- 2024/06/04
-
旋盤加工におけるバイト刃物の種類・特徴・選び方を紹介!
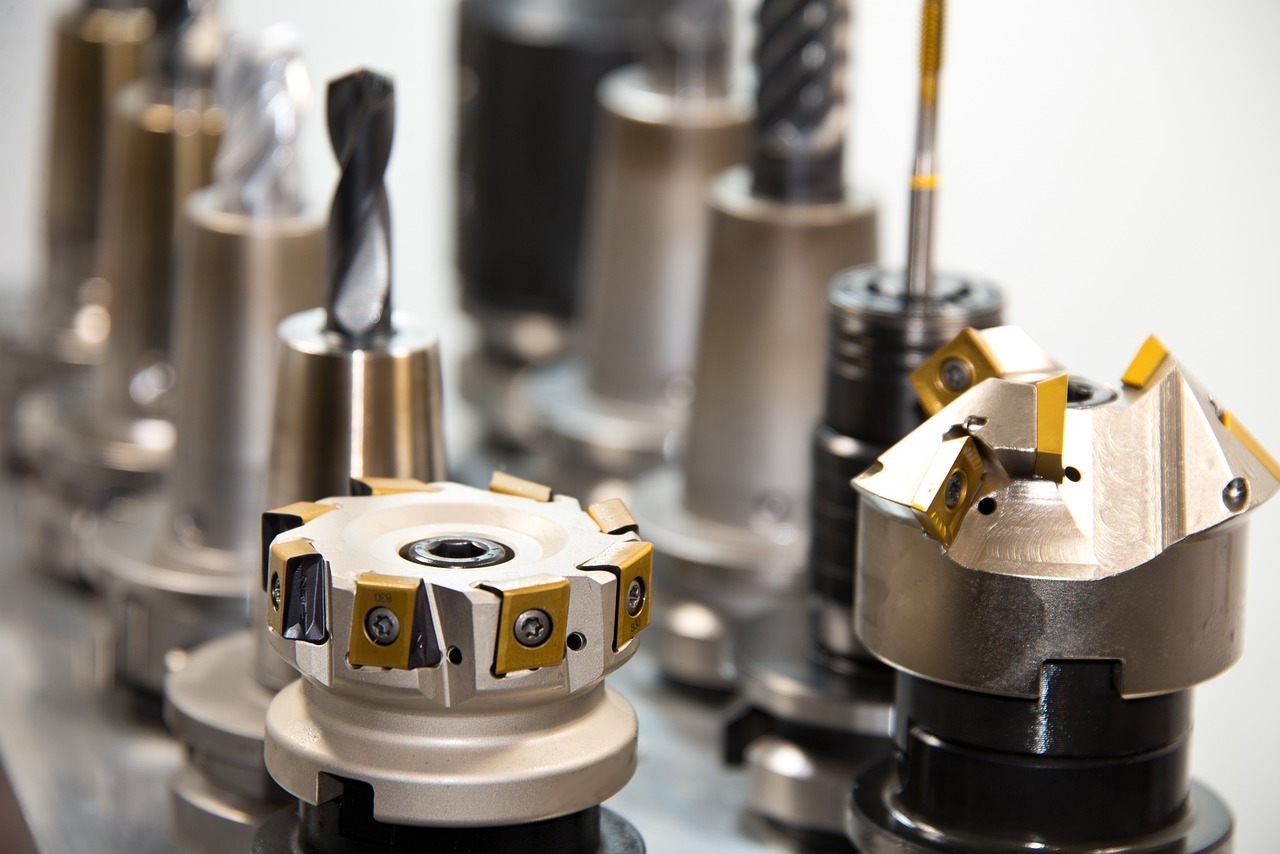
旋盤作業において、バイトの選定は仕上がりの精度と作業効率に大きく影響します。適切なバイトを選ぶことで、加工精度の向上や製品品質の安定が図れるだけでなく、作業全体の効率も向上します。
本記事では、バイトの種類やその選定方法を詳しく解説し、最適なバイト選びのポイントをご紹介します。
目次 [hide]
バイトの種類・分類や呼び方
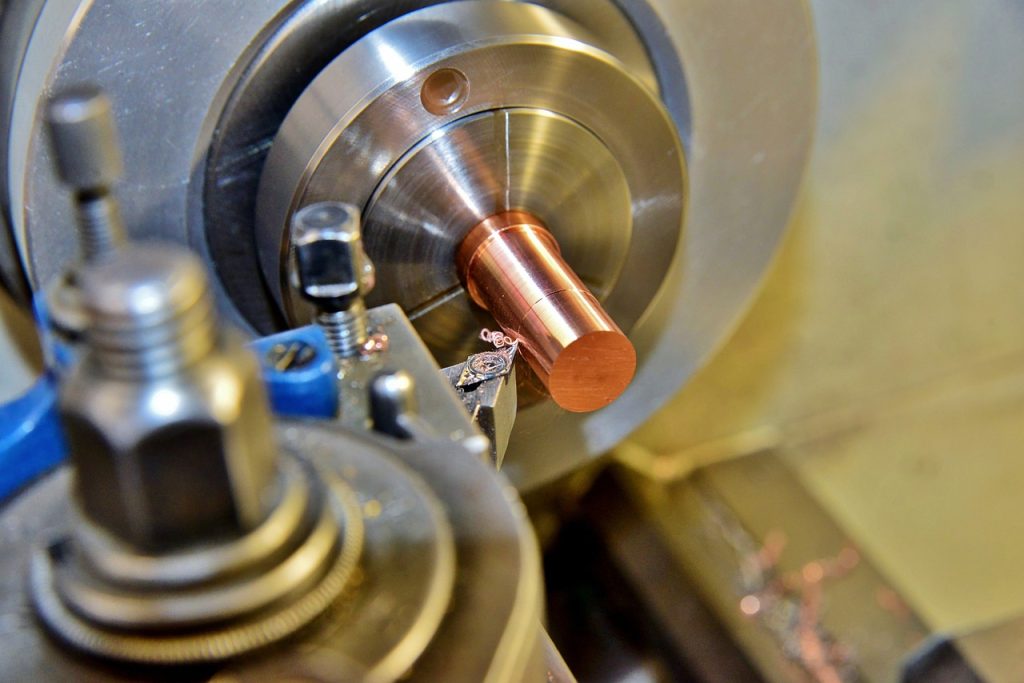
「バイト」とは、旋盤やフライス盤などで使用される切削工具のことです。
バイトの役割は、材料を削ったり切断したりすることですが、用途や形状、構造によってさまざまな種類や呼び方が存在します。
ここでは、さまざまなバイトの種類・分類を紹介します。
バイトの構造による分類
旋盤バイトは、その構造の違いから3種類に分けることができます。
名称 | 特徴 |
---|---|
ムクバイト | ・完全バイトとも言う ・刃とシャンクが一体となっている ・刃先の再研磨が可能で汎用性が高く、特殊な切削にも対応できる ・刃先の成形には技術が必要 ・主に炭素工具鋼や合金工具鋼製で、研磨により再利用が可能 |
付刃バイト | ・ろう付けバイトとも言う ・刃先とシャンクが別で、シャンクに刃先を溶着したバイト刃先の成形してからでないと 使用できない ・刃先を成形する必要があるため初心者向きではない |
スローアウェイバイト | ・クランプバイトとも言う ・刃先とシャンクが別パーツの旋盤バイト ・シャンクに刃先(チップ/インサート)をねじで取り付ける構造になっている ・切れ味低下時は刃先交換で再使用可能 ・研磨不要で使いやすい ・使いやすさから現在の主流タイプになっている |
以下の動画では一般的なバイトの紹介がされていますので、こちらも参考になさって下さい。
使用方法・形状による分類
旋盤用バイトは、内径加工、外形加工、溝入れ、突っ切り、ねじ切り、端面加工など、さまざまな加工に使用されます。これらの加工の種類に応じて、使用されるバイトの形状や構造が異なってきます。
以下では、加工の形状や使用方法によってバイトを分類しています。
名称 | 特徴・使用法 |
---|---|
剣バイト | ・刃先が剣のように尖っている ・剣バイトには真剣バイト(刃先が左右対称)、 先丸剣バイト( 刃先が少し丸くなっている)、 斜剣バイト( 刃先が左右非対称)、 平剣バイト(刃先がシャンクと直角になっている) といった種類がある ・剣バイトは主に外径削りや端面加工で使用され、 平剣バイトは立旋盤やプレーナーなどの平削り盤でも活躍する |
片刃バイト | ・シャンクと平行な切刃を持つ汎用性の高い旋削バイト ・外径加工や端面加工など、旋盤作業の基本的な加工に広く使用される |
突っ切バイト | ・円筒形の素材の外周から溝入れを行ったり、切断する際に使用される |
ねじ切りバイト | ・ねじ山を作る際に使用する・おねじ用、めねじ用がある |
中ぐりバイト | ・円筒形素材の内径加工に使用する・ボーリングバイトとも呼ばれる |
センタードリル | ・ワークの端面にセンター穴を開けるための工具 |
ヘールバイト | ・びびり、食い込みを避けるため、シャンクがRの形状になったバイト |
勝手(刃の方向)による分類
バイトには、勝手、つまり、刃のついている方向による分類もあります。
以下は、勝手による分類を表にまとめたものです。
勝手 | 特徴 |
---|---|
右勝手 | 作業者から見て刃先が左を向き、被削材の右側から切削する |
左勝手 | 作業者から見て刃先が右を向き、被削材の左側から切削する |
勝手なし | 向きが無く、両側から切削できる |
右勝手バイトは、一般的な右利きの作業者向け、左勝手バイトは左利きの作業者や特定の加工条件に合わせたものとなっています。
その他の条件による分類
構造、形状や使用方法、勝手の他にも、シャフトの形状の違いや刃部の材質の違いによっても、さらに細かく分類されています。
以下の表は、上記分類とも重複する箇所がありますが、購入先によっては以下の名称で呼ばれることもあるので、覚えておくと便利です。
名称 | 特徴 |
---|---|
剣バイト | :先端が尖った形状で、すくい面側から見ると真っ直ぐな形状のバイトの総称 |
