- 2025/03/03
-
マシニング作業での切削条件の設定方法を解説!
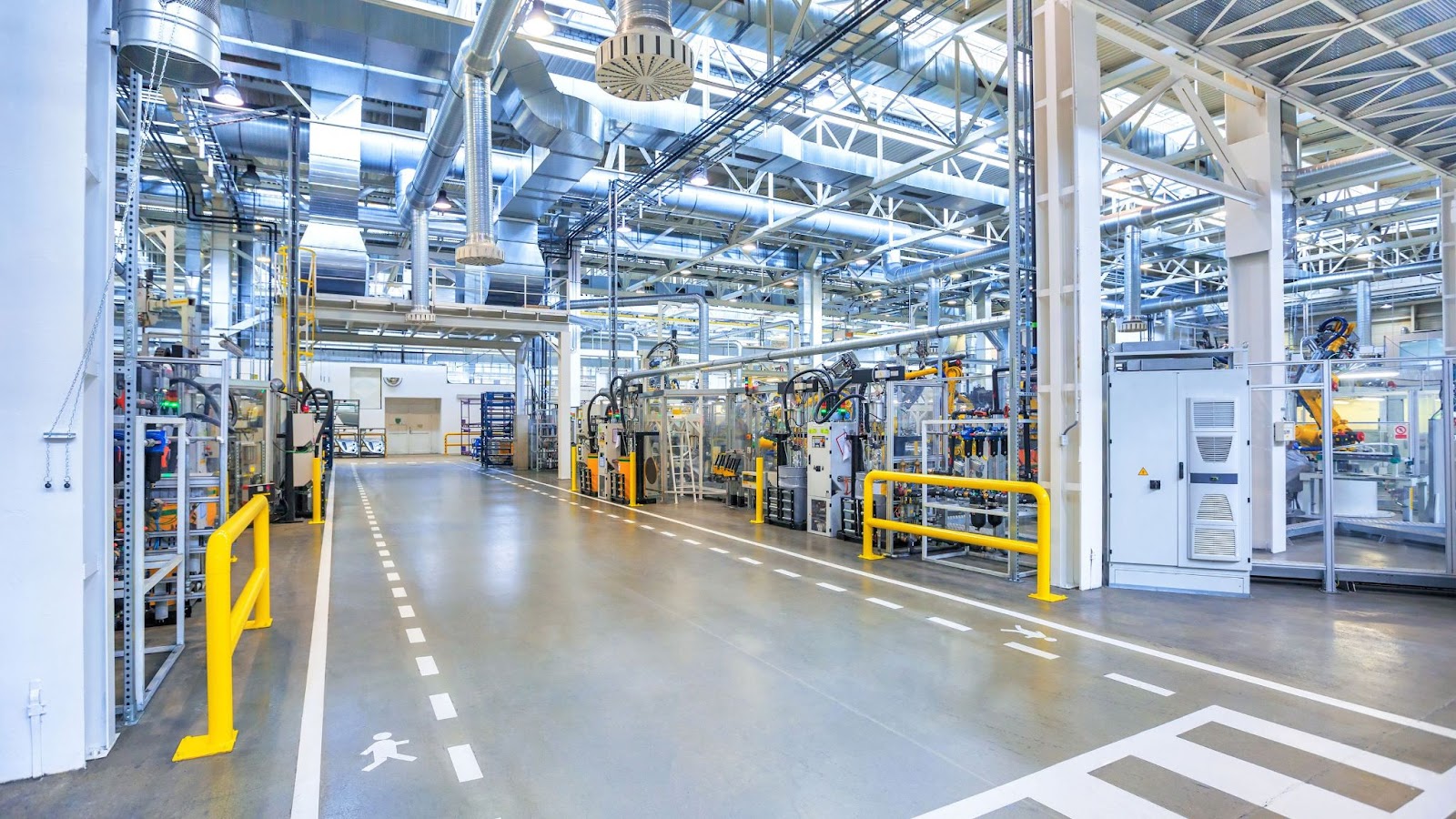
マシニングは、精密部品の製造に欠かせないプロセスです。正確な切削条件の設定と適切な工具選定は、加工の精度や生産性、さらには安全性に大きく影響します。
今回は、マシニングの基礎から切削条件の設定方法、工具選定と寿命延長のポイント、さらには最新技術の活用方法まで、押さえておきたいポイントを解説します。
マシニングとは?
