、平面や円筒形の外面だけでなく、テーパーや球面などの複雑な形状も加工することが可能です。
アンギュラ研削は、特に精密部品の加工に適しており、自動車のギアや軸受けなど、高い寸法精度と表面精度が求められる部品に使用されます。以下は特徴です:
- 多様な形状加工: 傾斜した砥石を使用することで、直線的な形状だけでなく、斜めの面も精密に加工できます。
- 高精度: 砥石と工作物の接触面積が小さいため、非常に精密な加工が可能です。
- 効率的な加工: 砥石の角度を調整することで、同時に複数の面を加工できるため、加工時間を短縮できます。
アンギュラ研削は、NC旋盤や専用の研削機で行われることが多く、設備によっては高度なプログラミングが必要とされます。この加工方法は、精度と効率を両立させることができるため、高品質な部品製造には欠かせない技術となっています。
プランジ研削
プランジ研削は、工作機械の研削方法の一つで、主に円筒形の工作物を高精度に仕上げるのに使用されます。この方法では、砥石を工作物に対して直線的に押し当てることで、研削を行います。
砥石は工作物の軸に垂直またはそれに近い角度で進行し、一度に全体の面を研削します。これにより、非常に短時間で精密な加工が可能となります。プランジ研削の主な特徴として、以下の点が挙げられます:
- 高速加工:砥石が一度に全面を研削するため、工程が迅速に進みます。
- 高精度:砥石と工作物の接触面が広いため、非常に高い精度で加工が行えます。
- 形状制御:異なる形状の砥石を用いることで、多様なプロファイルの加工が可能です。
プランジ研削は、主に大量生産を要求される部品の製造に適しており、自動車産業や航空産業での部品製造などに広く利用されています。その一方で、研削砥石の摩耗や熱影響などの管理が重要となり、精密な設定と定期的なメンテナンスが必要とされます。
トラバース研削
トラバース研削は、円筒研削の一形態で、砥石を工作物の長さ方向に往復させながら研削する方法です。この技術は特に長い工作物や大きな径を持つ部品の精密加工に適しています。
トラバース研削は、均一な表面仕上げを実現しやすく、特にシャフトやローラーなどの円筒形部品に使用されます。以下特徴です:
- 均一な仕上がり: 砥石が工作物の全長を通して一定の圧力で移動するため、非常に均一な表面粗さが得られます。
- 効率的な加工: 工作物の全長を一度に研削することが可能なため、加工効率が良いです。
