- 2025/03/19
-
フライス加工におけるフルバックとは?正面フライスの特徴と選び方
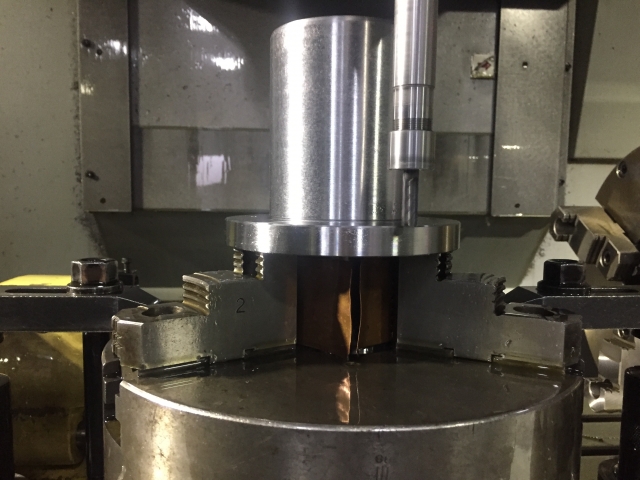
製造現場では、「フルバック」という言葉が使われることがあります。これは正面フライスを指す業界用語の一つですが、その由来をご存じでしょうか。本記事では、「フルバック」と呼ばれる正面フライスの特徴や用途、さらには選定のポイントについて詳しく解説します。フライス加工をより深く理解し、より良い工具を選ぶための参考にしてください。
目次 [hide]
フルバックとは?
製造業の現場では、「フルバック」という言葉が使われることがあります。これは、正面フライスを指す業界用語の一つであり、特に熟練した技術者の間で日常的に用いられています。
この名称が広まった背景には、日本の切削工具メーカーの影響があります。かつて、あるメーカーが正面フライスに「フルバック」という名称を付けて販売しました。その製品が多くの企業で採用され、業界内で広く認知されるようになったことで、次第に「フルバック」という言葉が工具の名称として浸透しており、現在でも、正面フライスの別称として使われることが多く、特に加工現場の会話では自然に通じる言葉となっています。
フライス加工とフルバック(正面フライス)の基本
フライス加工は、さまざまな素材を高精度に削り出すための大切な技術です。特に、正面フライスを使用することで、広範囲の平面加工を効率よく行うことが可能です。加工精度の向上や作業時間の短縮を実現するためには、それぞれの工具の特徴を正しく理解し、より良い方法で活用することが求められます。
ここでは、まずフライス加工の基本について解説し、その後、正面フライスの具体的な役割や使用用途について詳しく見ていきます。
フライス加工とは?
フライス加工とは、回転する工具を用いて金属や樹脂などの材料を削り取る切削技術のことを指します。フライス盤やマシニングセンターといった工作機械に取り付けた工具を高速回転させ、ワーク(加工対象)を削ることで、平面や溝、形状を整えることが可能になります。
この技術は、機械部品の製造や金型の加工、さらには航空宇宙産業や自動車部品の生産など、幅広い分野で活用されています。特に、精密な寸法や滑らかな仕上がりが求められる加工では、フライス加工の精度が製品の品質を左右するため、適切な工具選びが重要になります。
正面フライスの役割
正面フライスは、フライス加工の中でも特に広範囲の平面を効率的に加工するための工具です。エンドミルやフェイスミルといった他のフライス加工用工具と比べても、より大きな面積の削り出しに適しており、生産性の向上に貢献します。
正面フライスが使用される主な加工シーン
- 平面仕上げ
- 大型のワーク(加工対象物)の表面を均一に削り、滑らかに仕上げる際に活躍します。特に、精度が求められる機械部品や金型の製造では、仕上げの品質を向上させるために正面フライスが活用されます。
- 大型のワーク(加工対象物)の表面を均一に削り、滑らかに仕上げる際に活躍します。特に、精度が求められる機械部品や金型の製造では、仕上げの品質を向上させるために正面フライスが活用されます。
- 大径加工
- 通常のエンドミルでは対応が難しい、大きな面積の切削に適しています。特に、一度に広範囲を削ることで作業時間を短縮できるため、大量生産が求められる製造ラインでは欠かせない工具となっています。
- 通常のエンドミルでは対応が難しい、大きな面積の切削に適しています。特に、一度に広範囲を削ることで作業時間を短縮できるため、大量生産が求められる製造ラインでは欠かせない工具となっています。
- 荒加工と仕上げ加工の両方に対応
- 正面フライスは、荒削り(大きく削り取る加工)から仕上げ(表面を滑らかに整える加工)まで幅広く活用できます。刃数やチップの種類を適切に選定することで、求める仕上がりに応じた加工が可能となります。
このように、正面フライスは、フライス加工において大切な役割を果たします。適切な工具を選択することで、加工精度を向上させるだけでなく、生産効率の最適化にも貢献できます。
