- 2025/02/26
-
フライス加工とは?旋盤との違い・種類・使い方まで解説
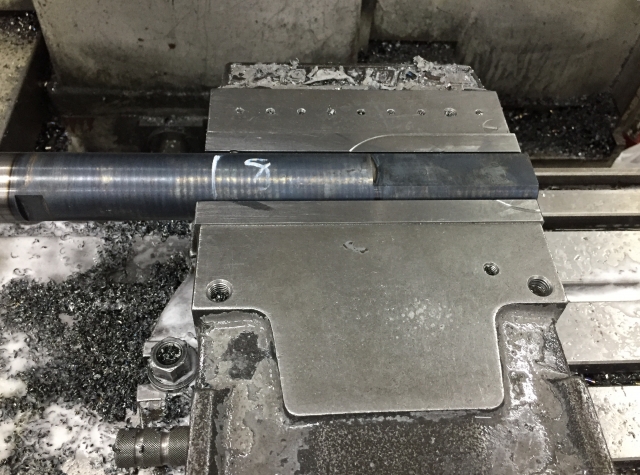
ものづくりの現場では、部品や製品の形状を精密に整えるためにさまざまな加工技術が活用されています。その中でも、フライス加工は金属や樹脂の切削に欠かせない方法のひとつです。専用の機械を使い、刃物を回転させながら素材を削り出すことで、高精度な仕上がりを実現できます。
一方で、フライス加工とよく比較される技術に旋盤加工があります。それぞれの加工法には異なる特徴があり、用途に応じて適切に使い分けることが大切です。本記事では、フライス加工の基本的な仕組みから旋盤との違い、使用する工具や具体的な加工方法まで、詳しく解説します。初心者から実務に携わる方まで役立つ情報をまとめていますので、ぜひ参考にしてみてください。
フライス加工とは?
ここでは、フライス加工の基本の仕組みと特徴を紹介します。
フライス加工の概要
フライス加工とは、フライス盤と呼ばれる工作機械を使用し、回転する刃物で金属や樹脂などの素材を削る加工方法のことです。切削工具を主軸に取り付けて高速回転させながら、ワーク(加工対象)を移動させることで、精密な形状を作り出します。
フライス盤は、平面や溝、曲面の加工を得意としており、自動車部品や航空機部品、金型の製造など、さまざまな産業で活用されています。手作業では実現が難しい高精度な仕上げを可能にし、CNC(コンピューター数値制御)を組み合わせることで、より複雑な形状の加工も行えます。
フライス加工は、旋盤加工とは異なり、素材を固定したまま刃物が回転する点が特徴です。これにより、直線的な削り出しはもちろん、湾曲した形状や特殊な角度の加工も柔軟に対応できます。
フライス加工の仕組み
フライス加工では、主軸に取り付けた刃物を回転させ、その回転運動を利用してワークを削ります。主軸の回転速度や送り速度、切削工具の種類を適切に調整することで、仕上がりの精度や表面の滑らかさをコントロールできます。
加工の基本的な形態として、直線加工・曲線加工・斜め加工があります。それぞれの特徴を詳しく見ていきましょう。
① 直線加工
フライス加工の基本的な形態で、ワークを固定し、刃物を一定の速度で移動させながら直線的に削り出します。平面を均一に仕上げる用途が多く、機械部品のベースとなるプレートやシャーシの加工などに用いられます。
② 曲線加工
特殊なエンドミルやボールエンドミルを使用し、ワークの曲線部分を滑らかに削る加工方法です。カムシャフトやギア部品など、複雑な形状を必要とする製品の製造に適しています。CNCフライス盤を活用することで、細かいデザインや立体的な加工も可能になります。
② 斜め加工
ワークに対して一定の角度をつけながら削る加工方法で、テーパーカットや斜めに溝を入れる際に使用されます。特殊な角度を持つ部品や、滑らかな接合面が求められる製品の製造に役立ちます。五軸CNCフライス盤を用いることで、より複雑な角度や曲面の加工も精密に行えます。
このように、フライス加工は刃物の回転方向や送りの調整によって多彩な加工が可能であり、さまざまな業界で活躍しています。適切な工具選びや加工条件の設定によって、求める精度や仕上がりを実現できます。
フライスと旋盤の違いとは?