- 精度の向上: 往復運動により、砥石の摩耗を均等に分散させることができ、精度を保つことが可能です。
この研削方法は、製造業での利用が広範にわたり、高精度が求められる工業製品の製造に不可欠です。砥石と工作物の速度や圧力を適切に調整することで、求められる仕上がりを実現することが可能です。
円筒研磨(研削)の工程
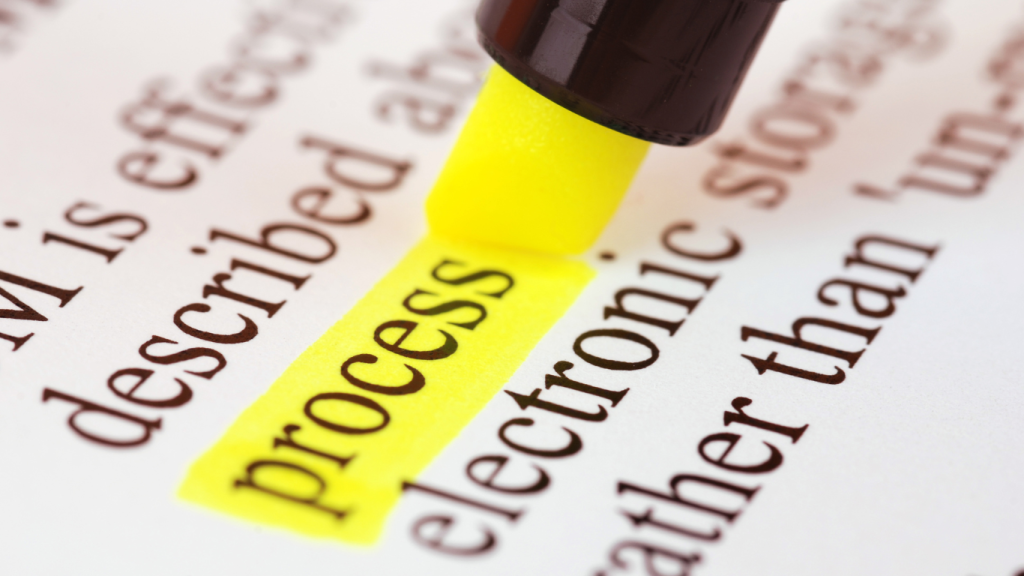
以下は、一般的な円筒研磨の工程です:
- 事前準備:
- 工作物の選定と準備: 研磨する部品を選定し、必要に応じて事前の加工(例えば旋盤加工)を行います。
- 研磨機の設定: 研磨機をセットアップし、砥石やその他の消耗品を取り付けます。
- 粗研磨:
- 加工条件の設定: 研磨速度、送り速度、砥石の種類などの加工条件を設定します。
- 初期研磨: 大きなバリや不均一な部分を取り除き、工作物の大まかな形状を整えます。
- 精研磨:
- 微細加工: 粗研磨で整形された部品をさらに細かく研磨し、必要な寸法精度や表面粗度を達成します。
- 多段階研磨: 必要に応じて、さまざまな粒度の砥石を用いて複数段階で研磨を行うことがあります。
- 仕上げ:
- 最終検査: 研磨が完了した製品の寸法や表面状態を検査し、品質基準に達しているかを確認します。
- クリーニング: 研磨剤や金属粉の残留物を清掃し、製品を清潔に仕上げます。
- 品質管理:
- 検査と評価: 全ての製品に対して、寸法精度、表面粗度、そして場合によっては材質の検査を行います。
- 記録保持: 製品の品質データを記録し、トレーサビリティを確保します。
円筒研磨機の日本国内有名メーカー
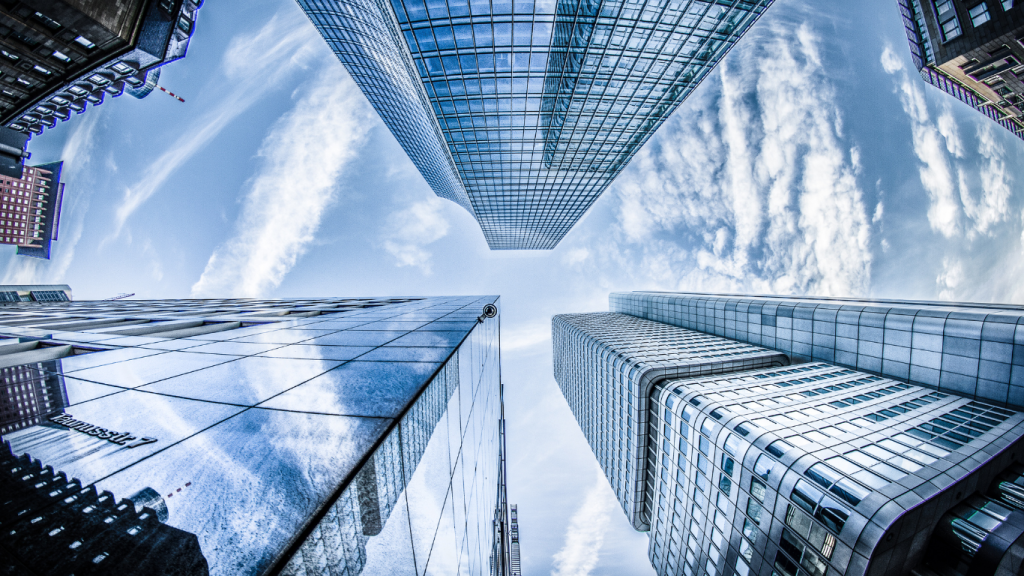
日本の企業で有名な円筒研磨機メーカーとしては、以下のような企業が挙げられます:
- 先進的なCNC工作機械を製造。円筒研磨機においても高精度と耐久性を誇り、多岐にわたる産業で採用されています。
- CNC機械のリーダーとして高い評価。円筒研磨機も含む広範囲の工作機械を提供し、技術革新に注力。
- 自動車業界向けに特化した機械を製造。精密な円筒研磨機を含む、効率と精度を兼ね備えた製品群を展開。
株式会社FUJI(Fuji Machine Manufacturing Co., Ltd.)
