- 2024/04/26
-
旋盤ねじ切りの手順とは?外径寸法や計算式・回転数を詳しく
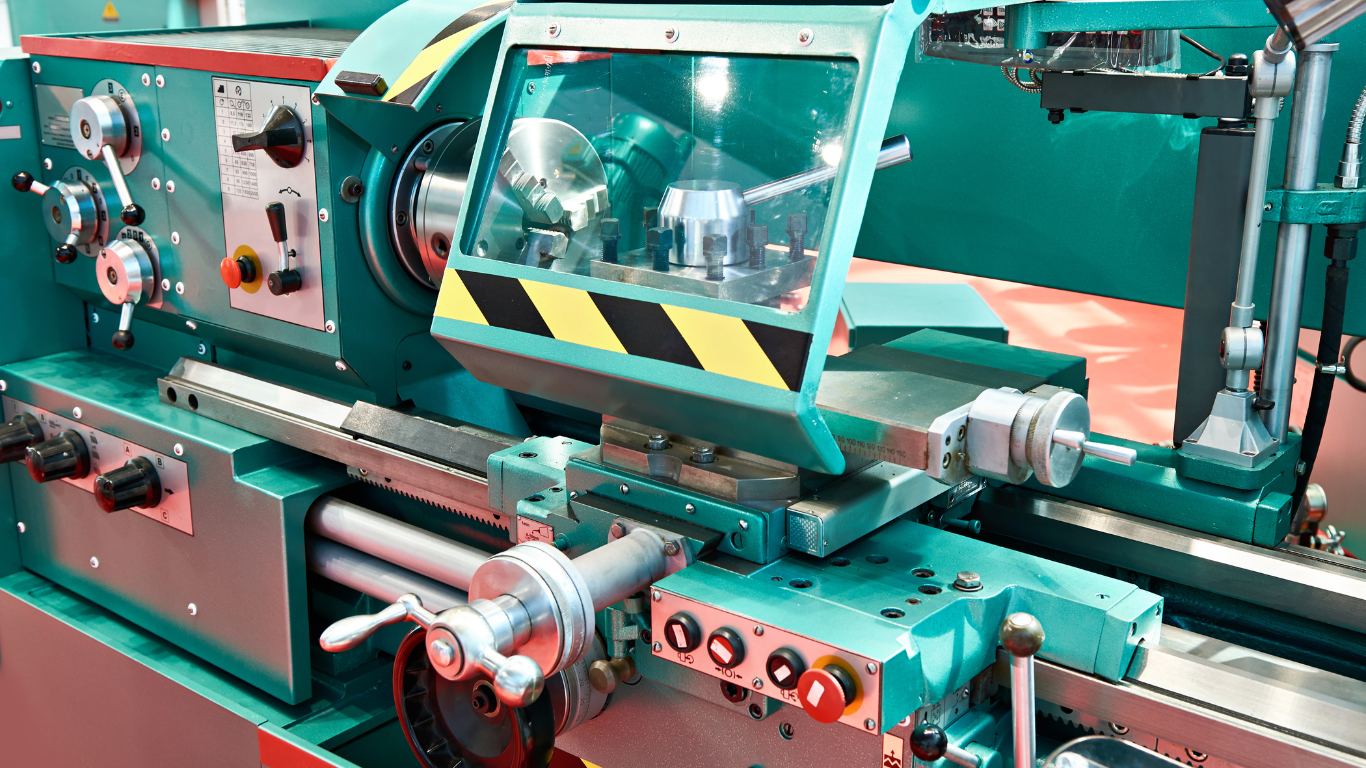
旋盤ねじ切りは、機械加工のなかで重要な技術の一つです。この記事では、初心者にもわかりやすく、具体的な手順や計算式について詳しく解説します。
また、トラブルシューティングや旋削チップの選定方法、切削力の設定方法やツールのメンテナンスに関するお話もしていきます。
目次 [hide]
ねじ・ねじ切りの基本
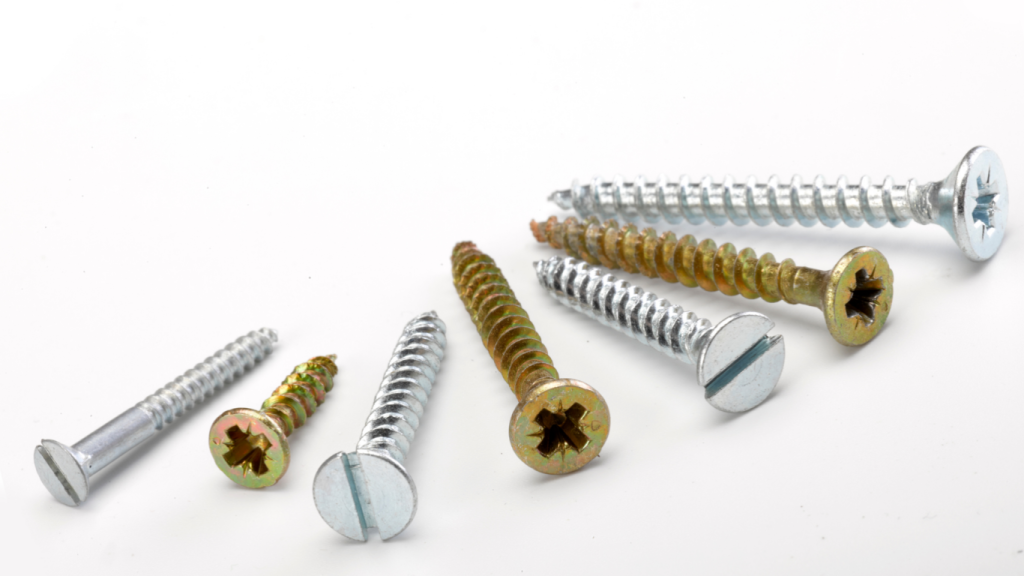
ねじは、様々な産業や日常生活で広く使用されています。以下に、ねじの基本的な知識とねじ切り加工のポイントをまとめます。
- ねじの基本構造
- 頭部: 工具と接触する部分で、プラス、マイナス、六角など様々な形状があります。
- 軸部: 螺旋状の溝があり、これが材料に食い込むことで固定力を発生させます。
- 先端部: ねじを材料に挿入する際にガイドとなる部分です。
- ねじの種類と用途
- 木ねじ: 木材を固定するのに使用されます。
- 機械ねじ: 金属やプラスチック部品を結合する際に使われます。
- タッピングねじ: 予め開けられた穴に直接ねじ込むことができます。
- ねじ切り加工の手順と注意点
- 下穴開け: ねじの外径より少し小さめに開けることが一般的です。
- ねじ山の切削: タップを使用してねじ山を形成します。タップのサイズと形状を適切に選ぶことが重要です。
- 力の均等なかけ方: タップを回す際は、力を均等にかけ続けることが必要です。
- 切りくずの除去: 途中でタップを逆回転させることで、切りくずを除去しやすくなります。
ねじ切りは正確なフィットを確保するため、何度かの試行錯誤が必要です。これにより、接合部の強度と耐久性を高めることができます。適切な知識と技術を身に付けることで、どのような状況でも適切なねじ選びとねじ切りが行えるようになります。
ねじ切り加工の流れ
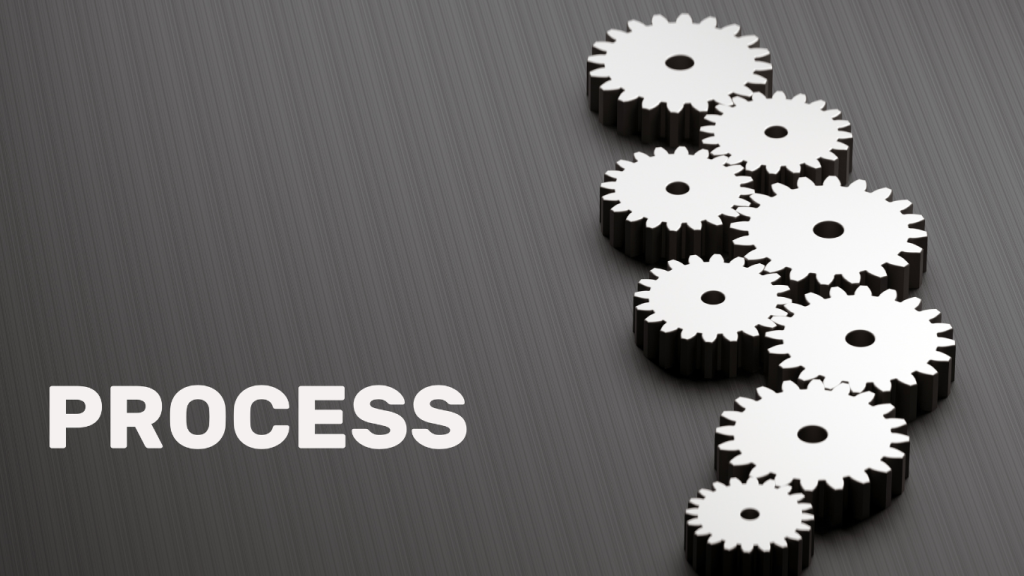
ねじ切り加工の各工程は緻密な調整と確認が求められるため、作業者の経験と技術が重要です。正確な作業により、寸法が合ったねじが作られます。以下がおおまかな流れとなります。
1. バイトを取り付ける
バイトを取り付ける際は、まず工具の選定を行います。適切なバイトを選ぶことで、ねじ切り作業の効率が向上します。次に、取り付け部の清掃を行い、異物を取り除きます。これにより、不具合の発生を防ぎます。
バイトの取り付けは慎重に行う必要があります。位置を確認しながら、ネジを締め付けて固定します。適切な締め付けトルクで固定することで、工具が動かないようにします。
2. 条件の設定
条件の設定では、まず回転速度と送り速度を調整します。これらの設定は、素材やバイトの種類に応じて異なります。次に、深さとピッチを設定します。これにより、精度の高いねじを切ることができます。
加工中の温度管理も重要です。冷却液や潤滑剤を適切に使用することで、切削温度を抑えます。これにより、工具の寿命が延び、品質の良い仕上がりになります。
3. 面取り
面取りは、ねじ切りの前に行う重要な工程です。まず、加工する部位をきれいに整えます。これにより、後のねじ切りがスムーズに進みます。
次に、バリを取り除くための工具を使用します。バリが残ると、ねじの精度が下がるため、丁寧に取り除くことが求められます。最後に、表面をなめらかに仕上げます。面取りをしっかり行うことで、ねじの接合が強固になります。
ネジ切りのサイクルとは
ネジ切りのサイクルとは、CNC(コンピュータ数値制御)旋盤やマシニングセンターなどの工作機械で自動的にねじを切るためのプログラムのことを指します。
このプログラムを用いることで、機械はあらかじめ設定された指示に従って、材料にねじ山を形成します。ネジ切りサイクルは効率的で精密なねじ切りを実現するために広く利用されています。