ものづくりの現場では、金属や樹脂などの素材を削る加工方法として旋盤加工とフライス加工が広く使われています。どちらも精密な加工を施すための技術ですが、加工対象や削り方に大きな違いがあります。
旋盤加工とは
旋盤加工は、円筒形の素材を回転させながら刃物(バイト)を当てて削る加工方法です。主に金属部品の外径加工や内径加工、溝加工、ねじ切りなどを行う際に用いられます。旋盤には手動で操作する汎用旋盤と、プログラム制御で自動加工を行うNC旋盤があります。
旋盤加工の特徴は、円形の部品を高精度で仕上げられる点にあります。例えば、シャフト、軸受け、パイプのような部品は、旋盤加工を用いることで滑らかで均一な表面を実現できます。また、ねじ切りやテーパー加工(円錐形状)にも対応できるため、回転部品の製造には欠かせない技術です。
フライス加工と旋盤加工の違い
フライス加工と旋盤加工の大きな違いは、「どちらを回転させるか」という点です。
- 旋盤加工 → ワーク(素材)が回転し、固定された刃物が削る
- フライス加工 → 刃物が回転し、ワークを移動させながら削る
旋盤は円筒形の部品を作るのに適しているのに対し、フライス加工は平面や溝、複雑な形状の加工が可能です。これにより、それぞれの加工方法を適切に選ぶことが大切です。
マシニングセンターとフライス盤の違いについては、「マシニングとフライスの違いとは?加工の特徴と使い分けを解説」の記事を参考にしてください。
フライス加工と旋盤加工の使い分け
旋盤加工は円筒形状の部品を作るのに適しています。例えば、自動車のエンジンシャフトやバイクのホイールハブのような回転対称の部品を精密に仕上げる際には、旋盤が欠かせません。旋盤では、外径・内径の加工だけでなく、穴あけやねじ切りなどの工程も行えます。
一方で、フライス加工は平面の削り出しや、ワークに溝や角度をつけた加工を施すのに適しています。例えば、金型や機械のベースプレート、歯車の溝などはフライス加工が得意とする領域です。さらに、CNCフライス盤を活用すれば、立体的な形状や斜め加工も高精度で実現できます。
加工方法 | 特徴 | 適した用途 |
旋盤加工 | 素材を回転させて削る | 円筒形の部品、シャフト、ねじ切り、軸受け |
フライス加工 | 回転する刃物で削る | 平面加工、溝加工、複雑な形状の切削 |
フライス加工と旋盤加工を組み合わせるケース
実際の製造現場では、フライス加工と旋盤加工を組み合わせて使うケースが多くあります。例えば、エンジン部品のように一部が円筒形で、一部に溝や段差がある場合は、まず旋盤で円筒部分を加工し、その後フライス盤で溝や穴を削るという流れになります。
また、フライス盤に回転軸を追加した複合加工機を使用すれば、一台で旋盤加工とフライス加工を連携させることも可能です。これにより、加工精度を向上させながら、作業効率を大幅にアップできます。
このように、旋盤加工とフライス加工はそれぞれ異なる役割を持ちながらも、製造の現場では両者を組み合わせることで、より高度な部品加工が実現されています。加工の目的や素材の形状に応じて、適切な方法を選ぶことが大切です。
フライス加工の種類
ここでは、フライス加工の種類と特徴を紹介します。
主なフライス加工の分類
フライス加工にはいくつかの種類があり、使用するフライス盤の種類や加工方法によって分類されます。主に「立フライス加工」「横フライス加工」「CNCフライス加工」の3つが代表的な加工方式として知られています。それぞれの特徴を詳しく見ていきましょう。
立フライス加工(主軸が垂直のフライス盤を使用)
立フライス加工とは、主軸が垂直に配置された立フライス盤を使用する加工方法です。刃物が回転しながら上下方向に切削を行うため、平面加工や溝加工、穴あけ加工など幅広い用途に対応できます。