- 自動車部品製造に特化した工作機械を提供。円筒研磨機においても、革新的な技術と高性能を追求し続けています。
円筒研磨(研削)の注意点
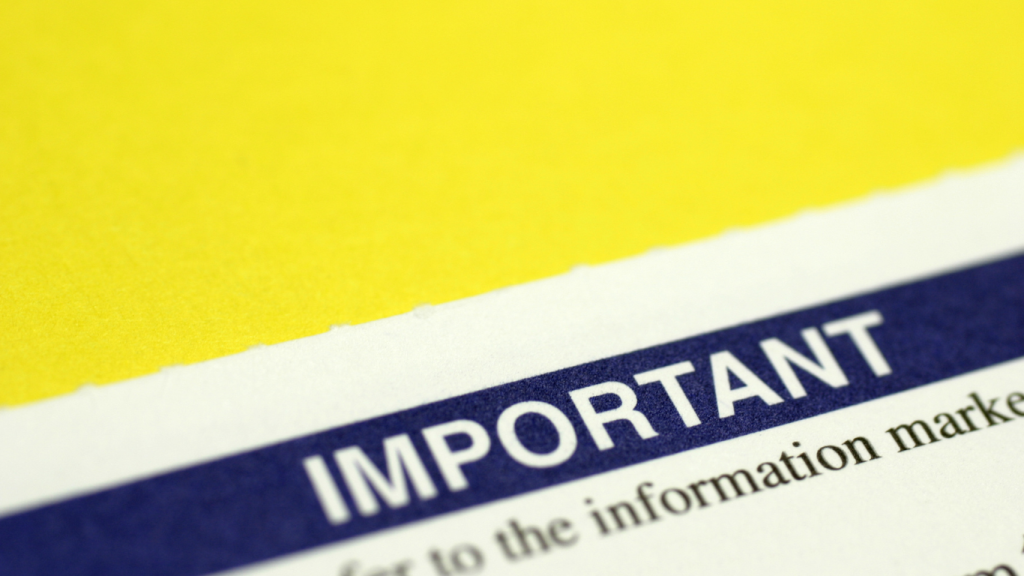
円筒研磨(研削)において注意すべきポイントは以下の通りです:
- 工具の管理:
- 使用する砥石の種類や形状を正確に選定し、定期的に交換する必要があります。砥石の摩耗や破損が加工精度に影響を与えるため、常に最適な状態を保つことが重要です。
- 機械の状態維持:
- 機械の各部が正確に配置されているか、定期的なメンテナンスを行い、特に芯出しやガイドの調整を正確に行うことが必須です。機械の微妙なズレが製品の品質に大きく影響します。
- 加工条件の設定:
- 加工速度、送り速度、砥石の圧力などの加工条件を適切に設定すること。材料や研磨の目的に応じて最適な条件を選ぶことで、高品質な仕上がりを実現します。
- 冷却液の使用:
- 適切な冷却液を使用し、常に適切な流量や温度を保つことで、加工中の熱による影響を最小限に抑えることができます。冷却液が不足すると加工物や砥石の過熱による損傷のリスクが高まります。
- 環境管理:
- 加工環境のクリーンさを保つことも重要です。工場内のほこりや異物が機械に入ることを防ぎ、定期的な清掃を行うことで精度の高い加工が可能となります。
これらの点に注意し、各工程での精度を確保することが、円筒研磨で高品質な製品を生産するための鍵となります。
高硬度材料の研磨(研削)
高硬度材料の円筒研磨では、特に注意が必要です。一般にこのような材料は硬度が高いため、研削抵抗が増加します。これにより、研削ホイールの摩耗が早くなることが多いです。
また、適切な切削条件を選定しないと、研削熱が多く発生し、ワークの寸法精度や表面品質に影響を与えるリスクがあります。したがって、適切な冷却方法とともに、高硬度用の研削ホイールを選ぶことが重要です。これに加え、研削盤の剛性や振動を抑えるための対策が有効となります。
高精度の寸法
高精度寸法を求める場合、円筒研磨には細心の注意が必要です。まず、精密な計測機器で定期的に寸法をチェックすることが基本です。次に、研削盤の設定を最適化するために、定期的なメンテナンスを行うことが肝心です。
また、加工中に発生する熱を最小限に抑えるために、冷却液の使用が不可欠です。特に、送り速度や回転速度を適宜調整することが、寸法精度を高めるポイントとなります。
高面粗度(鏡面加工)
高面粗度、つまり鏡面加工を実現するためには、いくつかの要点に注意する必要があります。まず、研削ホイールとワークの接触状態を正確に保つことが重要です。次に、研削ホイールの適自動ドレッシングを行い、常に鋭い切れ味を維持することも必要です。