ネジ切りサイクルの主なステップ
- プログラミング:
- ねじの直径、ピッチ(ねじ山の間隔)、ねじの長さ、切り込みの深さなどのパラメータをプログラムに入力します。
- 工具の設定:
- 適切なねじ切り工具(タップやダイス)を機械にセットアップします。
- 下穴の加工:
- ねじ切りを行う前に、適切なサイズの下穴を材料に開けます。この下穴は、ねじの内径よりわずかに小さいサイズであることが一般的です。
- 自動ねじ切りサイクルの実行:
- プログラムに従って、機械が自動的にねじを切り始めます。これには、切削油の注入、工具の進行と退行、ねじ山のカットが含まれます。
- ねじ山の検査と仕上げ:
- ねじ切りが完了したら、ねじ山が正しく形成されているかを検査し、必要に応じて追加の加工を行います。
ネジ切りサイクルの利点
- 効率性: 手動でねじ切りを行うよりも速く、多くのねじを連続して迅速に加工できます。
- 再現性と精度: 同じパラメータで一貫した品質のねじを何度も作成することが可能です。
- 労力の軽減: 操作者の手作業を減らし、肉体的な負担を軽減します。
ネジ切りサイクルは、製造業での生産性を向上させ、一貫した品質保持に重要な役割をもちます。特に量産環境や精密部品の製造において、この自動化は不可欠となるでしょう。
旋盤ねじ切りの種類・方法
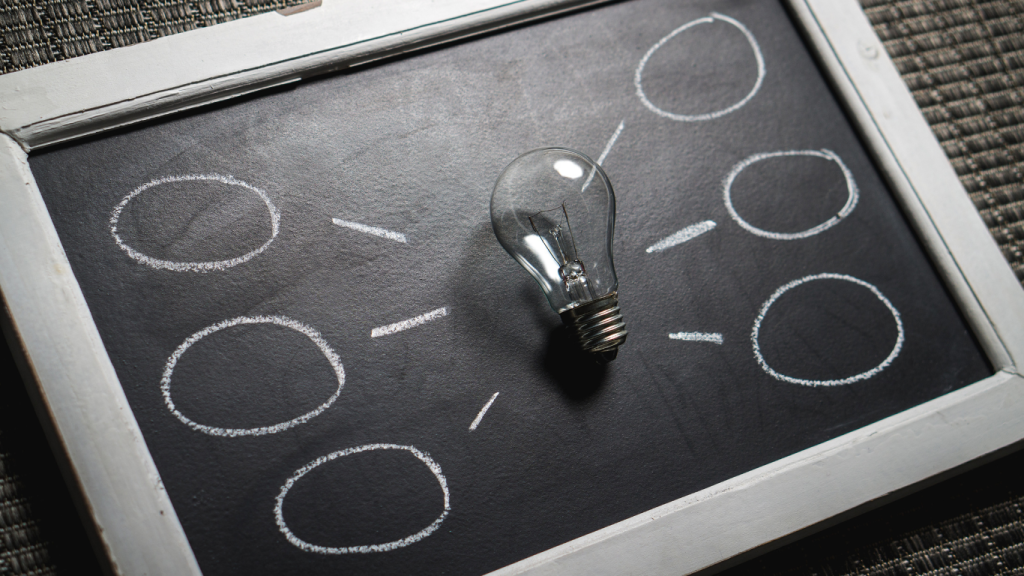
旋盤のねじ切りとは、金属やプラスチックなどの材料にねじ山を作る加工方法です。ねじ山は、部品同士をしっかりと固定するために不可欠な要素です。
おねじ切り
おねじ切りは、外側にねじ山を形成する加工方法です。材料の外周にねじを切ることで、ナットやめねじ加工された部品と組み合わせることが可能になります。ここではおねじ切りの基本的な手順を説明します。
- 外径の準備:
- おねじを切る部分の外径を正確に加工します。この外径はねじの規格によって異なり、正確な寸法が求められるため、旋盤やフライス盤などで精密に加工する必要があります。
- ダイスの選定:
- ねじ切りに使用するダイスを選びます。ダイスはねじの種類(メートルねじ、インチねじなど)とサイズに応じて異なります。
- ねじ切り:
- ダイスをダイスホルダーに固定し、準備した材料の外周に適用します。手動であれば、均等な圧力をかけながらゆっくりと回転させ、ねじ山を切っていきます。途中でダイスを少し戻すことで切り屑を排出し、ダイスの詰まりを防ぎます。
- 検査と仕上げ:
- ねじ切りが完了したら、ねじゲージを使用して精度を検査します。必要に応じて追加の調整を行い、ねじ山のバリを取り除くなどの仕上げ作業をします。
おねじ切りは、ねじを形成する際の正確さが重要であり、工具の扱いや材料の選定に注意が必要です。正しいツールと技術を用いることで、高品質なねじ接合部を作成することができます。
めねじ切り
めねじ切りは、材料の内部にねじ山を形成する加工方法です。通常、穴を開けた後にタップと呼ばれる特殊な切削工具を使用して内側にねじを切ります。ここではめねじ切りの基本的な手順を説明します。
- 下穴の開け方:
- めねじを切る前に、タップに適合するサイズの下穴を開けます。この下穴の大きさはタップサイズとねじのピッチによって異なりますが、一般的にはタップの外径よりわずかに小さい径が適切です。
- タップの選定:
- 材料の種類とねじの用途に応じて、適切なタップを選びます。手動で行う場合はストレートフルートのタップが一般的ですが、機械使用の場合はスパイラルフルートやスパイラルポイントのタップが適しています。
- タッピング:
- タップを下穴に挿入し、手動または機械を用いてゆっくりと回転させます。このとき、途中でタップを少し戻すことで切り屑を排出し、タップの詰まりや破損を防ぎます。
- 検査:
- ねじ切りが終了したら、ねじゲージやボルトを使用して、ねじが適切に形成されているかを確認します。