両刃剣バイト | :シャンクの両端に切れ刃を持つ剣バイト |
真剣バイト | :左右対称な切れ刃を持つ剣バイト |
先丸剣バイト | :左右対称な切れ刃と大きな丸コーナーを持つ剣バイト |
斜剣バイト | :左右非対称な切れ刃を持つ剣バイト |
平剣バイト | :主切れ刃がシャンクの軸にほぼ直角な剣バイト |
曲がりバイト | :シャンクの軸に対して左右どちらかに曲がった刃部を持つバイトの総称 |
右曲がりバイト | :右利き用の曲がりバイトで、刃先角は約60°、アプローチ角は約-20° |
左曲がりバイト | :左利き用の曲がりバイトで、刃先角は約60°、アプローチ角は約-20° |
先丸曲がりバイト | :大きな丸コーナーを持ち、刃先角は約40°、アプローチ角は約-30°の曲がりバイト |
平曲がりバイト | :刃先角は約90°、アプローチ角は約25°の曲がりバイト |
向きバイト | :刃先角は約90°、アプローチ角は約45°の曲がりバイト |
片刃バイト | :シャンクの軸にほぼ平行な切れ刃を左右どちらか片方だけに持つバイト |
腰折れバイト | :コーナの高さがシャンクの底面と一致するか、 底面より低くなるように首を曲げたバイトの総称 |
ヘールバイト | :切削時の振動を吸収するために、ばねのように首を曲げたバイトの総称 |
直速度(工具)鋼バイト | :刃部の材料に高速度工具鋼を使用したバイト |
超硬バイト | :刃部の材料に炭化タングステンを主体とした焼結体である超硬合金を使用した バイト |
サーメットバイト | :刃部の材料にチタンやタンタルの炭化物、炭窒化物、窒化物を主体とした 焼結体であるサーメットを使用したバイト |
セラミックバイト | :刃部の材料に酸化アルミニウムを主体とした焼結体であるセラミックを使用 したバイト |
CBNバイト | :刃部の材料に多結晶立方晶窒化ホウ素焼結体を使用したバイト |
ダイヤモンドバイト | :刃部の材料にダイヤモンドを使用したバイト |
PCDバイト | :刃部の材料に多結晶ダイヤモンド焼結体を使用したバイト |
コーティングバイト | :刃部の表面に炭化物、窒化物、酸化物、ダイヤモンドなどを 一層または多層にコーティングしたバイト、被覆バイトとも呼ばれる |
むくバイト | :刃部とシャンク、またはポデーが一体となった材料で作られたバイト |
付刃バイト | :チップをポデーにろう付けしたバイト |
溶接バイト | :刃部の材料とシャンクの材料を溶接して一体化させたバイト |
組立バイト | :刃部とシャンク、またはポデーを組立構造としたバイトの総称 |
差し込みバイト | :ブレードをホルダに差し込んで締め付けて使用する組立バイト |
クランプバイト | :チップまたはブレードをホルダまたはポデーに機械的に 締め付けて使用する組立バイトの総称 |
カートリッジ | :取り付け位置の微調整が可能な小型のクランプバイト |
スローアウェイバイト | :チップにスローアウェイチップを使用したクランプバイト |
組合せバイト | :複数のバイトを組み合わせて一体化させたバイト |
平削り盤用バイト | :主に平削り盤や形削り盤などで使用されるバイトの総称 |
立削り盤用バイト | :主に立削り盤で使用されるバイトの総称、スロッタバイトとも呼ばれる |
中ぐり盤用バイト | :主に中ぐり盤で使用されるバイトの総称 |
方形シャンクバイト | :シャンクの軸に垂直な断面が正方形になっているバイト |
長方形シャンクバイト | :シャンクの軸に垂直な断面が長方形になっているバイト |
台形シャンクバイト | :シャンクの軸に垂直な断面が台形になっているバイト |
丸シャンクバイト | :シャンクが円筒状になっているバイト |
テーパシャンクバイト | :シャンクが円錐状になっているバイト |
三角形シャンクバイト | :シャンクの軸に垂直な断面が三角形になっているバイト |
ひし形シャンクバイト | :シャンクの軸に垂直な断面がひし形になっているバイト |
穴付きバイト | :取り付け部に穴があるバイト |
ねじ付きバイト | :シャンクまたは取り付け穴にねじ山が切られているバイト |
ダブテールバイト | :シャンクまたはポデーのホルダとの嵌合部分が蟻溝状になっているバイト、 片側だけのものもある |
総形バイト | :刃形の輪郭を工作物の形状の一部に転写して加工するバイトの総称 |
ロールバイト | :ロール旋盤などで圧延ロールの穴形を成形する際に使用される総形バイト |
