- 2025/03/03
-
フライスとエンドミルの違いは何?徹底解説!
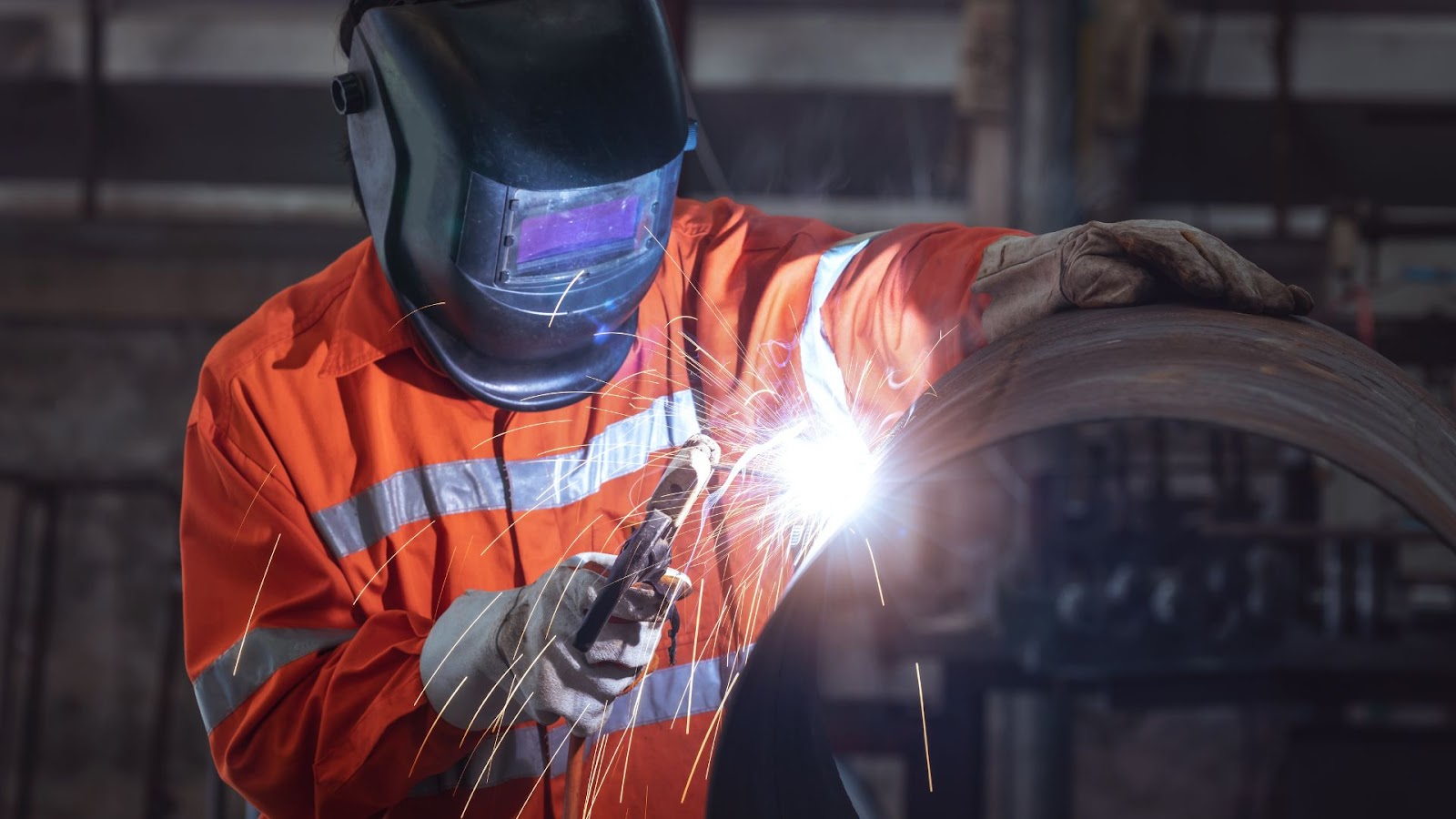
工作物の熱処理法において、フライス加工は基礎的かつ重要な技術の一つです。本記事では、初心者でも理解しやすい形でフライス加工の基礎知識を解説します。
フライス加工の種類や使用するフライス工具、エンドミルとの違いなどを詳しく紹介し、工具の選び方や使用時の注意点、さらに最新技術まで幅広くカバーします。フライスやエンドミルを活用した加工プロセスや応用事例を理解し、実践に役立ててください。
目次 [hide]
フライス加工とは?