この加工法は、一般的なフライス加工の中でも一番多く使用されており、金型加工や機械部品の製造、試作開発などで活躍しています。特にCNC制御を導入した立フライス盤では、複雑な形状の加工も高精度で行うことが可能です。
横フライス加工(主軸が水平のフライス盤を使用)
横フライス加工では、主軸が水平に設置された横フライス盤を使用し、長尺のワークや大きな部品の加工に適しています。刃物が水平方向に回転することで、より強力な切削が可能となり、頑丈な金属部品の大量生産にも向いています。
この方法は、大きなワークの側面を削る作業や、厚みのある部材の加工に使われることが多く、航空機部品や自動車のシャーシ部品などの製造に活用されています。
CNCフライス加工(自動制御による高精度加工)
CNCフライス加工は、コンピューター数値制御(CNC)を利用し、精密なプログラムに基づいて自動で加工を行う技術です。従来の手動フライス加工に比べて、高精度・高効率な生産が可能となり、特に精密部品や複雑な三次元形状の加工に適しています。
CNCフライス盤を用いることで、短時間で均一な品質の部品を大量生産できるため、自動車・医療機器・電子部品などの産業で広く利用されています。また、斜め加工や自由曲面の成形も可能で、従来の手動操作では難しかった高度な加工にも対応できます。
具体的な加工方法
フライス加工では、目的に応じたさまざまな加工方法が存在します。代表的なものとして、「平面加工」「溝加工」「斜め加工」があり、それぞれの用途や特徴を理解することで、適切な加工を選択できます。
平面加工(表面を均一に削る)
平面加工は、フライス加工の中でも一番基本的な方法であり、ワークの表面を均一な厚みに削ることを目的とします。主にフェイスミルカッターを使用し、滑らかで精度の高い仕上げを実現できます。
この加工法は、金属板の表面仕上げや、機械部品の基礎となる部分の加工に適しており、特にフラットな基盤を必要とする部品の製造において大切な役割を果たします。また、表面粗さを調整することで、高精度な仕上げや塗装前の処理としても利用されます。
溝加工(部品の溝やキー溝の作成)
溝加工は、ワークの表面に特定の形状の溝を掘る加工方法であり、主にエンドミルを使用します。機械部品や工具に使用される「キー溝」や「T字溝」「V字溝」など、さまざまな形状の溝を加工できます。
この加工法は、ギア部品やシャフトの固定溝、金型のガイドレールの作成などに活用され、機械部品の組み立てや動作に不可欠な要素となっています。特にCNCフライス盤を用いることで、複雑な溝形状や精密な加工が可能となり、製造業における幅広い用途で利用されています。
斜め加工(角度をつけた切削)
斜め加工は、ワークに対して一定の角度をつけて切削を行う加工方法で、通常の平面加工とは異なり、斜面や角度を持つ部品の成形に適しています。
この方法では、傾斜のついた部品や、テーパー(角度が徐々に変化する形状)の加工に用いられます。例えば、金型のエッジ部分や特殊な機械部品の製造において、斜め加工が求められるケースが多くあります。CNCフライス盤を使用すれば、多軸制御による正確な角度調整が可能となり、より複雑な形状の加工も実現できます。
フライス盤の基本操作
フライス盤を適切に操作することで、精度の高い加工を実現できます。加工ミスや工具の破損を防ぐためには、正しい手順で操作を行うことが大切です。ここでは、フライス盤の基本的な使い方や安全対策について詳しく解説します。
フライス盤の操作手順
フライス加工を行う際には、まずワーク(加工対象)をしっかりと固定し、刃物を適切に取り付けた上で、切削速度や送り速度を調整する必要があります。これらの工程を順番に見ていきましょう。
ワーク(加工対象)の固定方法
ワークの固定は、加工精度を左右する大切な工程です。固定が甘いと、切削時の振動や工具の食い込みによって、寸法のズレやバリの発生、さらには工具の破損につながる可能性があります。