めねじ切りは正確な寸法と手順を守ることが非常に重要で、適切に行うことで強度の高いねじ接合が得られます。
NC旋盤・おねじ切り
NC旋盤でのおねじ切りは、高精度かつ効率的にねじ山を形成する方法です。以下はNC旋盤を使用しておねじを切る基本的な流れです。
- プログラミング:
- NC旋盤の操作には、適切なプログラミングが必要です。ねじのピッチ、外径、切り込み深さなどのパラメータを設定し、これに基づいてGコードや他の対話式プログラムを作成します。
- 材料のセットアップ:
- 切り込む材料を旋盤のチャックにしっかりと固定し、正確にセンタリングします。材料が安定していないと、ねじ切りの精度に影響が出ます。
- 切削工具の選定と設置:
- おねじ切りに適した切削工具(ねじ切りインサート)を選び、ツールホルダーにセットします。切削工具の先端形状がおねじの形状と一致している必要があります。
- 加工サイクルの開始:
- プログラムに従って自動加工を開始します。NC旋盤は、プログラムされたパスに従って材料に対して切削工具を正確に動かし、ねじ山を切り進めます。
- 監視と調整:
- 加工中には、工具の摩耗や切り屑の除去を定期的にチェックし、必要に応じて調整を行います。NC旋盤の監視システムを使用して、加工の進行状況を確認することも可能です。
- 最終検査:
- ねじ切りが完了したら、ねじゲージを使用してねじの精度を検査します。寸法やピッチが仕様に適合しているか確認し、問題があれば追加の加工を行います。
NC旋盤によるおねじ切りは、一貫した精度と高い生産性を実現できるため、特に大量生産において有効です。適切なプログラミングと工具の管理により、優れたねじ加工が可能となります。
NC旋盤・めねじ切り
NC旋盤でのめねじ切りは、精密で効率的な内ねじの加工方法です。NC旋盤を使用することで、高い再現性と速度で複雑なねじ形状を正確に切削することができます。以下に、NC旋盤を用いためねじ切りの基本的な手順を説明します。
- プログラミング:
- めねじのスペック(内径、ピッチ、ねじの深さなど)に基づいてNCプログラムを作成します。このプログラムは、ねじの加工パラメータを含むGコードやその他のコマンドで構成されます。
- 下穴の加工:
- めねじを切る前に、材料に正確な下穴を開ける必要があります。下穴の直径はめねじの内径に合わせて選定し、旋盤でドリル加工を行います。
- 切削工具の選定と取り付け:
- めねじ用のタップを選び、それをツールホルダーに取り付けます。タップの種類とサイズはねじの仕様によって異なります。
- 自動加工の開始:
- プログラムを旋盤に入力し、自動加工サイクルを開始します。NC旋盤はタップを用いて自動的に内ねじを形成します。このプロセスは、タップが正確に位置決めされ、均等に圧力をかけながらねじ山を切ることが重要です。
- 監視と調整:
- 加工中、工具の摩耗や切削状態を監視し、必要に応じて調整を行います。NC旋盤のセンサーや監視機能を利用して、常に最適な加工条件を維持します。
- ねじの検査:
- めねじ加工後、ねじゲージを使用してねじの精度を確認します。仕様に適合しているかを検査し、問題があれば調整や再加工を行います。
NC旋盤によるめねじ切りは、その高度な制御機能と自動化により、連続生産における時間とコストの削減に貢献します。
旋盤のねじ切り・計算式(方法)と切り込み表
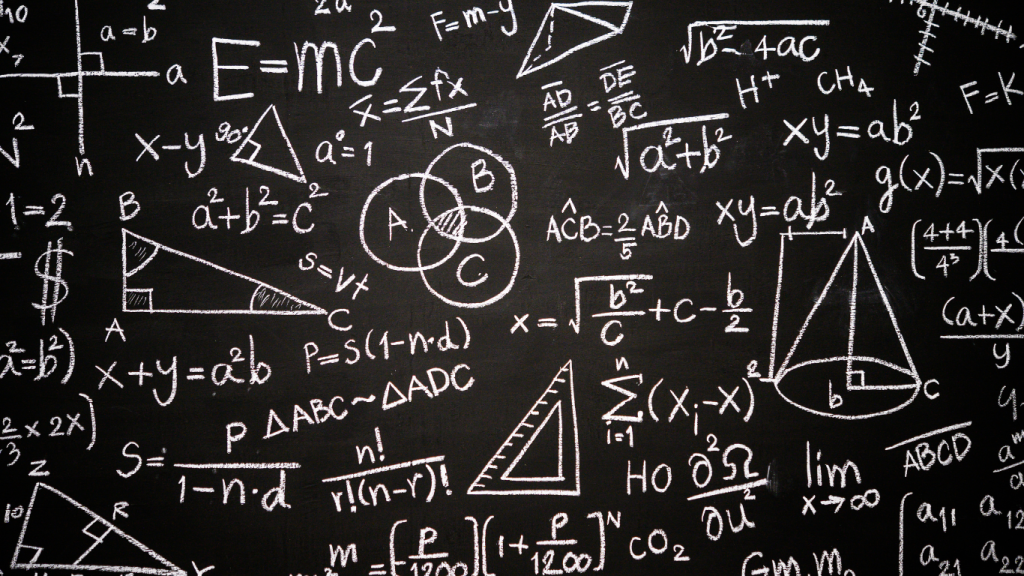
ねじ切り加工は旋盤で行われる精密な作業の一つで、適切な計算式を用いて正確な切削を行うことが求められます。ここでは、旋盤とNC旋盤におけるねじの切り方と必要な計算式を説明します。
ねじ切りの基本計算式
- 外径の計算:
- Do=Dn−(1.082532×P)D_o = D_n – (1.082532 \times P)Do=Dn−(1.082532×P)