フライス加工は切削加工の一種で、主に金属やプラスチックなどの材料を形状加工するために用いられます。回転するフライスカッターによって材料を削り取り、所望の形状や寸法に仕上げるのが特徴です。
水平・垂直・多軸といった多様な方向から加工でき、平面・溝・段差・斜面など複雑な形状にも対応できます。その高い精度と再現性から、機械部品や金型、産業機械など幅広い分野で利用されています。
ただし、機械の設定や操作方法、工具の選択が品質に大きく影響するため、正しい知識と技術が欠かせません。
フライス加工の種類
フライス加工には、エンドミル加工、フェイスミル加工、スロットミル加工、キー溝加工、ホブ加工など多彩な手法があります。いずれも工作機械に取り付けたカッターを回転させて切削する点は共通ですが、用途に応じて使用する工具や加工方法が異なります。
エンドミル加工とフェイスミル加工の違い
- エンドミル加工:円柱形のエンドミルカッターを使い、主に溝や穴、曲面を高精度に削り出す加工。部品の内部を複雑に削る場面で活躍します。
- フェイスミル加工:広い面を効率的に削る工具(フェイスミル)を用いる方法。大型部品の表面を一度に平滑にする際に適しており、作業時間の短縮にもつながります。
フライス工具の種類
フライス加工で用いられる工具は多岐にわたります。エンドミル、フェースミル、アングルカッターなどが代表的で、それぞれ加工形状や効率に違いがあります。
たとえば、エンドミルは細かい溝や曲面に強く、フェースミルは広い平面の切削に長けています。アングルカッターは特定の角度が必要な加工に適しています。いずれの場合も、工具選択が加工品質や効率を大きく左右します。
フライスとエンドミルの違い
フライスとエンドミルはいずれも切削加工に使う工具ですが、用途や形状に違いがあります。一般的に「フライス」と呼ばれるカッターは広い面の平面加工や溝加工を得意とし、工作機械に取り付けて使われます。
一方、エンドミルは穴あけや複雑な形状の削り出しなど、幅広い用途で使われる円柱形のカッターを指します。
フライスの構造
フライスは円盤状のカッターに複数の刃が配置され、広い面を一気に削れる点が特徴です。機械側で角度や位置を調節でき、広範囲の平面や溝加工に対応可能です。
エンドミルの形状
エンドミルはシャンク(軸)に刃を設けた円柱形状の工具で、先端や側面を使って材料を削ります。複雑形状や深い溝、穴加工など、より細かい作業にも適しており、CNCマシニングセンターなどで多用されます。
フライスとエンドミルの使用方法
フライスとエンドミルはいずれも工作機械に取り付けて回転させ、材料を削り出すという点で共通しています。しかし、加工方法やプロセスは用途によって異なります。
フライスを使った加工のプロセス
- 材料を固定:振動やズレを防ぐため、バイスや治具を使ってワークを安定させる。
- 工具選定と取り付け:フェースミルやスロットミルなど、目的に合ったフライスカッターを取り付ける。
- 切削条件の設定:材料の硬さや工具径に合わせ、回転数・送り速度を調整。
- 冷却・刃物の状態管理:加工熱を抑え、工具摩耗を減らすために切削油やクーラントを適切に使用。
- 仕上げ:加工後、表面精度や寸法を確認。必要に応じて最終仕上げを行う。
エンドミルを使った加工の手順
- 工具と材料の選定:エンドミル形状(フラット、ボール、ラフィングなど)や材質(HSS、超硬など)を加工内容に応じて選ぶ。
- 工作物の固定:しっかりクランプし、振動を最小限に抑える。
- 回転速度・送り速度の設定:深い溝や硬い材料ほど熱や摩耗が増えるため、無理のない条件を設定する。
- 冷却・排出:切りくずや切削熱を適切に制御し、工具寿命と加工精度を高める。
- 仕上がり確認:穴や溝の寸法、公差、表面品質を検査し、必要なら追加加工を行う。
フライスとエンドミルの使い分け
フライスは平面や溝の加工に、エンドミルは細かな形状や穴あけ、曲面加工に力を発揮します。工作物の大きさ、形状、必要な精度に合わせ、最適な工具を選ぶことがポイントです。
適切な工具の選び方
- 材料特性:硬度や靭性に合わせて、超硬やコーティング工具などを選択。
- 加工目的:溝加工、穴あけ、平面仕上げなど、作業内容に応じて工具形状を選ぶ。
- コーティングや刃数:被削材との相性や切りくず排出を考慮し、適切な刃先設計を選ぶ。
使用時の注意点
- 工具はしっかり固定し、振動・ズレを防ぐ。
- 回転数や送り速度を過度に上げると、熱や摩耗が増えて工具寿命が縮む。
- 異音や振動が発生したら作業を止め、原因を特定してから再開する。
フライスとエンドミルの使用シーン
それぞれの工具特性を活かし、多種多様な業界・用途で使われています。
フライス加工の応用事例
- 金型の製作:高い寸法精度が要求されるため、フライス加工で平面や斜面をきれいに仕上げる。
- 機械部品・産業機械:精度や強度が求められる部品の溝、段差、斜面加工などに幅広く利用。
- 航空機・自動車部品:大型ワークの削り出しに多軸フライス盤を活用し、複雑な形状にも対応。
エンドミル加工の実践例
- 精密機器部品:小型・複雑形状の部品を高精度で加工。
- 医療機器:複雑なカーブや曲面をもつ器具・部品の加工に最適。
- 多品種少量生産:CNC制御でプログラムを切り替え、様々な形状の加工を効率的に行う。
フライスとエンドミルの最新技術
工具材質の進化やコーティング技術、さらにはIoTやAIを活用した工作機械の高機能化により、フライスやエンドミルによる加工精度・効率は大きく向上しています。
フライスとエンドミルの技術革新の背景
- 高強度・軽量素材の需要:自動車や航空宇宙分野での軽量化要求に応じ、高耐摩耗性の刃先や新素材コーティングが登場。
- ナノ技術やダイヤモンドコーティング:工具寿命を大幅に延ばし、加工面をより高品質に仕上げる。
- IoT・AIの導入:工具摩耗の自動検知や加工条件の自動最適化により、不良率やコストを削減。
まとめ
切削加工においては、工具の選択や熱管理が品質と効率を左右します。フライスやエンドミルによる加工では、回転数や送り速度、冷却手段を適切に設定することで、工具摩耗や加工面の変質を抑え、寸法精度を高めることが可能です。
最新の技術革新も取り入れながら、熱の制御と正しい工具運用を徹底することで、より高度な製品づくりを実現できます。今後もフライス加工やエンドミル加工の技術を学び、熱管理を意識して作業効率や品質向上を目指しましょう。
お問い合わせ
弊社製品、加工についてのお問い合わせは、こちらで受付しております。
各部門のスペシャリストが、ご質問にお応えします。
電話
0574-54-2231
(平日 8:15~17:15)
FAX
0574-54-2235