フルバックの歴史|フライス加工の現場で広まった理由
フルバックという名称は、現在でも製造現場で広く使われているが、その由来を詳しく知っている人は意外と少ないかもしれません。業界内で定着したこの呼び名は、単なる通称ではなく、特定の切削工具メーカーが生み出したものであり、技術の進化とともに広まっていきました。フルバックがどのように誕生し、なぜここまで普及したのか、その歴史を紐解いてみましょう。
フルバックの誕生
「フルバック」という名称は、日本のある切削工具メーカーが販売した正面フライスの商品名に由来しています。このメーカーが、当時の加工現場のニーズに応じた高性能な正面フライスを開発し、「フルバック」というブランド名で市場に投入しました。その製品は、安定した切削性能と耐久性の高さが評価され、業界内で広く普及しました。
正面フライスは、それ以前から存在していた工具ですが、従来のものと比べてこの「フルバック」という製品は、加工精度や工具寿命の面で優れた特性を持っていました。そのため、多くの企業がこの製品を導入し、「フルバック」という名称がそのまま正面フライスの代名詞のように定着することとなったのです。
フルバックが広まった背景
「フルバック」という名称が急速に広まった理由のひとつに、当時の製造業の発展と技術革新があります。切削加工の分野では、より精度の高い部品製造や、作業の効率化が求められていました。
特に、以下のような要因が、フルバックの普及に大きく影響を与えました。
- 加工精度の向上:フルバックは従来の正面フライスよりも安定した切削が可能で、部品の寸法精度が向上した。
- 耐久性の向上:特殊な刃先設計や素材の工夫により、工具の摩耗が少なく、長時間使用できるようになった。
- 作業効率の改善:一度に広い範囲を加工できるため、生産ラインの作業時間を短縮し、コスト削減につながった。
こうした特徴により、「フルバック」という製品は、多くの加工現場で導入され、その結果として「正面フライス」=「フルバック」という認識が浸透していきました。
また、日本の切削工具メーカーは、この技術を活かして海外市場にも展開を進め、フルバックは国際的にも評価されるようになりました。国内外を問わず、フルバックという呼称が技術者の間で使われるようになり、今日に至るまで業界内で根付いています。
現在の業界での位置づけ
現在でも、「フルバック」という言葉は製造現場で使われることが多く、ベテラン技術者の間では一般的な呼称として定着しています。しかし、技術文書や製品カタログでは「正面フライス」という正式名称が用いられることが一般的です。
その理由の一つとして、新しい世代の技術者や海外の取引先とのコミュニケーションにおいて、統一した名称を使用する必要があることが挙げられます。そのため、企業の公式な資料では「正面フライス」と表記されることが多く、「フルバック」という言葉は現場の口語表現として残っている状態です。
しかし、現場レベルでは今でも「フルバック」という呼称が使われ続けており、新人技術者がベテラン技術者からこの言葉を学ぶ場面も少なくありません。結果として、業界内での伝統的な用語として生き続けているのです。
また、一部の切削工具メーカーでは、フルバックの名称をブランド名として再活用し、新たな高性能正面フライスを展開する動きも見られます。このように、「フルバック」という言葉は単なる業界用語にとどまらず、技術の進化とともに再び注目される可能性を秘めています。
フルバック(正面フライス)の特徴
正面フライスは、加工の効率や精度を左右する大切な工具です。その中でも「フルバック」と呼ばれるタイプは、用途や加工対象に応じてさまざまなバリエーションが存在します。それぞれの特性を理解し、適切な選択を行うことで、工具の寿命を延ばし、作業の生産性を向上できます。ここでは、代表的なフルバックの種類について詳しく見ていきましょう。
フルバックの種類
フルバック(正面フライス)には、加工対象の材質や用途に応じたさまざまな種類が存在します。適切な種類を選択することで、切削精度の向上や工具の寿命を延ばすことが可能になり、結果として生産効率の改善につながります。以下に代表的なフルバックの種類を紹介します。