タイヤバイト | :車輪旋盤などで車輪の外周を成形する際に使用される輪形バイト |
クランクバイト | :クランク軸のジャーナルまたはピンの切削に使用する総形バイト |
多刃バイト | :複数の切れ刃で同時に切削を行うバイト |
サーキュラバイト | :取り付け穴またはシャンクを持つ円板状のバイト、外周の一部に切れ込みを入れて 主切れ刃としたもの。主に総形バイトとして使用される |
完成バイト | :熱処理済みのむくの高速度工具鋼製バイトで、端面以外が研削されており、 使用する際に刃部を成形してから使用される |
方形バイト | :方形シャンクの完成バイト |
長方形バイト | :長方形シャンクの完成バイト |
板バイト | :幅の狭い長方形シャンクの完成バイト |
逃げ付き板バイト | :横逃げ角を付けた台形シャンクの完成バイト |
ステッキバイト | :ホルダに対して角度のある取り付け部を持つ台形シャンクの完成バイト |
丸バイト | :丸シャンクの完成バイト |
荒削りバイト | :荒削り工程で使用されることを目的としたバイト、一般的に重切削に 耐えられる形状や寸法で、切屑処理を考慮した形状になっている |
仕上げバイト | :仕上げ工程で使用されることを目的としたバイト、一般的に良好な仕上げ面を 得られるように考慮されている |
突切りバイト | :切落しや幅の狭い溝削りに使用するバイトの総称 |
逆突切りバイト | :下向きに刃物台に取り付けて使用する突切りバイト |
中突切りバイト | :主切れ刃がシャンクの軸に対して対称にある突切りバイト |
ヘール突切りバイト | :切落しや溝削りに使用するヘールバイト |
ヘール仕上げバイト | :比較的広い工作物の面に良好な仕上げ面を得るために使用するヘールバイト |
トレパンバイト | :工作物の回転軸に平行に端面から送り、心残し削りに使用するバイト、 縦突切りバイトや親子取りバイトとも呼ばれる |
溝削りバイト | :溝削りに使用するバイトの総称 |
リセッシングバイト | :内面の溝削りに使用するバイト |
穴ぐりバイト | :穴を旋削する際に使用するバイトの総称、一般的に長い首の先端に 曲がった刃部を持っている |
穴仕上げバイト | :シャンクの軸に平行な主切れ刃を持つ穴ぐりバイト |
穴ぐり荒バイト | :シャンクの軸に対して傾斜した切れ刃を持つ穴ぐりバイト |
先丸穴ぐりバイト | :大きな丸コーナーを持つ穴ぐりバイト |
中ぐりバイト | :中ぐり棒に取り付けて使用する小型のバイト |
面削りバイト | :面削りに使用するバイトの総称 |
ねじ切りバイト | :ねじ切りに使用するバイトの総称 |
おねじ切りバイト | :おねじを切る際に使用するバイト |
めねじ切りバイト | :めねじを切る際に使用するバイト |
ヘールねじ切りバイト | :おねじを切る際に使用するヘールバイト |
総形ねじ切りバイト | :ねじ山形状の刃形を持ち、ねじ切りに使用する総形バイト |
サーキュラねじ切りバイト | :外周にねじ山形状の刃形を持ち、ねじ切りに使用するサーキュラバイト |
キー溝バイト | :キー溝を掘る際に使用するバイト |
面取りバイト | :工作物の鋭い角を面取りする際に使用するバイトの総称 |
座ぐりバイト | :工作物の鋭い角を面取りする際に使用するバイトの総称 |
回転バイト | :丸駒バイトを回転できるようにホルダに取り付けて使用する組立バイト、 主運動と送り運動の組み合わせによって受動的に回転するものと、 強制的に回転させるものがある |
タンジェンシャルバイト | :バイトの主運動の方向と送り運動の方向を一致させて使用するバイトの総称 |
シェーピングバイト | :前加工で工作物に残った凹凸を取り除き、仕上げ面粗さを向上させるために 使用するタンジェンシャルバイト |
スカイピングバイト | :大きなすくい角と切れ刃傾斜角を持ち、1回の接線送りで目的の輪郭寸法を得る ために使用するタンジェンシャルバイト |
ローラターナバイト | :片持ちの長い棒材を2つのガイドローラで振れを抑えながら外周を旋削する際に 使用するバイト |
トリマバイト | :鋼板や鋼管などの溶接部の余肉やビードかすなどを除去して滑らかにする際に 使用するバイト、かす取りバイトとも呼ばれる |
ピーリングバイト | :鋼材の皮むき専用機などの回転するホルダに取り付けて皮むきに使用するバイト |
現在の主流であるスローアウェイバイトとは?