マシニングとは、金属やプラスチックなどの材料を削り、設計図通りの形状に加工する技術です。近年は、コンピューター制御(CNC)による高精度な加工が一般的で、自動車、航空機、電子機器など幅広い産業で利用されています。
マシニングセンタの種類
マシニングセンタは主に「垂直型」と「水平型」に分類され、さらに5軸加工機など複雑な加工が可能な機種も登場しています。
種類 | 特徴 |
垂直型 | 型部品の加工に適し、主軸が垂直に配置する |
水平型 | 大型部品や高生産性が求められる現場で使用され、主軸が水平に配置される・最近では対話型ソフトウェアを用いた操作モデルも増加しており、操作性が向上している |
マシニング作業の流れ
マシニング作業は、以下のステップで進行します。
- 設計図の確認とプログラム作成
設計図をもとに、加工対象の形状、順序、使用する工具などの詳細を含む加工プログラム(Gコードなど)を作成します。
- 材料のセットと工具の取り付け
作成したプログラムに合わせ、マシニングセンタに材料をセットし、適切な工具を取り付けます。工具の選定と正確な取り付けは、加工精度と効率に直結する大切な工程です。
- 試運転による確認
プログラムを入力後、試運転を実施し、設定通りに加工が進むかを確認します。不具合があれば、この段階で調整を行います。
- 本運転での加工実施
試運転で問題が解消されたら、本運転に移行し、実際の加工を開始します。
- 加工後の検査と仕上げ
加工が完了したら、製品の寸法、表面仕上げ、その他の品質チェックを実施し、最終製品としての完成度を確認します。
切削条件とは?
切削条件とは、工作機械で材料を削る際に設定するパラメータの総称です。主なパラメータとして、切削速度、送り速度、切込み量などが挙げられます。
これらは材料の種類、工具の特性、機械の性能、さらには冷却や環境条件など、さまざまな要因を考慮して最適化しなければなりません。
切削速度と送り速度の違い
切削速度が高すぎると工具の摩耗が早くなり、低すぎると加工時間が延びるため、適切なバランスが重要です。
- 切削速度
工具の刃先が材料に当たる速さ(m/min)。工具の回転数と外径に基づいて計算され、材料の硬度や特性に合わせて設定します。
- 送り速度
工具が材料内を進む速度(mm/min)。加工精度や仕上がりに大きく影響するため、最適なバランスが求められます。
材料別の切削条件
材料ごとに物理的特性が異なるため、切削条件も個別に調整が求められます。
金属材料
鉄鋼、アルミニウム、銅合金などでは、硬さや熱伝導性に応じた切削速度が設定されます。たとえば、硬い鉄鋼には低速、柔らかいアルミや銅には高速切削が推奨され、冷却液や切削油を使いましょう。
非金属材料
プラスチック、木材、セラミックスなどは、加工時の変形や熱影響を防ぐため、低速での切削や特殊な工具・冷却対策が欠かせません。切りくずの排出や刃先温度の管理にも注意が必要です。
複数材料の同時加工
異なる特性を持つ材料を組み合わせる場合、各材料の最適条件のバランスを取るため、工具の選定や切削速度、冷却方法の調整が求められます。
安全かつ効率的な条件設定のポイント
適切な切削条件は、加工精度と工具寿命の延長、さらに安全な作業環境の実現に直結します。設定時には以下の点に注意しましょう。
- 材料・工具・機械の仕様の確認
- 過去の実績やシミュレーション結果に基づいた条件設定
- 試運転での動作確認と記録、状況に応じた微調整
- クーラントや切削油の適切な選定と管理
切削工具の選定方法
切削工具の選定は、加工効率や仕上がり品質、工具コスト管理に直結する欠かせない工程です。素材の種類、加工方法、工具の材質・形状、使用環境などを総合的に考慮することが求められます。
工具の種類と特徴
切削工具には用途に応じた多くの種類があります。以下、主要な工具とその特徴を具体例とともに紹介します。
エンドミル
エンドミルは、フライス盤で平面加工や溝・輪郭加工に使用される工具です。直径6~12mm程度のものが一般的で、切削刃の数や形状により粗加工から仕上げ加工まで幅広く対応し、アルミや銅などの軽量金属加工で高い実績を持ちます。
用途 | フライス盤での平面加工、溝加工、輪郭加工に利用される |
特徴 | 切削刃の形状(ラジアルカッティングエッジの数や形状)により、粗加工用から仕上げ加工用まで幅広い用途に対応 |
具体例 | 直径6mm~12mmのエンドミルが、アルミや銅の加工で使用される |
ドリル
ドリルは、穴あけ加工専用の工具で、Ø3~Ø20mmのビットが存在します。先端のシャープな形状と特殊なコーティングにより、切りくずを効率的に排出し、穴精度を高める設計となっており、自動車や航空機部品の加工で重宝されています。