加えて、冷却液の噴射角度と量を調整することで、ワーク表面に熱がこもらないようにすることが重要です。こうすることで、高面粗度の仕上がりを得ることができます。
円筒研磨(研削)のトラブルシューティング
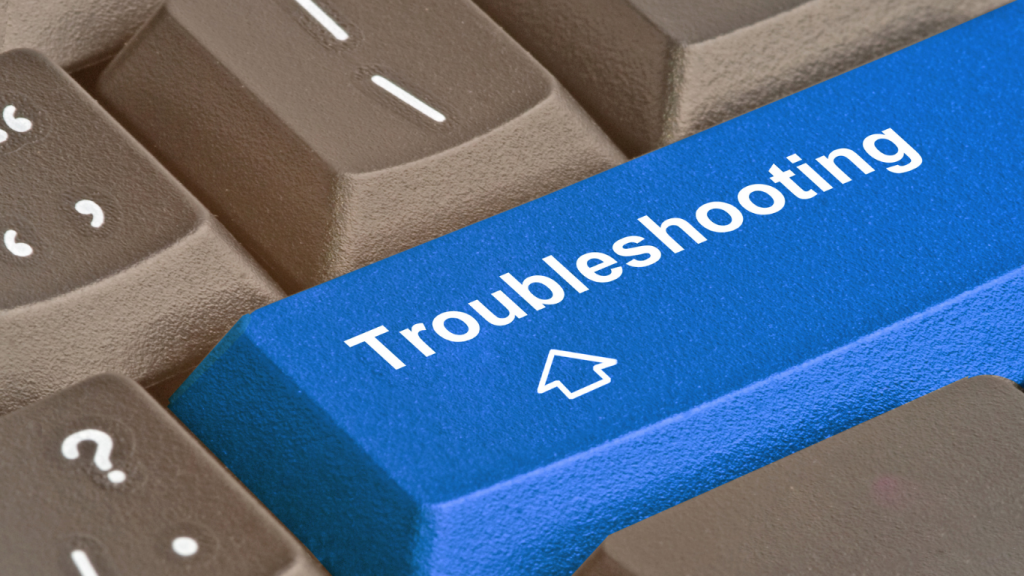
円筒研磨(研削)のトラブルシューティングでは、機械的な問題やプロセスの不具合が発生することがあります。以下にいくつかの一般的な問題とその解決策を示します:
- 仕上がりが不均一:
- 原因: 砥石の摩耗が不均一か、または機械のセットアップが不適切である可能性があります。
- 対策: 砥石の交換や再ドレッシング(形状修正)を行い、機械のセットアップを再確認します。
- 加工精度が低い:
- 原因: 芯出しの誤りや砥石の不適切な選定、または冷却液の不足が考えられます。
- 対策: 芯出しを正確に行い、砥石と冷却液を適切なものに交換してください。
- 加工中の振動:
- 原因: 機械の固定不足や、工作物の支持が不十分なことが原因で振動が生じることがあります。
- 対策: 機械の安定性を向上させ、工作物の固定方法を見直し、必要に応じて支持方法を改善します。
- 異常な砥石の摩耗:
- 原因: 砥石の硬度が不適切であるか、加工条件が適切でない可能性があります。
- 対策: 砥石の材質や硬度を見直し、加工条件を最適化します。
- 表面に傷がつく:
- 原因: 砥石が汚れているか、工作物に異物が付着している可能性があります。
- 対策: 砥石を清潔に保ち、工作物の表面を清掃する。必要に応じて砥石をドレッシングします。
トラブルの原因は多岐にわたるため、問題が継続する場合は専門の技術者に相談することも検討してください。これらの基本的なチェックと対策を行うことで、多くの問題は初期段階で解決可能です。
まとめ
円筒研磨(研削)は、その精密な技術が多岐にわたる産業で必要とされています。この技術により、部品の寸法精度を極めて高く保つことができ、それによって製品全体の性能を向上させることが可能です。
しかし、その実施には高度な技術と正確な設備の維持が求められるため、日々の操作とメンテナンスが非常に重要です。技術の進歩により、より効率的で精密な方法が開発され続けていますが、それに伴う課題もあります。
お問い合わせ
弊社製品、加工についてのお問い合わせは、こちらで受付しております。
各部門のスペシャリストが、ご質問にお応えします。
電話
0574-54-2231
(平日 8:15~17:15)
FAX
0574-54-2235