固定方法の基本
- バイスを使用する:金属製のバイス(万力)を使い、ワークをしっかりと固定する。ワークの大きさや形状に応じて適切なバイスを選ぶ。
- 治具を活用する:複雑な形状のワークや、大量生産時には専用の治具を用いることで、加工の精度と作業効率を向上させる。
- クランプで押さえる:バイスに挟めない大きなワークは、Tスロット付きのテーブルにボルトとクランプを使って固定する。
固定後は、ワークが動かないか手で軽く押して確認し、必要に応じて締め直すことが大切です。また、加工中に発生する応力を考慮し、ワークの向きや支点を適切に設定することで、安定した切削が可能になります。
刃物の取り付けと切削速度の調整
フライス盤で加工を行う際には、使用する工具(エンドミル・フェイスミル・ボールエンドミルなど)を主軸にしっかりと取り付け、適切な切削速度を設定することが大切です。
刃物の取り付け手順
- コレットやチャックを確認する:工具のシャンク径に合ったコレットを選び、しっかりと装着する。
- 工具を主軸に固定する:工具を主軸のチャックに差し込み、レンチを使ってしっかりと締める。締め付けが不十分だと、加工中に工具が抜ける恐れがある。
- 振れを確認する:工具が正しく取り付けられているか、空回転させて振れがないか確認する。
切削速度の設定
切削速度は、使用する刃物の種類・素材の硬さ・加工方法によって値が異なります。基本的には以下の要素を考慮して調整します。
- 刃物の直径が大きいほど、回転数を低く設定する
- ワークの材質が硬いほど、回転数を低めにし、送り速度をゆっくりにする
- 切削条件を効率化するために、メーカーの推奨値を参考にする
適切な切削速度を選ぶことで、工具の寿命を延ばし、加工精度を向上できます。
切削時の送り速度とクーラントの使用
送り速度とは、工具がワークに対して移動する速度のことで、送り速度が適切でないと、仕上がりの精度や工具の消耗に影響を与えます。
- 速すぎる場合 → 工具に過剰な負荷がかかり、刃こぼれや摩耗が早まる
- 遅すぎる場合 → 加工時間が長くなり、効率が低下する
また、加工中に発生する摩擦熱を抑えるために、クーラント(切削油や水溶性クーラント)を使用することで、工具の寿命を延ばし、仕上がりの品質を向上できます。
クーラントの効果
- 切削熱を抑え、工具の摩耗を軽減
- 切りくずの排出を促進し、加工面の仕上がりを向上
- 加工時の発熱によるワークの変形を防止
適切な送り速度とクーラントの使用により、加工精度を保ちながら効率的な作業が可能になります。
フライス加工の安全対策
フライス加工を安全に行うためには、作業環境を整え、適切な保護具を着用することが大切です。また、加工中の異常を素早く察知し、適切な対処を行うことで、事故や工具の破損を防げます。
作業時の注意点(手袋NG、保護メガネ着用など)
フライス盤を使用する際には、安全対策を徹底することが求められます。特に以下のポイントに注意しましょう。
- 手袋は着用しない:回転する刃物に手袋が巻き込まれる危険があるため、素手で作業を行う。
- 保護メガネの着用:切りくずが飛散するため、目を保護するためのゴーグルやメガネを装着する。
- 長髪は束ねる:髪の毛が巻き込まれるリスクを防ぐため、作業時は結ぶか帽子をかぶる。
- 作業服を適切に着用:ダボついた服は機械に引き込まれる恐れがあるため、作業に適した服装を選ぶ。
これらの安全対策を守ることで、作業時の事故を未然に防げます。
加工中の異常音や振動の確認
フライス加工を行っている途中に、通常とは異なる音や振動を感じた場合は、すぐに作業を中断し、原因を確認することが大切です。
- 異常な音(高音や異常な金属音) → 刃物の摩耗やワークの固定不良の可能性
- 過度な振動 → ワークの固定が不十分、または主軸のブレによるもの