超硬チップ付きフルバック
超硬合金製のチップを使用したタイプで、耐久性が高く、長時間の連続加工に適しているのが特徴です。切削抵抗が少なく、摩耗しにくいため、精密加工が求められる場面で活躍します。
- 適用範囲: 高精度な仕上げ加工、大量生産向けの加工
- メリット: 切削時の熱に強く、硬い材質でも安定した加工が可能
- デメリット: 一般的な工具に比べて価格が高め
特に、金型加工や航空機部品の製造など、精密な仕上げが必要なケースでは、超硬チップ付きフルバックがよく使用されます。
高速鋼(HSS)フルバック
高速度工具鋼(HSS)を素材としたフルバックで、コストパフォーマンスに優れ、汎用性が高いのが特徴です。耐摩耗性は超硬チップ付きのものに比べると劣りますが、加工条件を適切に設定すれば安定した切削が可能です。
- 適用範囲: 試作加工、小ロット生産、軽切削用途
- メリット: 価格が比較的安価で、幅広い加工に対応
- デメリット: 長時間の使用では摩耗しやすく、頻繁なメンテナンスが必要
試作品の製作や、小規模な部品加工の現場では、高速鋼フルバックのコストメリットが大きく活かされます。
クーラント対応フルバック
切削時の発熱を抑えるために、クーラント(冷却液)を効果的に供給できる設計が施されたフルバックです。熱がこもると加工精度に悪影響を及ぼすため、高温になりやすい材料や長時間の連続切削に適しています。
- 適用範囲: チタンやステンレスなど熱伝導性の低い金属の加工
- メリット: 熱による工具の摩耗を抑え、長寿命化につながる
- デメリット: クーラント供給設備が必要なため、導入コストがかかる
チタンやインコネルのような難削材の加工では、クーラント対応フルバックの導入によって、工具の摩耗を軽減し、安定した品質を維持することが可能になります。
各種類の適用範囲
選択するフルバックの種類によって、加工効率や仕上がりの品質が大きく異なります。用途に応じた適切な選定を行うことで、作業効率を向上させることが可能です。
フルバックの種類 | 主な用途 | メリット | デメリット |
超硬チップ付きフルバック | 高精度仕上げ加工、大量生産 | 耐摩耗性が高く、長時間の安定した加工が可能 | 価格が高い |
高速鋼(HSS)フルバック | 試作、小ロット生産、汎用加工 | コストが安く、幅広い加工に対応 | 摩耗しやすく、メンテナンスが必要 |
クーラント対応フルバック | 難削材の加工、高温になりやすい素材 | 熱による工具の摩耗を抑え、寿命が長い | クーラント供給設備が必要 |
例えば、金型のような精密加工では超硬チップ付きフルバックが適切であり、一方で試作品の加工や汎用的な用途には高速鋼フルバックが使われることが多くなります。また、熱の影響を受けやすい難削材の加工ではクーラント対応タイプが有効です。
適切なフルバックを選ぶことで、加工精度を高めるだけでなく、工具の寿命を延ばし、コスト削減にもつながるため、使用環境に合わせた選択が重要になります。
フルバックの選び方
フルバック(正面フライス)を適切に選定し、正しく使用することは、加工の精度や生産効率を左右する大切な要素です。特に、加工材質に適したフルバックを選ぶことで、工具の寿命を延ばし、作業コストの削減につながります。また、使用中の管理やメンテナンスを徹底することで、安定した加工品質を維持することが可能になります。ここでは、フルバックを選ぶ際のポイントと、長く活用するための管理方法について詳しく解説します。
加工材質ごとの適したフルバックの選定
フルバックを選ぶ際は、加工対象の材質に適した工具を選択することが大切です。素材ごとに適したフルバックを使用することで、工具の摩耗を抑えつつ、高品質な仕上がりを実現できます。以下に、代表的な加工材質ごとの適切なフルバックの選び方を紹介します。
鋼材の加工
鋼材の加工では、硬度が高く耐摩耗性に優れたフルバックが求められます。特に、超硬チップ付きフルバックが適しており、長時間の連続使用にも耐えることが可能です。