- DoD_oDo は外径、DnD_nDn は公称径、PPP はピッチです。
- 下穴径の計算:
- Dhole=Do−PD_{hole} = D_o – PDhole=Do−P
- 下穴はねじの外径よりわずかに小さく
4旋盤のねじ切り・計算式(方法)ChatGPT
旋盤でのねじ切りには、正確な計算式が必要です。これにより、ねじの精度と強度を確保し、効率的な生産を実現できます。以下に基本的なねじ切りの計算方法を紹介します。
下穴径の計算
ねじ切りに先立ち、正しい下穴径を計算することが必要です。この径は、ねじの種類やサイズに依存しますが、一般的にはねじの外径よりも少し小さいサイズにします。
- メートルねじ (M) の場合: Dhole=D−PD_{hole} = D – PDhole=D−P ここで DDD は公称外径、PPP はピッチです。
切り込み深さの計算
切り込み深さはねじ山の深さを決定し、これが全体のねじ強度に大きく影響します。
- 切り込み深さの公式: h=0.613×Ph = 0.613 \times Ph=0.613×P PPP はピッチです。
ねじのリード角の計算
ねじ山を切る際の工具の進行角度、つまりリード角も重要です。
- リード角の計算: θ=tan−1(Pπ×Dmean)\theta = \tan^{-1}\left(\frac{P}{\pi \times D_{mean}}\right)θ=tan−1(π×DmeanP) DmeanD_{mean}Dmean はねじの中間径です。
工具の進行速度
ねじ切り工具の進行速度は材質や切削条件によって異なりますが、一般的な速度設定があります。
- 進行速度の設定: 通常、ねじ切り工具の速度は低めに設定し、切削油を使用して摩擦を最小限に抑えます。
これらの計算式を使用して、旋盤でのねじ切りを行う際には、正確な測定と設定が非常に重要です。プログラム可能なNC旋盤を使用する場合、これらのパラメータはソフトウェアによって自動的に計算され、適切に設定されるため、操作が大幅に簡単になります。
切り込み量の計算
- ねじのピッチに基づく計算: ねじのピッチ PPP は、切込み量を決定するための重要な要素です。一般的に、ねじの総切込み量は次の式で計算されます:総切込み量=0.75×P−ノーズR総切込み量 = 0.75 \times P – ノーズR総切込み量=0.75×P−ノーズRここで、ノーズR はバイトの先端半径です。より簡単に計算する場合、ノーズR を無視して 0.65×P0.65 \times P0.65×P としても大きな問題はありません。
- 切込み回数の決定: 総切込み量を複数回に分けて行うことが推奨されます。これにより、バイトへの負荷を軽減し、チッピングやバリの発生を防ぎます。
- 最初のパスでは大きな切込み量を設定し、各パスごとに少しずつ減らしていきます。
- 例えば、ピッチが 1.5mm の場合、総切込み量は約 0.975mm です。この量を5回に分けて切削する場合、次のようになります:
- 1回目: 0.30mm
- 2回目: 0.25mm
- 3回目: 0.20mm
- 4回目: 0.15mm
- 5回目: 0.075mm
- 素材とバイトの種類: 加工する素材と使用するバイトの種類も切込み量に影響します。硬い素材や繊細なバイトを使用する場合は、切込み量を小さく設定する必要があります。
- 機械の設定と条件: 旋盤の性能や条件に応じて、適切な切込み量を調整します。古い機械や精度が低い機械では、無理な切込みを避け、複数回に分けて慎重に切削を進めることが重要です。
切込み量と回転数の設定例
以下に、ピッチ 1.5mm のねじを切る際の具体的な設定例を示します:
- ピッチ: 1.5mm
- 総切込み量: 0.975mm
- 切込み回数: 5回
- 各パスの切込み量:
- 1回目: 0.30mm
- 2回目: 0.25mm
- 3回目: 0.20mm
- 4回目: 0.15mm
- 5回目: 0.075mm