- 切削面が荒れる → 刃物の摩耗、切削速度が合っていない可能性
異常を感じた際は、フライス盤の電源を切り、安全を確認した上で工具やワークの状態をチェックすることが必要です。早期対応を行うことで、工具の破損や作業中のトラブルを防げます。
フライス加工に使用する工具
フライス加工における工具と刃物は、加工する部品や求められる精度に合わせて選定されます。使用する工具や刃物の種類によって、加工の効率や仕上がりの精度が大きく異なるため、これらの選定は大切です。ここでは、代表的なフライス加工に使用される刃物や工具について、具体的に説明します。
フライス加工で使用される刃物の種類
フライス加工にはさまざまな刃物が使用され、それぞれに特徴や適した加工方法があります。主要な刃物について詳しく見ていきましょう。
エンドミル(主に溝加工や曲線加工)
エンドミルは、回転する刃物の先端が切削を行うタイプの工具です。主に溝加工や曲線加工に使用され、複雑な形状や精密な切削を行う際に欠かせない刃物です。エンドミルは様々な形状やサイズがあり、2枚刃、4枚刃、6枚刃などの種類が存在します。それぞれの刃数によって、切削力や仕上げ面の滑らかさが変わります。
エンドミルは平面加工だけでなく、角度をつけた切削や斜め切削など、自由度が高い加工が可能です。特に、細かい溝や複雑な曲線を作る際に多く使用されます。
フェイスミル(平面加工に適した工具)
フェイスミルは、工具の前面に多数の刃が配置されているタイプのフライス刃物です。主に平面加工に用いられ、大面積の加工を行う際に適しています。フェイスミルの刃物は、大きな切削面を持ち、強力な切削能力を発揮します。これにより、金属や硬い素材を素早く削ることができ、効率的な加工が可能です。
フェイスミルは、加工対象の大きな面を均一に削るため、製造業の多くの現場で利用されています。また、仕上がりの精度を向上させるため、フェイスミルには可変角度の刃を持つものもあります。
ボールエンドミル(曲面加工や3D形状の加工)
ボールエンドミルは、先端が球状になっている刃物で、主に曲面加工や3D形状の加工に使用されます。ワークの曲面や複雑な立体形状を精密に削るための工具で、切削面が滑らかであるため、特に3D形状の部品の加工におすすめです。
ボールエンドミルは、立体的な加工が可能で、金型や模具の製造などに広く利用されています。また、CNCフライス盤と組み合わせることで、高精度な加工を行うことが可能です。
フライス加工の工具(治具・バイスなど)
フライス加工で使用される工具は、刃物だけではありません。加工の効率や精度を高めるために、さまざまな補助工具や治具も重要な役割を担います。ここでは、代表的な工具について説明します。
バイス(ワークの固定具)
バイスは、ワークをしっかりと固定するための工具です。フライス盤に取り付けて使用し、ワークを一定の位置に保持する役割を果たします。バイスは金属やプラスチックなどの素材をしっかりと固定できるため、加工中にワークが動いて精度が落ちるのを防ぎます。
バイスには、上下可動式のものや、可動範囲が広いタイプなど、用途に応じたさまざまな種類があります。また、特定の形状に対応するために、ワークに合わせた特注のバイスや治具を使用することもあります。
クーラント(刃物の冷却と潤滑)
フライス加工時には、刃物やワークが高温になるため、クーラントの使用が不可欠です。クーラントは、切削中の摩擦熱を冷却し、刃物の寿命を延ばすだけでなく、切削面を滑らかに仕上げる役割も果たします。
クーラントは、水溶性液体や油性液体などがあり、加工の種類や素材に応じて使い分けが必要です。例えば、アルミや銅などの柔らかい金属を加工する場合は水溶性のクーラントがよく使用され、硬い金属を削る場合は油性のクーラントが使用されます。
フライスとドリルの違いとは?