用途 | 穴あけ加工専用。自動車部品や航空機部品の穴あけ工程で広く用いられる |
特徴 | 先端のシャープさや、切削部のコーティングにより、穴あけ時の切りくず除去と穴精度を向上 |
具体例 | Ø3mm~Ø20mmのドリルビットがあり、スパイラル形状が切りくずの排出を促進 |
バイト
バイトは、旋盤加工で外径や内径の削り出しに使用され、特に円筒部品の仕上げに適しています。工具の形状や切削角度が多様に設計され、加工負荷に応じた最適な切削条件を実現するため、シャフトなどの精密部品加工で効果を発揮します。
用途 | 旋盤での外径加工や内径加工に使用。特に円筒状の部品の仕上げに適している |
特徴 | 切削角度や刃先の形状が多様で、切削負荷に合わせた最適な加工が可能 |
具体例 | 外径50mmのシャフト加工には、形状や角度が最適化されたバイトが採用される |
特殊工具(リーマ、タッピング工具など)
特殊工具は、穴の内径拡大やねじ切りなど特定用途に特化した工具です。航空機用の高精度タッピング工具などは、特殊コーティングや精密なバランス調整が施され、従来の工具では難しい高精度加工を可能にする設計が特徴です。
用途 | 穴の内径拡大やねじ切りなど、特定の加工に特化した工具 |
特徴 | 用途に応じた特殊設計により、従来の工具では困難な加工ができる |
具体例 | 航空機用の高精度タッピング工具は、特殊なコーティングと精密なバランス調整が施されている |
工具選定のポイント
工具選定のポイントは、加工する素材の特性を理解し、それに適した工具を選択することです。まず、素材の硬度や粘性、熱伝導性を考慮し、適切な工具材料を選びましょう。
素材の特性
加工対象の金属は、鋳鉄、アルミ、ステンレスなどで硬度や熱伝導性が異なります。たとえば、アルミは切削抵抗が低く超硬エンドミルで高速切削が可能ですが、鋳鉄は発熱が大きいため冷却液使用と耐熱性の工具が必須です。
工具形状とサイズ
部品の形状や加工精度に合わせ、工具の直径、刃数、切削角度などが重要です。微細加工では小径で高精度なエンドミルが好まれ、大型部品では強度や耐久性を重視した工具が選定されます。
耐久性とコスト
工具は長期的に使用することを前提に、耐摩耗性とコストパフォーマンスの両面を見極めることが求められます。初期投資が高くても、TiAlNコーティングなどを施した高耐久性工具を導入することで、交換頻度を減らし、結果的にコスト削減に繋がる場合があります。
コーティングの有無
工具のコーティングは摩擦熱の低減と耐摩耗性向上に寄与します。例えば、TiNやTiAlNコーティング工具は、ステンレス鋼や難削材の加工で工具摩耗を50%以上改善できる実績があり、品質維持に大きな効果があります。
工具寿命の延ばし方
工具は加工コストや生産性に直結する要となる存在です。長期間にわたり高い切削性能を維持するためには、適切な使用方法と日常的なメンテナンスが不可欠です。
適正な使用条件の遵守
工具メーカーが提示する最大切削速度(エンドミル600 m/min)や最適な送り速度(0.1~0.3 mm/tooth)を守ることが重要です。試運転やシミュレーションで最適な加工条件を見極め、過負荷運転を防ぎます。
定期的な清掃と点検
加工後は工具表面に付着した切りくずや油分を専用クリーナーで除去し、毎日の終業前に摩耗状態などを点検します。早めの交換や再研磨に取り組むことで、性能を安定させられます。
再研磨の実施
工具の刃先が鈍化した際には、専用の研磨装置で刃先を再生します。定期的な再研磨により、工具寿命を30~50%延長できるケースが報告されており、経済的かつ高品質な加工を実現する有効な手段です。
適切な保管
工具は湿度や温度変動の少ない環境で、専用ケースやラックに整理して保管することが望ましいです。工具専用の乾燥庫を利用することで、腐食や変形のリスクを低減し、長期間にわたり性能を維持できます。
切削条件を最適化するためのツールと技術
切削加工の効率を最大化し、品質を向上させるためには、適切なツールと技術の選択が欠かせません。
切削条件を最適化するためのツールとしては、CNCプログラムや対話型ソフトウェアが挙げられます。加工プロセスを自動化し、人為的なミスを減らすことが可能です。
また、最新の技術を利用することで、加工速度を上げながらも精度を保つことができ、製造コストの削減や製品の競争力向上に寄与します。
CNCプログラムの活用法