- 回転数: 使用するバイトと素材に応じて設定。一般的には低速(100-200 RPM)が推奨されます。
旋盤のねじ切りトラブルシューティング(問題と解決策)
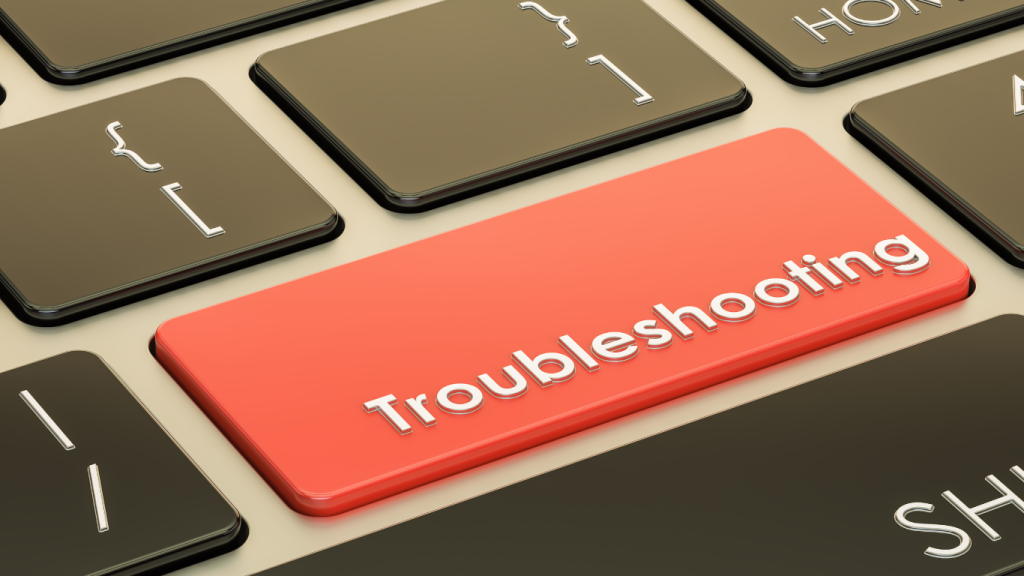
ねじ切り作業の問題点とその解決策について詳しく説明します。
ねじ山のバリ(カエリ)について
ねじ山のバリは、完成後にねじの精度や見た目を損なう原因となります。この問題を解消するためには、工具の選定や切削条件の調整が必要です。
例えば、適切なバイトの使用と速度調整を行うことで、バリの発生を抑えることができます。また、仕上げ加工としてデバリング工具を使用することも効果的です。これにより、ねじ山の品質を向上させることができます。
ねじ山のバリを取り除くには、十分な冷却を行うことも重要です。冷却材を適切に使うことで、切削時の熱を抑えバリを最小限にします。さらに、切りくずの排出をスムーズにするための工夫も必要です。これにより、安定した切削が可能となります。
バイトが折れたとき
バイトが折れたときの対応には、原因を特定し、適切な解決策を実施することが重要です。以下はバイトが折れた際の一般的な対処法です:
- 停止と安全確認:
- すぐに機械を停止させます。
- 安全を確認した上で、折れたバイトの破片を取り除きます。
- 原因の特定:
- 折れた原因を分析します。過剰な負荷、不適切な切削条件、バイトの取り付け誤り、材質の選択ミスなどが考えられます。
- バイトの交換:
- 折れたバイトを新しいものに交換します。この際、バイトの種類や材質が適切であることを確認してください。
- 切削条件の見直し:
- 切削速度、送り速度、切り込み深さを見直し、必要に応じて調整します。
- 材料の硬さや加工形状に応じて適切なバイトを選定します。
- 再加工前の準備:
- 折れたバイトによるダメージがワークになかったかを確認し、必要に応じて再加工を行います。
- 機械の調整やメンテナンスを再確認します。
- 徐々に負荷をかけてテスト:
- 新しいバイトで少ない負荷から始め、徐々に通常の作業条件に戻していきます。
- 短期間に同じ問題が再発しないかを注意深く観察します。
バイトが折れるという事故は、高価な機械やワークへのダメージにつながるため、適切な訓練とメンテナンスが事故の予防には不可欠です。また、作業者の安全にも注意を払うことが重要です。
適切なねじ切り旋削チップの選定
適切なねじ切り旋削チップを選定する際には、以下のポイントを考慮することが重要です。これらの要素は、ねじ切り作業の精度と効率、工具寿命に大きく影響します。
- ねじのタイプとサイズ:
- ねじの種類(メートル並目、ユニファイ、管用テーパーなど)によって適切なプロファイルのチップが異なります。
- ねじのサイズに応じて、チップのサイズや形状を選びます。
- 材料の種類:
- 加工する材料(鋼、ステンレス鋼、アルミニウム、非鉄金属など)によって適切なチップの材質とコーティングが異なります。
- チップの形状:
- フルプロファイルチップは、ねじ山の完全な形状を一度に切削できるため、高精度が要求される場合に適しています。
- パーシャルプロファイルチップは、異なるピッチのねじに対応可能で、柔軟性が高いです。
- コーティング:
- チップには、耐摩耗性や耐熱性を向上させるためにさまざまなコーティングが施されています。TiN、TiCN、TiAlNなどが一般的です。
- コーティングの選択は、加工する材料の種類や加工条件によって異なります。
- 耐久性とコスト:
- チップの耐久性とコストを考慮し、経済的な選択を行います。初期コストが高くても、長寿命のチップが総合的にコスト効率が良い場合もあります。
- メーカーの推奨と技術サポート:
- 各メーカーが提供する技術データやカタログを参照し、推奨されるチップを選定します。
- 必要に応じてメーカーの技術サポートに相談し、最適なチップを選択します。