- 推奨工具: 超硬チップ付きフルバック
- 理由: 切削時の摩耗が少なく、安定した加工が可能
- 注意点: 高い硬度を持つため、欠けやすい場合がある。適切な切削条件の設定が重要
アルミ加工
アルミは比較的柔らかい素材のため、高速での切削が可能です。そのため、軽量でコストパフォーマンスに優れる高速鋼(HSS)フルバックが適しています。
- 推奨工具: 高速鋼(HSS)フルバック
- 理由: 軽量でありながら十分な耐久性を持ち、高速回転での加工に向いている
- 注意点: 加工速度が速すぎるとバリ(切削時の残りカス)が発生しやすいため、適切な回転数を維持することが重要
難削材(チタンやインコネルなど)
チタンやインコネルのような難削材は、熱がこもりやすく、通常の工具では摩耗が激しくなります。このため、クーラント対応フルバックがおすすめです。
- 推奨工具: クーラント対応フルバック
- 理由: 冷却効果を高め、熱による工具の摩耗を抑えることができる
- 注意点: クーラントを適切に供給しないと、効果が十分に発揮されない
適切なフルバックを選択することで、工具の寿命を延ばし、加工の効率をできる限り高められます。
工具寿命を延ばすための管理
フルバックを長く使用するためには、適切な切削条件の設定と定期的なメンテナンスが不可欠です。特に、加工条件を誤ると、工具の摩耗が早まり、結果的にコスト増加につながることがあります。
適切な切削条件の設定
切削速度や送り速度、切削深さなどの条件を適切に設定することで、工具の寿命を大幅に延ばすことが可能です。
- 回転速度の効率化:
- 速すぎると摩耗が早まり、チップの欠けが発生する可能性がある
- 遅すぎると切削効率が低下し、生産性が悪化する
- 切削深さの調整:
- 深すぎると工具に過剰な負荷がかかり、寿命が短くなる
- 適度な切削深さを設定することで、安定した加工が可能
- 送り速度の調整:
- 送りが速すぎると切削負荷が増し、工具の摩耗が加速する
- 適切な送り速度を維持することで、切削面の品質も向上
これらの条件を適切に調整することで、工具の負荷をできる限り抑えながら、長期間にわたって安定した加工を実現できます。
チップ交換時の注意点
フルバックの多くはチップ交換式であり、摩耗したチップを適切なタイミングで交換することが求められます。チップの摩耗を放置すると、以下のような問題が発生する可能性があります。
- 切削精度の低下: 切れ味が落ちることで、加工面が荒くなり、品質が不安定になる
- 加工負荷の増大: 摩耗したチップでは切削抵抗が増し、工具本体にも負担がかかる
- 工具本体の寿命が短くなる: チップを適切に交換しないと、フルバック全体の寿命にも影響を及ぼす
適切なチップ交換のタイミング
摩耗を見極めるポイントとして、加工面の仕上がりや切削時の異音に注意を払うことが大切です。
- 仕上がりの悪化: 切削面が粗くなったり、加工精度が低下してきたら交換のサイン
- 異音の発生: 正常な切削時と比べて、異常な振動や異音が発生した場合は、チップの摩耗が進行している可能性がある
- 工具負荷の増加: 切削中に工具がスムーズに動かなくなった場合、摩耗したチップが原因の可能性がある
また、定期的な点検と交換スケジュールを設定することで、突発的な工具トラブルを防げます。特に、大量生産を行う現場では、計画的なチップ交換が加工ラインの安定稼働につながります。
フルバックと他のフライス加工工具の違い
フルバック(正面フライス)は、特に大径の平面加工に特化した工具ですが、他にもエンドミルやフェイスミルなどの工具が存在します。これらの工具は、それぞれの特性を活かし、異なる用途で使用されるため、適切に使い分けることで加工の効率と品質をに向上できます。
エンドミル・フェイスミルとの比較
フルバック(正面フライス)は、エンドミルやフェイスミルと比べると、大きな平面の切削を得意とする工具です。それぞれの特徴を理解し、用途に合わせた選択を行うことが大切です。
エンドミルとは?