CNCプログラムは、工作機械を正確かつ効率的に動かすための命令を与える仕組みです。複雑な加工でも一貫して高精度に行えるのが特徴で、まずは加工する部品の設計図をもとにGコードやMコードを指示します。シミュレーションで問題がなければ、本番の加工へ移行します。
また、加工中に条件を変更したり、エラーを修正したりする場合でも、CNCプログラムなら柔軟に対応でき、リアルタイムで調整が可能です。こうした特性により、製造工程の信頼性と効率性が大幅に向上します。
対話型ソフトウェアの利点
対話型ソフトウェアは、操作のしやすさと柔軟性を兼ね備えており、初心者や小規模事業者にとって有力な選択肢です。ユーザーフレンドリーなインターフェースを持ち、プログラムの専門知識があまりなくても簡単に利用できます。
また、シミュレーション機能を活用すると、加工前の段階で問題点を洗い出しやすく、実際の作業をスムーズに進められます。リアルタイムでの設定変更や最適化も容易なため、作業環境を効率的に整えられるほか、データを一括管理できるのも大きな利点です。このように、情報共有やトレーサビリティの向上にも貢献する点が評価されています。
最新技術による効率化
切削加工の効率化には、最先端の技術を取り入れることが欠かせません。たとえばAIを活用した自動化技術では、加工条件をリアルタイムで最適化し、品質を一定に保ちながら生産速度を上げることができます。
IoT技術を組み合わせた状態監視システムを導入すれば、機械の稼働状況を常時把握し、故障の予兆を早期に検知することでダウンタイムを最小限に抑えられます。
さらに、工具の耐久性や切削速度を向上させる材料技術の進歩も、トータルコストの削減に大きく寄与します。これらの技術革新を適切に導入することで、製品の品質と生産性が向上し、企業の競争力強化につながります。
トラブルシューティングと予防策
機械加工ではトラブルの発生を完全に避けるのは難しく、特に切削工程では工具の摩耗や破損、加工精度の低下、機械自体の故障など、多様な問題が起こり得ます。こうしたトラブルを迅速に解決し、再発を防ぐことは、生産性や作業効率を維持するうえで重要です。
切削時のよくある問題
切削作業中、代表的なトラブルとして挙げられるのが、工具の摩耗や破損です。これが原因で切削面の仕上がりが粗くなり、製品の品質に影響が出る場合があります。
また、加工時の振動も大きな課題です。振動が大きいと精度が低下するだけでなく、工具の寿命が縮まります。
切削油が適切に使われていない、あるいは不足していると、加工面の焼き付きや工具の過熱が起こりやすくなります。これらを防ぐには、工具の定期的な点検や交換、振動を抑えるための機械設定の見直し、そして十分な切削油の管理が大事です。
問題発生時の対処法
切削作業で不具合が発生した場合は、まず原因を特定し、早急に対策を講じる必要があります。たとえば、摩耗や破損した工具を交換してさらなる品質低下を防ぐ、振動が原因なら回転速度や送り速度を調整して振動を抑えるなどの対応が考えられます。
切削油に原因がある場合は、適切な使用量や種類を見直すことで、焼き付きや工具損傷を軽減できるでしょう。こうした対策を行っても改善しない場合は、専門の技術者に相談し、機械全体を改めて点検することも視野に入れるべきです。
予防策とメンテナンス
トラブルを未然に防ぐには、日頃のメンテナンスや対策が重要です。工具を定期的に点検・交換することで摩耗から起こる問題を最小限に抑えられます。切削油の選定と適切な使用量の維持も重要で、油不足や不適切な種類の使用を避けることで工具寿命が延び、加工精度も向上します。
また、機械の定期清掃や点検を行うことで、振動や不具合の兆候を早期に発見できます。加えて、作業環境の整理整頓は、作業者の動きやすさを高め、ヒューマンエラーの低減にもつながります。こうした予防策を地道に積み重ねることで、トラブル発生率が大きく下がり、安定した生産活動を維持できます。
まとめ
マシニングセンターで用いられる対話型プログラムとGコードには、それぞれ異なる強みがあります。対話型プログラムは操作性が高く、新しく機械を導入する際のハードルも低いのがメリットです。
一方、Gコードは複雑な加工をより厳密に制御でき、専門的な現場では欠かせません。いずれの方法を選ぶかは、作業内容やスタッフのスキルレベルなどに応じて判断すべきです。今後、業界が進化していくなかで、両方の手法に通じておくことが、企業の競争力や生産性の向上に直結するといえます。
お問い合わせ
弊社製品、加工についてのお問い合わせは、こちらで受付しております。
各部門のスペシャリストが、ご質問にお応えします。
電話
0574-54-2231
(平日 8:15~17:15)
FAX
0574-54-2235