適切なチップを選ぶことで、ねじ切り作業の品質を保ちながら生産効率を向上させることができます。また、不適切なチップの使用は工具の早期摩耗や製品の不良を引き起こす可能性があるため、慎重な選定が求められます。
親ねじとハーフナットの遊びと噛み合い
親ねじとハーフナットの遊びや噛み合いのトラブルは、ねじ切りの精度に直接影響を与えます。まず、遊びが大きい場合、ねじ山の形状が正確に形成されず、精度が低下します。これを防ぐためには、機械の調整が必要です。
親ねじとハーフナットの基本概念
- 親ねじ:機械的な動作においてネジ軸またはリードスクリューとして機能するねじ部分です。
- ハーフナット:親ねじに一致する内部ねじを持つ、二つに分割可能なナットのことで、通常は線形運動や位置決めに使用されます。
噛み合い
- 親ねじとハーフナットの噛み合いは、精度と反応速度を確保するために非常に重要です。噛み合いが正確であれば、スライド動作がスムーズで、バックラッシュが少なくなります。
- ハーフナットは通常、親ねじに対して簡単に嵌合および離脱できるように設計されています。これにより、ツールチェンジや位置調整が迅速に行えます。
遊び(バックラッシュ)
- バックラッシュ:親ねじとハーフナット間の隙間や「遊び」とも呼ばれ、ネジとナット間に存在するわずかな動きの余地を指します。この遊びは意図的に設定されることもあり、過度の摩耗や熱膨張による詰まりを防ぐために重要です。
- 適切なバックラッシュを設定することで、装置の精度を保ちつつ、部品の長期間にわたる信頼性を確保することができます。
定期的なメンテナンスを行い、ハーフナットの状態を確認します。そして、適切なタイミングで部品の交換を行います。これにより、常に良好な噛み合いを保ち、ねじ切りの精度を維持します。また、噛み合いが異常な場合には、潤滑を適切に行うことも効果的です。潤滑が不足していると、摩擦が増し機械の性能が低下するためです。
チッピングの問題
チッピングは、工具の刃先が欠けることを指し、切削の精度や仕上がりに大きな影響を与えます。主な原因は過負荷、適切でない工具選定、切削条件の不適切さです。これらの要因を見直し、適正な条件を選定することが必要です。
チッピングの原因
- 不適切な切削条件:切削速度、送り速度、または切削深さが適切でない場合、工具への過負荷がチッピングを引き起こす。
- 工具の選択ミス:材料や加工タイプに不適合な旋削チップを使用すると、刃先の損傷が生じやすくなります。
- 潤滑不足:十分な冷却液や潤滑剤が供給されない場合、摩擦熱が増加してチップが欠けやすくなります。
- 工具の摩耗:過剰な摩耗は切削エッジの脆弱化を招き、突然のチッピングを引き起こすことがあります。
- 振動と安定性の問題:機械の振動や不安定なクランプが切削中の衝撃を増大させ、チッピングのリスクを高めます。
チッピングへの対策
- 切削条件の最適化:材料と加工タイプに応じて、切削速度や送り速度を調整します。また、浅い切削深さで徐々に材料を削ることが推奨されます。
- 適切な工具選択:加工する材料に最適な旋削チップやホルダーを選択し、定期的に交換して鋭利な刃を保ちます。
- 適切な潤滑と冷却:充分な冷却液を使用して工具と加工面の間の摩擦を最小限に抑え、熱を効果的に排除します。
- 振動の管理:機械のメンテナンスを行い、安定したクランプと適切な設定で振動を抑えます。
- 段階的な加工:大きな切り込みを避け、段階的に材料を削除することで、工具へのストレスを軽減します。
定期的な機械の点検とメンテナンスも忘れずに行うことが重要です。
旋盤ねじ切り・旋削チップの選び方
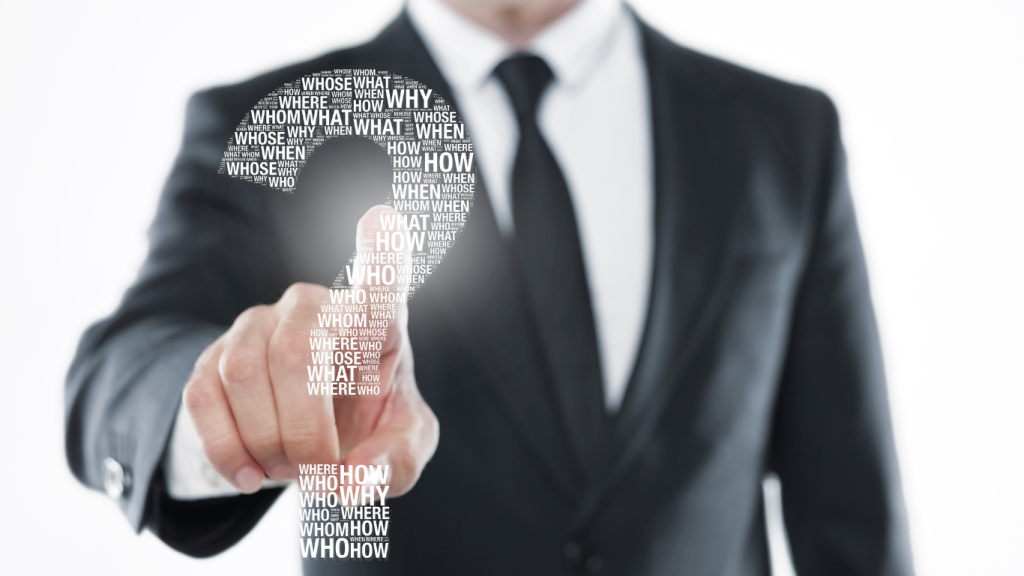
旋盤ねじ切りや旋削作業において、チップ選びは非常に重要です。適切なチップを選ぶことで作業効率が向上し、製品の品質も高まります。まず、素材と目的に応じたチップを選定することが基本です。