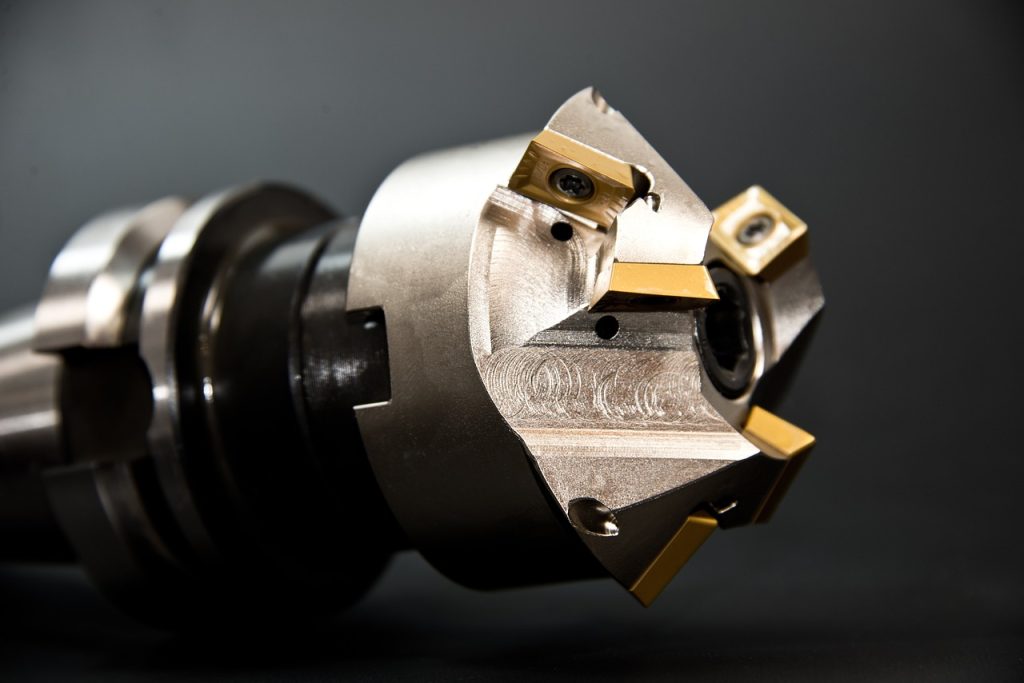
スローアウェイバイトは、利便性が高く、現在最も広く使われている旋盤バイトです。
以下に、このバイトの特徴や構造について、より詳しく説明していきます。
スローアウェイバイトの特徴
スローアウェイバイトが現在、最も広く使われているその最大の理由は、チップ交換の利便性にあります。チップが摩耗したり破損した場合でも、工具全体ではなくチップのみを交換すれば再び使用できます。
これは、従来の旋盤バイトのように工具全体を研磨する必要がないため、作業効率の向上とコスト削減に大きく貢献します。また、様々な形状や材質のチップが用意されているため、用途に応じて最適な刃先を選ぶことができます。
使い方も比較的簡単であることから、初心者からベテランまで幅広く利用されています。
スローアウェイバイトの構造
スローアウェイバイトは、シャンクとチップが分離した構造をしています。
- シャンク: 工具の持ち手部分
- チップ: 実際に切削を行う部分で、すくい面、逃げ面、切れ刃、コーナRなどから構成され、それぞれが加工精度や切れ味に影響を与える
- ボディー: シャンクに設けられた、チップを固定するための座を含めた部分
チップはボディーに機械的に固定され、容易に取り外しが可能です。この構造により、摩耗したチップだけを簡単に交換できるため、スローアウェイバイトは高い利便性と経済性を実現しています。
スローアウェイバイトに使われるチップの種類
スローアウェイバイトに取り付けることのできるチップにはさまざまな種類があり、それらは材質や形状によって分類されます。
チップの材質による分類
スローアウェイバイトのチップに使用される素材は、主に以下の9種類です。
- ハイス
- 超硬合金
- PVDコーティング超硬合金
- CVDコーティング超硬合金
- サーメット
- セラミックス
- CBN
- ダイヤモンド
- PCD
これらの中でも、最も一般的に使用されているのは超硬合金製のチップです。
超硬合金は「硬さ」と「粘り強さ」の両方を兼ね備えているため、多様性があります。
超硬合金チップは、記号と色で識別できるように規格化されており、それぞれのアルファベットと色が被削材に適したチップを選ぶ目安となります。
以下の表にその詳細をまとめました。
材質 | 記号 | 色 | 特徴 |
---|---|---|---|
鉄鋼 | P | 青 | 硬さと粘り強さがバランス良い |
ステンレス鋼 | M | 黄 | 腐食に強い |
アルミニウム合金 | N | 緑 | 軽く、柔らかい |
鋳鉄 | K | 赤 | 硬く、脆い |
チタン合金 | S | 茶 | 軽くて強度が高い |
焼入れ鋼 | H | 灰 | 硬度が非常に高い |
チップの形状による分類
チップはその形状により、被削材との近接性に相違があります。主なチップの形状には以下の種類があります。
- 円形
- ひし形35°
- ひし形55°
- ひし形80°
- 正三角形60°
- 正方形90°
- 六角形80°
刃先角度が大きくなるとチップの強度は増しますが、その反面、切削中の振動が起こりやすくなります。
チップブレーカーとは?