フライス加工とドリル加工は、どちらも切削加工の一種ですが、それぞれに異なる特性があります。ここでは、フライスとドリルの基本的な違いと、フライス盤を使ったドリル加工の応用について詳しく解説します。
フライス加工は横方向の切削、ドリルは垂直方向の穴あけ
フライス加工は、刃物が回転しながらワークを横方向に削る加工方法であり、平面や溝、曲線を加工するために使用されます。一方、ドリルは、垂直方向に回転しながらワークに穴をあけるための工具です。
- フライス加工 → 横方向の切削
- ドリル加工 → 垂直方向に穴をあける
そのため、フライス盤は多様な形状を削り出すために用いられ、ドリルは主に穴あけ作業に使用されます。
フライス盤を使ったドリル加工の応用
フライス盤を使ってドリル加工を行うことも可能で、フライス盤にはドリルチャックを取り付けることで、精密な穴あけが可能です。ドリル加工は、単一の直線的な切削が必要な場面で有効ですが、フライス盤の回転軸を調整することで、より高精度な穴あけや深穴加工も行えます。
さらに、フライス盤を使ったドリル加工では、穴の形状や精度、深さの調整が容易であり、特に複数の異なる径の穴あけを同時に行いたい場合に便利です。
フライス加工の主軸と精度の関係
フライス加工の精度は、使用する工具や切削条件だけでなく、主軸の特性や駆動方式にも大きく左右されます。主軸は刃物を取り付ける部分であり、その剛性や駆動方式によって加工の安定性が決まります。ここでは、主軸の種類とその影響、加工精度を向上させるためのポイントについて詳しく解説します。
主軸の役割と種類
主軸は、フライス盤の中心的な部品であり、刃物を回転させることでワークを切削する役割を果たします。主軸の回転速度や剛性が適切でないと、加工精度の低下や工具の摩耗が早まる原因となるため、用途に応じた主軸の選定が大切です。
ベルト駆動方式 vs. ギア駆動方式
フライス盤の主軸には、ベルト駆動方式とギア駆動方式の2種類があります。それぞれの特徴と適した用途を見ていきましょう。
ベルト駆動方式
- 特徴:ベルトを介してモーターの動力を主軸に伝える方式
- メリット:
- 騒音が少なく、比較的静かに動作する
- ギアの摩耗がないため、長期間安定した動作が可能
- 振動が少なく、表面仕上げの品質が向上しやすい
- デメリット:
- 高トルクの切削には不向き(重切削時にベルトが滑ることがある)
- 加工負荷が高い場合、ベルトが劣化しやすい
ギア駆動方式
- 特徴:金属製のギアを使ってモーターの動力を主軸に直接伝える方式
- メリット:
- 強いトルクを維持できるため、重切削や硬い金属の加工に適している
- 高負荷の加工でも安定した回転が可能
- 長時間の加工に耐えられる耐久性の高さ
- デメリット:
- ギアの摩耗により、定期的なメンテナンスが必要
- 騒音が大きく、振動が発生しやすい
- 精密加工時に、微細なブレが影響を与えることがある
選択のポイント
- 高精度な仕上げを求める場合 → ベルト駆動方式が適している
- 強力な切削力を必要とする場合 → ギア駆動方式が有利