各チップには固有の特性があり、それぞれの用途に最適なものを選べば、作業が安定します。メーカーの推奨設定やカタログ情報を参考にするのも良いです。
マルチポイントチップ
マルチポイントチップは、旋削加工やねじ切り加工に使用される工具の一種で、一つのチップに複数の切削点を持たせたものです。これにより、一回のパスで複数のねじ山を同時に形成することが可能となり、加工効率が大幅に向上します。以下にマルチポイントチップの特徴と利点を説明します。
特徴
- 複数の切削エッジ:通常のシングルポイントチップに比べ、マルチポイントチップは複数の切削エッジを有しており、これにより同時に複数のねじ山が切削されます。
- 高効率加工:複数のエッジが同時に材料を削るため、加工時間が短縮され、生産性が向上します。
- 耐摩耗性:マルチポイント設計により、各エッジへの負荷が分散されるため、工具の耐摩耗性が向上し、長寿命化が期待できます。
利点
- 加工速度の向上:複数のポイントが同時に加工するため、シングルポイントチップを使用する場合に比べて加工速度が速くなります。
- 生産効率の改善:工具の交換頻度が減少し、連続運転時間が長くなるため、生産ラインの効率が向上します。
- コスト削減:工具の寿命が延びることで、工具コストが削減されます。また、高速加工が可能になるため、機械の運転コストも削減できます。
使用場面
- 量産環境:同じ仕様のねじを大量に製造する場合、マルチポイントチップの効率の良さが特に有効です。
- 自動旋盤:NC制御された自動旋盤での使用に適しており、高精度なねじ加工が求められる場面でよく使用されます。
注意点
- 設定の精度:マルチポイントチップを使用する場合、切削条件(切削速度、フィード率、切削深さなど)を正確に設定する必要があります。不適切な条件では、ねじ山の品質が損なわれることがあります。
- 専門知識:マルチポイントチップを最大限に活用するためには、高度な技術知識と経験が必要です。適切なトレーニングと経験を積んだオペレーターによる管理が望ましいです。
仕上げ刃なし(V形状)
仕上げ刃なし(V形状)の旋削チップは、特定のねじ切り作業において非常に有効です。このタイプのチップは、ねじ山の頂点を完全に形成しないため、刃先の負担を軽減し、より長いツール寿命を実現することができます。具体的には、以下のような特性を持っています。
特徴と利点
- 柔軟性: 仕上げ刃なし(V形状)チップは、同じ角度とコーナー半径であれば、異なるピッチのねじにも適用可能です。これにより、工具の汎用性が高まり、複数のねじサイズに対応するために多くのチップを用意する必要がなくなります。
- バリ発生のリスク: ねじ山の頂点を切削しないため、加工後のバリが少なくなりますが、一部のケースでは、ねじ山の頂点にバリが残ることもありますので、後処理が必要になる場合があります。
- 切削抵抗: 刃先が小さいため、切削抵抗が低くなり、より滑らかな切削が可能です。しかし、小さな刃先は摩耗しやすく、工具寿命が短くなる可能性があります。
- コスト効率: 刃物の本数を減らすことができるため、工具コストの削減に寄与します。
使用場面
- 多様なピッチのねじ加工:このチップは、同一の角度とコーナ半径で複数のピッチに対応できるため、さまざまなねじピッチの加工が頻繁に行われる環境で有効です。これにより、工具の交換を頻繁に行う必要がなくなり、生産性を向上させることができます。
- 量産環境:量産環境では、生産効率とコスト削減が重要です。仕上げ刃なしチップを使用すると、工具の交換回数が減少し、工具コストが削減されます。また、これらのチップは少ない切削抵抗でスムーズに加工できるため、機械の摩耗を減らし、メンテナンスコストも削減できます。
- 粗加工用途:ねじの粗加工段階で使用すると効果的です。頂点を切削しないため、加工中の負荷を軽減し、その後の仕上げ工程で細かい調整を行う余地を残します。これにより、仕上げ工程での精度を向上させることができます。