チップブレーカーとは、切削作業中に発生する切りくずを細かく分断するための、チップの溝や突起のことを指します。
切りくずが長くなると絡まりやすくなり、作業効率が低下し、作業者にも危険を及ぼす可能性があります。チップブレーカーを使うことで、切りくずが細かく分断され、安全で効率的な切削作業が可能になります。
以下の動画では、チップブレーカーの有無によって切屑がどのように分断されているかが良くわかります。
チップブレーカーの形状
チップブレーカーにはさまざまな形状があり、それぞれの形状によって切りくずの分断効果が異なります。主な形状としては以下のようなものがあります。
- V字型ブレーカー:溝がV字型に掘られており、切りくずを中央に集めて分断する効果がある
- U字型ブレーカー:溝がU字型に掘られており、切りくずを滑らかに流しつつ分断する効果がある
- 凸型ブレーカー:チップのすくい面に突起が設けられており、切りくずが突起に当たって折れ曲がり分断される
逃げ角による分類
逃げ角とは、工具が材料に触れる部分での摩擦を減らし、刃先がスムーズに材料を削れるようにする角度のことです。
逃げ角を大きくすると、工具と被削材の間の摩擦が減少し、切削性能が向上します。これは特に柔らかい材料の加工に適しています。一方で、逃げ角が大きすぎると刃先の強度が低下し、工具が破損しやすくなります。
逆に、逃げ角を小さくすると刃先の強度が向上し、硬い材料の加工や重切削条件に適します。ただし、小さすぎる逃げ角は工具と被削材の摩擦を増加させ、工具寿命を短くする可能性があります。
逃げ角の形状により、チップはネガチップとポジチップに分類され、以下のような表にまとめることができます。
チップの種類 | 逃げ角の特性 | 刃先強度 | 適用用途 |
ネガチップ | 先端形状90° (逃げ角なし) | 刃先強度が高い | 重切削に適している |
ポジチップ | 先端形状90°より小さい (逃げ角あり) | 切削抵抗が小さい | 内径加工などに適している |
適切な逃げ角の選択は、被削材の硬さや加工条件に応じて行うことが重要です。
スローアウェイバイトに用いられるバイトホルダーとは?
バイトホルダーは、切削加工においてチップ(取り替え可能な刃)を保持・固定するための装置です。この部品により、加工中もチップが安定的に固定され、切削作業の効率が向上します。
主なバイトホルダーの役割と特徴を以下のようになっています。
- チップを安定して固定する
- 切削加工の精度向上をサポートする
- チップの交換を容易にする
- 工具全体の寿命を延ばす
- 工具交換コストを削減する
バイトホルダーの種類
バイトホルダーは大きく外形加工用と、内径加工用に分類することができます。
以下にバイトホルダの種類について表形式でまとめます。
種類 | 特徴 | クランプ方式 | 用途 |
---|---|---|---|
外径加工用 ホルダー | 高剛性が特徴 さまざまな形状が ある | ねじ式、レバーロック式、 ピンロック式、押え金式 | 外径加工 |
内径加工用 ホルダー | 高剛性が必要 シャンク径や加工穴径に 注意が必要 | なし | 直線加工、 通し穴加工、 バックボーリング |
それぞれ特徴が異なるので、加工に応じて使い分けることが必要になります。
ホルダーの選び方
ホルダーを選ぶ際には、いくつかのポイントがあります。以下のようにステップバイステップで選んでいくと良いでしょう。
1.加工の種類を考える
- 外側を削る? → 外径加工用バイト
- 穴の内側を削る? → 内径加工用バイト
2.材料の硬さと切削の深さを確認
- 硬い材料や深く削る場合 → より強固なバイトホルダ
- 柔らかい材料や浅く削る場合 → 標準的なバイトホルダ
3.切り込み角(刃物が材料に当たる角度)を選ぶ
- 直角に近い仕上がりが必要 → 大きな切り込み角
- 斜めの仕上がりでOK → 小さな切り込み角
4.チップの固定方法(クランプ方式)を決める
- 頻繁にチップ交換する → レバーロック式(取り外しやすい)
- 小さな穴の加工 → ねじ式(小型のチップに適している)
5.内径加工の場合は追加で考慮
- 深い穴を加工 → より太いシャンク径(棒の部分)
- 振動が気になる → 超硬合金など、より硬い素材のバイトホルダ
バイトホルダを選ぶときは、まず加工の種類(外側か内側か)を決め、次に材料や切削条件を考慮します。その後、仕上がりの角度や作業のしやすさに合わせて細かい選択をしていきます。内側を加工する場合は、さらに穴の深さや振動の問題も考える必要があります。
適切なバイトホルダを選ぶことで、作業性が高まります。また工具の寿命も延びるので、効率的で経済的な加工ができるようになります。
旋盤加工の基礎とバイト刃物の役割
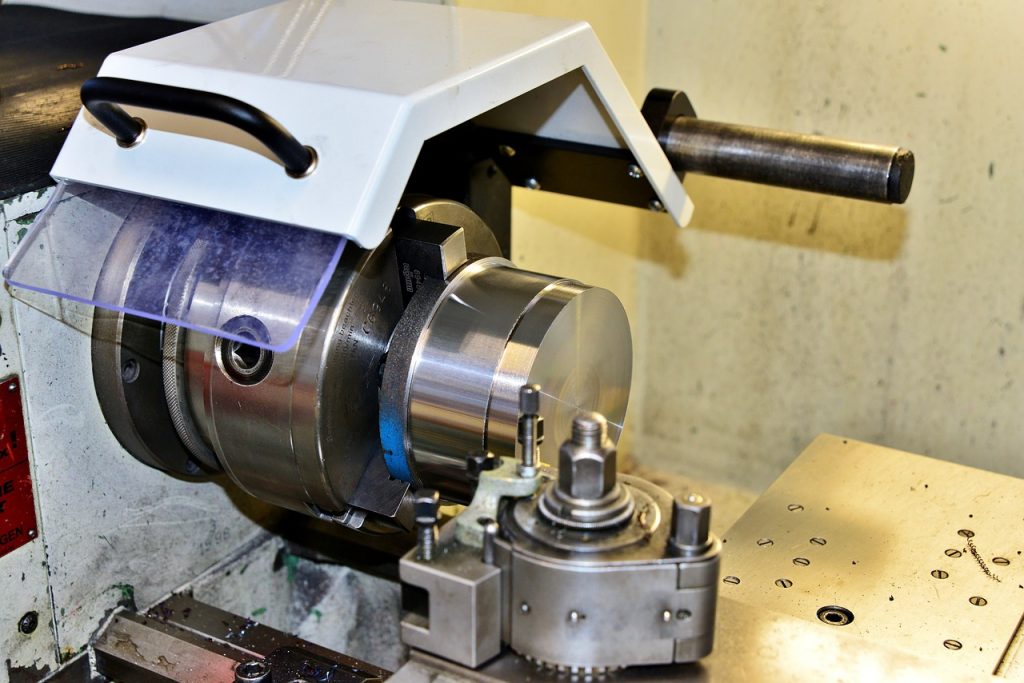
旋盤加工は金属の加工法の一つです。そして、旋盤加工にはバイト刃物が欠かせません。
ここでは、旋盤加工の基礎とバイト刃物がどのように重要なのかを説明しています。
旋盤加工とは?