主軸の剛性と加工精度への影響
主軸の剛性(剛性とは、外部からの力に対する変形のしにくさ)は、加工の安定性と精度を決定づける大切な要素です。
- 主軸の剛性が高い → 切削時の振動を抑え、寸法精度を向上させる
- 主軸の剛性が低い → 加工中に刃物がたわみ、仕上がりが不均一になる可能性がある
主軸の剛性が求められるのは、特に重切削や深穴加工、高精度な仕上げが必要な場合です。剛性を確保するためには、主軸ベアリングの精度や適切な締め付けトルクの管理が大切になります。また、主軸のメンテナンスを定期的に行うことで、摩耗を防ぎ、長期的な安定性を保つことが可能です。
加工精度を高めるためのポイント
高精度なフライス加工を実現するためには、適切な工具の選定や、振動を抑えるための対策が必要です。ここでは、加工精度を向上させるための具体的なポイントについて解説します。
正しい工具の選定と切削条件の調整
加工の精度を高めるためには、適切な工具の選定と正しい切削条件の設定が欠かせません。
工具の選定
- 加工する素材に適した刃物を選ぶ(例えば、アルミ加工にはアルミ専用のエンドミル、硬い金属には超硬工具を使用)
- 切削する形状に応じて工具の種類を変更(平面加工にはフェイスミル、曲面加工にはボールエンドミルなど)
- 工具の摩耗を定期的にチェックし、早めに交換(摩耗した刃物を使用すると、加工精度が低下し、工具寿命も縮む)
切削条件の調整
- 切削速度と送り速度のバランスを効率化
- 速度が速すぎるとバリが発生しやすく、遅すぎると加工時間が長くなる
- 回転数を適切に設定(ワークの材質や工具の種類に応じた適正なRPMを選択)
- 切削深さと送り量を慎重に調整(無理な切削は工具の摩耗を早め、加工面の精度を損なう)
ワークの固定方法と振動対策
ワークの固定が不十分だと、加工中に微妙なズレが生じ、寸法精度が大きく狂う原因となります。しっかりと固定することが、高精度な加工を実現するカギとなります。
ワークの固定方法
- バイスを使用してしっかりと固定する(ワークの形状に合ったバイスを選ぶ)
- Tスロットや治具を活用する(大型のワークはテーブルに直接固定することで、ズレを防止)
- クランプの締め付けトルクを均一にする(片側だけ強く締めるとワークが歪み、加工誤差が発生する)
振動対策
- 低剛性の工具は避ける(剛性の低いエンドミルはたわみやすく、加工精度が落ちる)
- 主軸の回転数を適切に調整する(共振が発生しない回転数を選ぶ)
- 切削中にクーラントを適切に使用する(摩擦熱によるワークの膨張を防ぎ、安定した加工を実現)
振動を抑え、ワークをしっかりと固定することで、より高精度な仕上がりを実現し、工具の寿命も延ばすことが可能です。
フライス加工と表面粗さの関係
フライス加工では、加工条件によって仕上がりの表面粗さが大きく変わります。表面粗さは、部品の耐久性や摩擦係数に影響を与えるため、求められる精度に応じてより良い加工方法を選ぶことが大切です。ここでは、フライス加工における表面粗さの基本概念と、精度の高い仕上げを実現するためのポイントについて詳しく解説します。
表面粗さとは?