エンドミルは、主に小型部品の加工や溝加工に適した工具です。先端や側面に刃を持っており、垂直方向(Z軸)の切削が可能であるため、穴あけや細かな形状の切削にも対応できます。
- 適用範囲: 小型部品の加工、溝加工、穴あけ、輪郭切削
- メリット: 小回りが利き、細かい加工や複雑な形状の切削が可能
- デメリット: 広範囲の平面加工には向かない
フェイスミルとは?
フェイスミルは、仕上げ加工や高速加工に向いている工具であり、主に平面仕上げの用途で使われます。フルバックと用途が似ていますが、フェイスミルは比較的小径の工具が多く、切削面の仕上がりの美しさが求められる場面で活躍します。
- 適用範囲: 平面仕上げ加工、薄いワークの加工
- メリット: 高速回転が可能で、滑らかな仕上がりを実現
- デメリット: 広範囲の加工には不向きで、大径の加工には時間がかかる
フルバック(正面フライス)の特徴
フルバック(正面フライス)は、上記の工具と異なり、一度に広範囲を削れるため、特に大きなワークの加工に適しています。
- 適用範囲: 大径の平面加工、厚みのある部品の削り出し
- メリット: 大面積を効率的に切削でき、均一な仕上がりを実現
- デメリット: 細かい加工や複雑な形状の切削には向かない
フルバックのメリット・デメリット
ここでは、フルバックのメリットとデメリットをみていきましょう。
フルバックのメリット
- 広範囲の加工が可能: 一度に大きな面積を削れるため、大径の平面加工におすすめ
- 高い作業効率: 加工時間を短縮できるため、生産性の向上に貢献
- 安定した仕上がり: 均一な加工が可能で、仕上げ品質が安定する
フルバックのデメリット
- 小回りが利かない: 細かい形状の加工には適しておらず、エンドミルやフェイスミルとの併用が必要
- 初期導入コストが比較的高い: 大型の工具であるため、導入コストがかかる
用途に応じた適切な使い分け
フルバック、エンドミル、フェイスミルは、それぞれ得意とする加工が異なります。そのため、以下のような場面で使い分けることが大切です。
工具 | 主な用途 | 特徴 | メリット | デメリット |
フルバック(正面フライス) | 大面積の平面加工 | 広範囲の加工に適している | 均一な仕上がり、作業効率が高い | 小回りが利かない、初期コストが高い |
エンドミル | 小型部品、溝加工、穴あけ | 細かい形状の加工が得意 | 複雑な形状の加工が可能 | 広範囲の加工には時間がかかる |
フェイスミル | 平面仕上げ | 滑らかな仕上がりを実現 | 高速回転が可能、仕上げ品質が良い | 大径加工には向かない |
このように、フルバックは大面積の加工におすすめですが、細部の加工にはエンドミルやフェイスミルとの併用が不可欠です。たとえば、大きな部品の平面をフルバックで削り出した後、細部の仕上げや形状加工にはエンドミルを使用するといった使い分けが効果的です。
適切な工具を選択し、それぞれの特性を活かして加工を行うことで、精度の高い仕上がりを実現しながら、生産効率も向上できます。
まとめ
「フルバック」は、日本の切削工具メーカーが開発・販売した正面フライスの商品名が由来となり、業界全体に広がった呼称です。現在でも製造現場では広く使われており、特に技術者の間では一般的な言葉として定着しています。
正面フライスは、フライス加工において大面積の平面加工を効率よく行うための大切な工具です。適切な種類を選択し、加工条件を効率化することで、仕上がりの品質向上、作業効率の向上、コスト削減を実現することが可能になります。
また、フルバックはエンドミルやフェイスミルとは異なる特性を持ち、それぞれの工具と組み合わせて使用することで、加工精度をさらに高められます。フライス加工における正面フライスの役割を正しく理解し、より良い工具を選定することで、より高品質な加工を実現しましょう。
お問い合わせ
弊社製品、加工についてのお問い合わせは、こちらで受付しております。
各部門のスペシャリストが、ご質問にお応えします。
電話
0574-54-2231
(平日 8:15~17:15)
FAX
0574-54-2235