旋盤加工は、工作機械の一種である旋盤を用いて行う金属加工技術です。
旋盤は素材を回転させ、その回転運動を利用してバイト刃物で加工物を削り出します。この方法によって、円筒状や円錐状の部品が高精度に加工されます。
旋盤加工は加工の精度が高いため、機械部品や工具などの製造に広く使用されます。
旋盤加工で使用されるバイトとは?
旋盤加工で使用されるバイトは、幾つかの部位から構成されています。
主に、刃先、シャンク、切り屑排出口などが挙げられます。刃先は材料と直接接触する部分で、シャンクはバイトを保持する部分です。切り屑排出口は加工中の切り屑を効率よく排出する役割を持っています。
それぞれの部位が正確に機能することで、効率的な加工が可能となります。
旋盤加工におけるバイト刃物の役割とは?
旋盤加工におけるバイト刃物の役割は、素材を効率的かつ精密に削ることです。
バイト刃物は、その形状や材質により、加工精度や耐久性に大きな影響を与えます。適切な刃物を選定することで、加工時間の短縮や仕上がりの向上が期待できます。
旋盤バイトを使用した旋盤加工の種類
旋盤バイトを使用した旋盤加工には、幾つかの種類があります。それらの種類と特徴を下記表にまとめました。
加工方法 | 特徴 |
---|---|
外径加工 | :材料の外側を削る。仕上げや形状作成に用いられる |
内径加工 | :穴を広げたり仕上げたりする。深い穴では工具のたわみに注意が必要 |
ねじ切り加工 | :ねじのピッチを作成。雄ねじと雌ねじの両方が加工可能 |
突切り加工 | :不要な部分を切り落とす。精度の高い加工には技術が必要 |
穴あけ加工 | :材料にドリルを当てて穴を開ける。内径加工前の準備として使用 |
これらの方法は組み合わせることで、複雑な形状の部品も作り出すことができます。
バイト刃物に使われる材料とその特性
バイト刃物の性能は、その材料によって大きく影響を受けます。切削速度、摩耗抵抗、熱耐性など、刃物に求められる特性はさまざまです。それらの特性を最大限に引き出すために、材料の選定が重要となってきます。以下では、代表的な刃物材料とその特性について詳しく説明します。
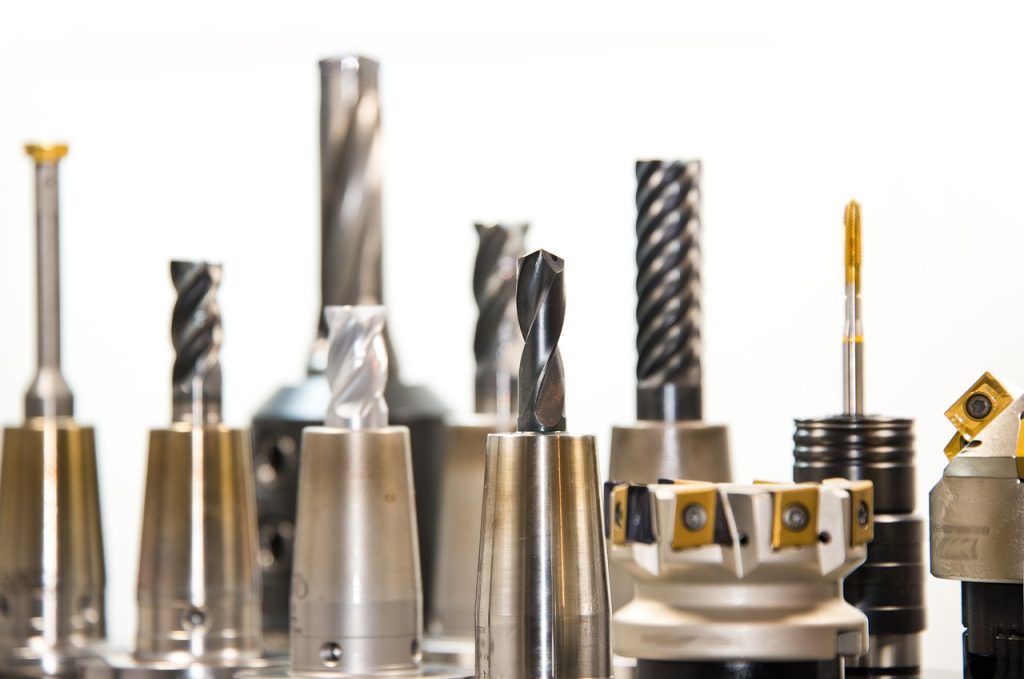
バイト刃物に使われる材料
バイトの材質として主に使われているのは、以下の3種類です。
- 超速度工具鋼
- 超硬合金
- セラミックス
これらの材質には、以下のような特徴があります。
材料 | 特徴 | 用途 |
---|---|---|
超速度工具鋼 | 高速での切削に適している比較的 安価耐熱性と耐摩耗性がある | 複雑な形状の加工や高速での切削が求められる 場面で頻繁に使用される |
超硬合金 | 非常に硬く、耐摩耗性に優れている 高速切削や長時間の使用に適している 超速度工具鋼よりも高価 | 高精度が求められるパーツの加工に選ばれる |
セラミックス | 超高速切削が可能非常に高い耐熱性 と耐摩耗性最も高価だが、特殊な 加工条件下で優れた性能を発揮 | 硬度の高い材料や耐熱合金の加工に使用される |
これらの材料は、加工する材料の種類や切削条件、コスト、要求される仕上がり品質などに応じて選択されます。
刃先のコーティングとは?