表面粗さとは、加工後のワーク表面の凹凸の程度を示す指標であり、数値が小さいほど滑らかな仕上がりを意味します。フライス加工では、使用する刃物の種類、切削速度、送り速度、加工方式によって表面の仕上がりが変わります。
加工方法別の表面仕上げの違い
- 荒加工(ラフカット):切削量が多く、送り速度も速いため、表面に大きな凹凸が残る
- 中仕上げ加工:送り速度を調整しながら加工することで、ある程度滑らかな仕上がりが得られる
- 仕上げ加工(ファインカット):切削深さを小さくし、送り速度を遅くすることで、極めて滑らかな表面を実現
表面仕上げの粗さは、Ra(算術平均粗さ)やRz(最大高さ粗さ)などの数値で表され、精密部品や金型製作では、求められる表面粗さの基準が厳しくなる傾向があります。
粗さをコントロールするための切削条件
表面粗さを適切にコントロールするためには、加工時の切削条件を効率化することが不可欠です。
表面粗さを向上させるためのポイント
- 切削速度を上げる:回転数を高めることで、切削時の刃物の衝撃を軽減し、滑らかな表面が得られる
- 送り速度を適切に調整する:送り速度が速すぎると加工面に波形が発生しやすく、遅すぎると切削面が均一になりにくい
- 刃物の剛性を高める:剛性の低い刃物は微細な振動が発生し、表面に加工跡が残るため、剛性の高いエンドミルやフェイスミルを選択する
- 切削液を適切に使用する:クーラントを適切に供給することで、摩擦熱を抑え、切削面の品質を向上させる
これらの要素を適切に調整することで、フライス加工の表面仕上げの精度を大幅に向上させることが可能です。
高精度な表面仕上げを実現するためのポイント
フライス加工において、高精度な仕上がりを得るためには、送り速度や回転数の効率化、仕上げ加工に適した刃物の選定が不可欠です。
送り速度と回転数の調整
送り速度と回転数は、加工の品質や表面の滑らかさを左右する大切な要素です。適切な設定を行うことで、表面粗さをより良い状態にコントロールできます。
送り速度の調整
- 速すぎる場合:切削面に波状の加工跡ができやすく、表面の粗さが増す
- 遅すぎる場合:過剰な摩擦が発生し、刃物の摩耗が早まることがある
回転数の調整
- 回転数を高める:切削点が細かくなり、表面の滑らかさが向上する
- 回転数が低すぎる:切削点が荒くなり、加工面が粗くなる
理想的な組み合わせを見つけるためには、加工するワークの材質や刃物の種類に応じた適正値を設定することが大切です。特に、CNCフライス盤では、数値制御による効率化が可能であり、より高精度な加工が実現できます。
仕上げ加工時の刃物選び
仕上げ加工の品質を高めるためには、用途に応じたより良い刃物を選定することが大切です。
仕上げ加工に適した刃物の選び方
- 刃数の多いエンドミルを使用(多刃タイプのエンドミルは、より細かく滑らかな仕上がりが可能)
- ボールエンドミルを活用(曲面やR形状の仕上げには、ボールエンドミルが適している)
- コーティングされた刃物を使用(耐摩耗性の高いコーティング刃物は、仕上げ精度を向上させる)
- 超硬エンドミルを選択(高硬度のワークを加工する際には、耐久性のある超硬工具がおすすめ)
また、刃物の摩耗状態を定期的にチェックし、必要に応じて交換することで、常に安定した表面仕上げを維持できます。
まとめ
フライス加工は、金属や樹脂の加工において欠かせない技術の一つです。主軸の回転を利用して素材を精密に削ることで、平面や溝、斜め加工など幅広い用途に対応できます。また、旋盤加工との違いを理解し、適切に使い分けることで、より効率的で高精度な加工を実現することが可能です。
加工精度を向上させるためには、使用する刃物や工具の選定、適切な切削条件の設定が大切です。特に、主軸の剛性や回転方式、送り速度の調整が、仕上がりの品質に大きく影響します。さらに、表面粗さを効率化することで、製品の耐久性や性能を向上できます。
弊社では、新しい精密加工機械を導入し、お客様の求める加工品質に対応できる環境を整えております。設備の選定から技術的なサポートまで、一貫してご提案できる体制を構築しており、新規導入をご検討の際には、専門のスタッフがより良い機種や加工方法についてアドバイスいたします。導入後の運用についても丁寧にサポートいたしますので、設備の導入や加工精度の向上に関するご相談がございましたら、お気軽にお問い合わせください。
お問い合わせ
弊社製品、加工についてのお問い合わせは、こちらで受付しております。
各部門のスペシャリストが、ご質問にお応えします。
電話
0574-54-2231
(平日 8:15~17:15)
FAX
0574-54-2235