- バリが問題となる加工:ねじ山の頂点を切削しないため、バリの発生を抑えることができます。これは、後工程でのバリ取り作業の手間を減らし、製品の品質を保つのに役立ちます。
マルチポイントチップ
マルチポイントチップは、複数の切削点を持つ旋削チップで、一度に複数のねじ山を形成することができるため、生産性を大幅に向上させることができます。以下はその特徴とメリット、および使用場面です。
特徴とメリット
- 高い生産性:複数の切削点があるため、一回のパスで多くのねじ山を同時に加工できます。これにより加工時間が大幅に短縮され、高い生産効率を実現します。
- 工具寿命の向上:切削負荷が複数のポイントに分散されるため、個々の刃の摩耗が減り、工具寿命が延びます。
- 優れた仕上がり:均一な切削が可能で、ねじの品質が向上します。特に精密なねじ加工に適しています。
使用場面
- 大量生産:同じ仕様のねじを大量に製造する工業製品の生産ラインでよく使用されます。自動車部品や家電製品の組み立てなど、一貫生産が求められる場面で特に効果的です。
- 高精度加工:航空宇宙産業や医療機器など、精度が極めて重要なアプリケーションで使用されることがあります。マルチポイントの均一な切削により、高い寸法精度と良好な表面仕上がりが得られます。
切削力とツールのメンテナンス
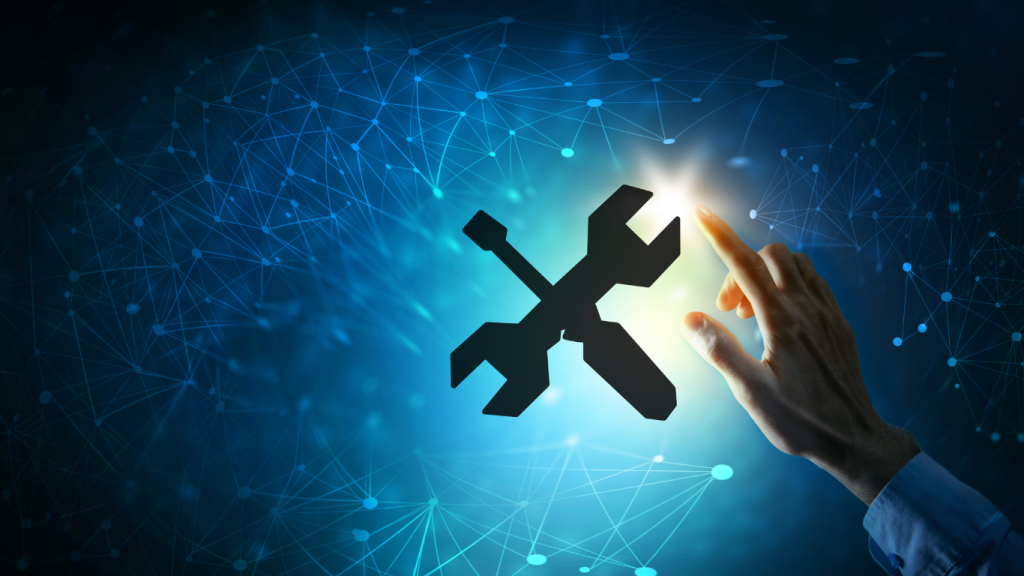
切削力とは、切削工具が材料を加工する際に発生する力であり、切削工具の耐久性や加工精度に大きな影響を及ぼします。適切な切削力の管理とツールのメンテナンスは、効率的で品質の高い加工を維持するために重要です。以下に詳しく解説します。
切削力の影響
- 切削抵抗の増加:切削力が大きいほど、ツールにかかる負荷が増加し、摩耗が早く進行します。
- ねじれや変形のリスク:材料が弾力性を持つ場合、過剰な切削力によって材料がねじれたり変形したりすることがあります。
- 加工精度の低下:切削力が不均一だと、仕上がりの表面が不均一になる可能性があります。
ツールのメンテナンスの重要性
- 刃の状態を常にチェック:切削工具の刃が鈍ると、必要な切削力が増加し、加工品質が低下するため、定期的な検査と交換が必要です。
- クリーニングと潤滑:切削工具と加工物の間で発生する熱を軽減するために、工具を清潔に保ち、適切な潤滑油を使用することが重要です。
- 適切な設定と調整:切削条件(切削速度、送り速度、切削深さ)を適切に設定し、ツールが最適な状態で動作するよう調整します。
切削力を適切に管理する方法
- 切削条件の最適化:材料の種類や加工の目的に応じて、切削速度や送り速度を調整し、切削力を適切な範囲内に保ちます。
- 高品質のツール使用:高品質の切削ツールを使用することで、切削力を効率的に伝達し、耐久性を高めることができます。
- 技術的なトレーニング:操作者が切削工具の特性と適切な使用方法を理解していることが、効果的な切削力の管理とツールの適切なメンテナンスには不可欠です。
適切な切削力の管理と工具のメンテナンスを行うことで、切削作業の効率を向上させ、工具の寿命を延ばし、最終製品の品質を保つことができます。
まとめ
旋盤ねじ切りの過程は、正確さと緻密な計画が求められる技術です。この記事を通じて、ねじ切りの基本から計算方法、トラブルシューティングに至るまでの情報を提供しました。
これらの知識を生かし、実際の作業で適切な判断を下すことが、より良い製品を作り出すための一歩となります。正確な作業と工具のメンテナンスに注意を払うことで、旋盤ねじ切りの技術を深め、多様な製造課題に対応する力を身につけることができます。
お問い合わせ
弊社製品、加工についてのお問い合わせは、こちらで受付しております。
各部門のスペシャリストが、ご質問にお応えします。
電話
0574-54-2231
(平日 8:15~17:15)
FAX
0574-54-2235