刃先コーティングとは、刃の表面に炭化物や窒化物、酸化物、ダイヤモンドなどを一層または多層で化学的または物理的に密着させる技術です。この技術により、刃物の寿命が長くなります。
またコーティングすることで、以下のようなメリットがあると言われています。
- 切削工具の寿命が延びる
- 加工面の面粗度が向上する
- 切り屑の排出性が向上する
- 耐熱性能が向上する
- 超硬素材の靱性を保ちつつ、耐摩耗性(高硬度)を大幅に改善する
- 工具費削減と工具交換回数の減少が可能
- 切削速度を高く設定でき、切削時間の短縮が可能
- 刃物がワークに溶着しにくくなる(構成刃先がつきにくくなる)
- フルート(溝)の滑りが良くなり、切り屑の排出がスムーズになり、切子詰まりによる破損やチッピングを防止できる
コーティングの種類として、TiN(窒化チタン)やAlTiN(窒化アルミチタン)などが一般的です。これらのコーティングは、耐摩耗性や熱耐性を高め、摩擦を軽減します。
技術の進化により、DLC(ダイヤモンドライクカーボン)など、さらに多くの種類のコーティングが開発されています。また、近年のコーティング技術では、コーティング層がより均一で密着性が高くなり、工具の寿命や性能が飛躍的に向上しています。
バイト刃物のメンテナンスと交換時期
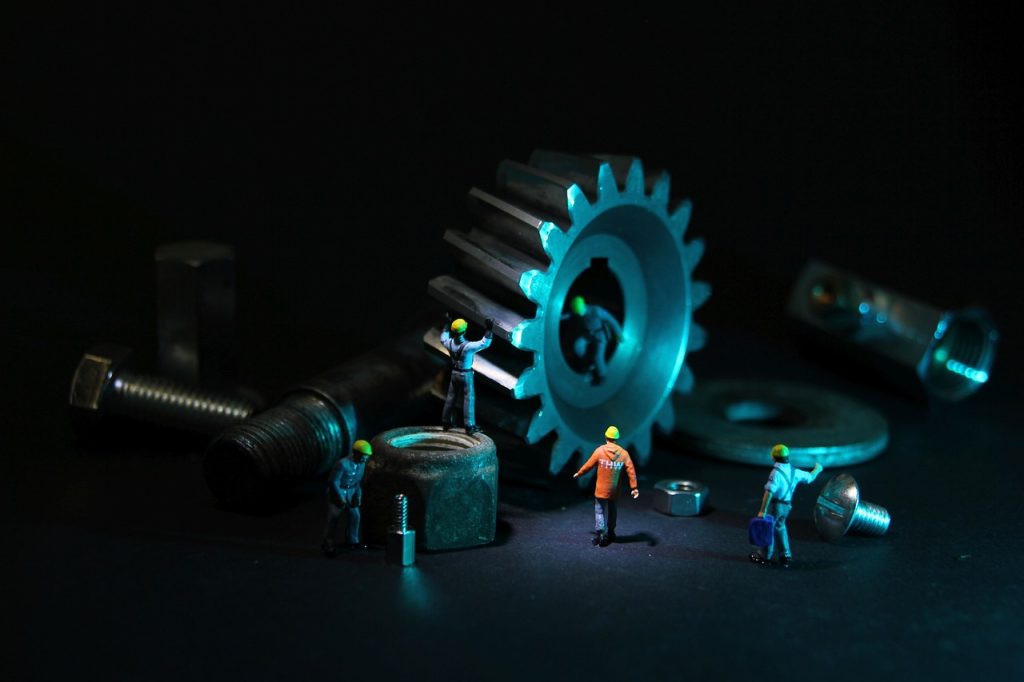
バイト刃物は、劣化や摩耗が進むと作業効率が低下します。そのため、定期的なメンテナンスと交換時期を策定することが必要になってきます。
刃先の劣化原因と対策
刃先の劣化原因には、摩耗、熱の影響、腐食などがあります。
摩耗は主に使用回数と加工材料によって進行します。特に硬い材料を加工すると、刃先が早く摩耗します。また、高速での加工は刃先に熱を持たせ、これが劣化の一因となります。この対策として、加工速度を適切に設定し、冷却剤を効果的に使用することが重要です。さらに、刃物を清潔に保つことも劣化防止になります。
腐食は、湿気や化学物質の影響で進行します。作業後に刃物を乾燥させ、防錆剤を塗布することで、腐食を予防することができます。
刃物寿命を延ばすためのメンテナンス
刃物の寿命を延ばすためには、日常的なメンテナンスが必要です。
まずは、使用後に刃物をきれいに洗浄し、乾燥させてください。その際に、細かい部分まで丁寧に確認して異物を取り除きます。次に切れ味が落ちてきた場合には、定期的に刃物を研ぐことが推奨されます。
さらに、専用の収納ケースに保管することで不要な衝撃や湿気から保護できます。これらの日常的なケアが、刃物の寿命を大きく延ばすカギとなります。
劣化した刃物の交換時期とは?
劣化した刃物は、早めに交換することが重要です。
刃先が鈍くなったり、亀裂が入ったりしたときが交換のサインです。このような状態の刃物を使用し続けると、加工精度が低下し、製品に不具合を引き起こすことがあります。
また、作業効率も落ちるため、無理に使用せず、新しい刃物に交換することをお勧めします。定期的なチェックと記録をつけることで、刃物の寿命を予測し、適切なタイミングで交換ができます。
加工する素材に適したバイトの選び方
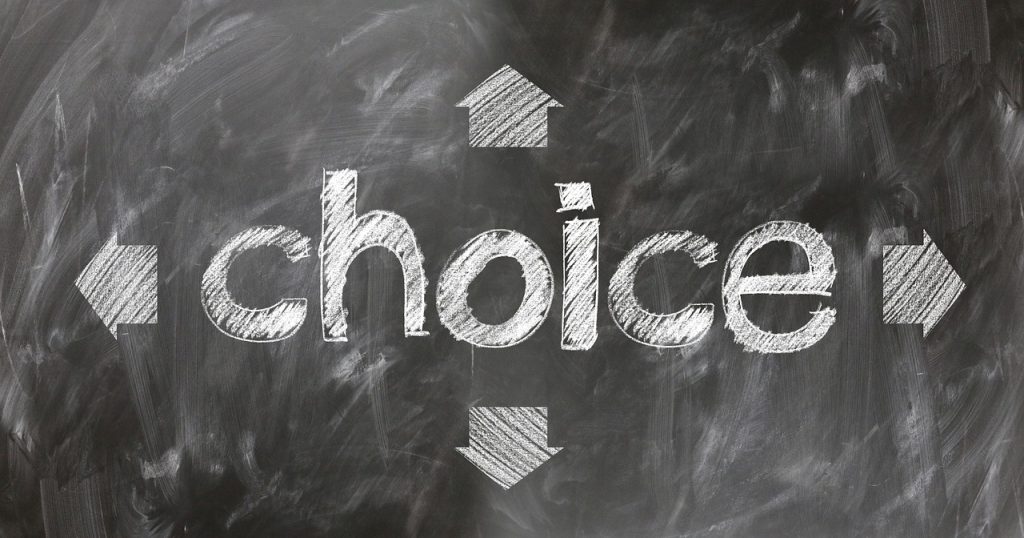
これまでに、バイトに使用されるチップの材質や、バイトの材質については触れてきましたが、ここでは、加工する素材に適したバイトについてまとめました。
加工する素材に適したバイトを使用することで、加工の効率や仕上がりは大きく変わってきます。加工対象となる素材の特性も理解しておきましょう。
アルミニウムを加工するのに適したバイトとは?
アルミニウムの加工に適したバイト(切削工具)は、アルミニウムの軟らかさと粘り気を考慮して選ばれます。アルミニウムは軽量で加工しやすいが、粘着性が高く、工具に材料が付着しやすい特性を持っています。以下はアルミニウム加工に推奨されるバイトの種類です。
- 超硬バイト
- アルミニウム加工専用の超硬バイトは、精密加工が可能で、耐摩耗性に優れています。
- 表面にポリッシュ加工が施されていることが多く、材料の付着を防ぎながら滑らかな加工面を実現します。
- ダイヤモンドコーティングバイト
- ダイヤモンドコーティングは、超硬バイトよりもさらに硬く、アルミニウムの粘着性による問題を効果的に軽減します。
- 高速加工時における耐熱性と耐摩耗性が高く、長寿命です。
- ポリクリスタリンダイヤモンド(PCD)バイト
- 高硬度で非常に耐摩耗性が高く、大量生産に適しています。
- アルミニウム合金や高シリコンアルミニウムの高速加工に特に効果的です。
- 高速度鋼(HSS)バイト
- 比較的柔らかいアルミニウムの加工には、高速度鋼も適していますが、超硬バイトに比べて耐久性は低くなります。
- 小ロットや一般的な加工にはコストパフォーマンスが良い選択となる場合があります。
これらのバイトは、アルミニウムの加工品質を向上させ、工具の寿命を延ばすために有効です。加工条件や機械の能力に応じて、適切なバイトを選ぶことが大切です。
硬い鋼材を加工するのに適したバイトとは?
硬い鋼材を加工する際に適したバイト(切削工具の一種)は、材料の硬さや加工の精度、耐久性などを考慮して選ばれます。以下に、硬い鋼材加工に適した主なバイトの種類を紹介します。
- 超硬バイト
- 超硬材料(タングステンカーバイドなど)で作られており、高硬度で耐磨耗性に優れています。
- 高速での加工や長時間の連続加工に適しています。
- セラミックバイト
- 非常に硬いセラミックス(酸化アルミニウムや窒化アルミニウムなど)で作られており、高温での切削に強い特性があります。
- 超硬バイトよりもさらに高い切削速度で加工が可能ですが、衝撃には弱いので注意が必要です。
- コーティングバイト
- 基本的なツール素材(超硬や高速度鋼など)に、チタンやアルミニウムなどの薄いコーティング層を施しています。
- コーティングにより耐熱性や耐摩耗性が向上し、長寿命で高精度の加工が可能になります。
- 高速度鋼(HSS)バイト
- 硬い鋼材の加工には限界がありますが、特殊な合金を使用した高速度鋼は、一般的な鋼材よりも耐熱性が高く、適度な硬さと靭性を持っています。
- 複雑な形状や精密な加工に使用されることがあります。
それぞれのバイトは加工する材料の特性や、求められる加工の性質に応じて選ばれます。硬い鋼材を効果的に加工するには、超硬バイトやセラミックバイトが一般的に推奨されますが、具体的な加工内容や設備にもよりますので、使用環境を考慮して選ぶことが重要です。
複合材を加工するのに適したバイトとは?
複合材(コンポジット材料)を加工する際には、材料の特性に合わせたバイト(切削工具の一種)を選択することが重要です。複合材は、異なる種類の材料が組み合わさっているため、それぞれの材料が持つ特性に適した加工方法が必要です。以下は複合材加工に適したバイトの例です。
- ダイヤモンドコーティングバイト
- ダイヤモンドは非常に硬いため、繊維強化プラスチック(FRP)やカーボンファイバー強化プラスチック(CFRP)などの硬質複合材料を効率的に加工できます。
- ダイヤモンドコーティングは耐摩耗性に優れており、切削面の品質を高めることができます。
- PCD(ポリクリスタリンダイヤモンド)バイト
- PCDは超硬材料よりも硬く、耐摩耗性が非常に高いため、アブレーシブな複合材を長時間にわたって高精度に加工できます。
- 自動車産業や航空産業での複雑な部品の加工に適しています。
- 超硬バイト
- 超硬バイトも複合材の加工に使用されることがありますが、ダイヤモンドコーティングやPCDバイトに比べると耐摩耗性に劣る場合があります。
- 一部の複合材やソフトマトリックス材料に適している場合があります。
- CVD(化学蒸着)ダイヤモンドバイト
- CVDダイヤモンドバイトは非常に硬いダイヤモンド層を持ち、極めて長い耐久性と優れた切削能力を提供します。
- 高い初期コストがかかるものの、長期的な使用においてコスト効率が良い場合があります。
複合材の加工には、材料が持つ繊維の種類、樹脂の種類、硬度、耐熱性など多様な特性を考慮する必要があります。特にカーボンファイバーやガラスファイバーなどの繊維強化材料を含む複合材では、切削時の繊維の引き抜きや欠けを防ぐために、適切な切削条件とともに適切なバイトを選択することが重要です。
まとめ
この記事では、旋盤加工におけるバイトの種類、特徴、選び方について詳しく説明してきました。
バイトは旋盤やフライス盤などで使用される切削工具であり、加工の精度や仕上がりに大きな影響を与える重要な要素です。バイトは、その構造、使用方法、形状、刃の方向、シャンクの形状や材質などによって多くの種類に分類され、それぞれに特有の用途や特徴があります。
適切なバイトの選定は、作業の生産性と加工精度に大きく影響します。そのため、加工する素材や最終的な目標を十分に考慮し、最適なバイトを選定することが大切です。
お問い合わせ
弊社製品、加工についてのお問い合わせは、こちらで受付しております。
各部門のスペシャリストが、ご質問にお応えします。
電話
0574-54-2231
(平日 8:15~17:15)
FAX
0574-54-2235