- 2024/06/04
-
製造業における部品加工の基礎知識!重要ポイントと最新動向
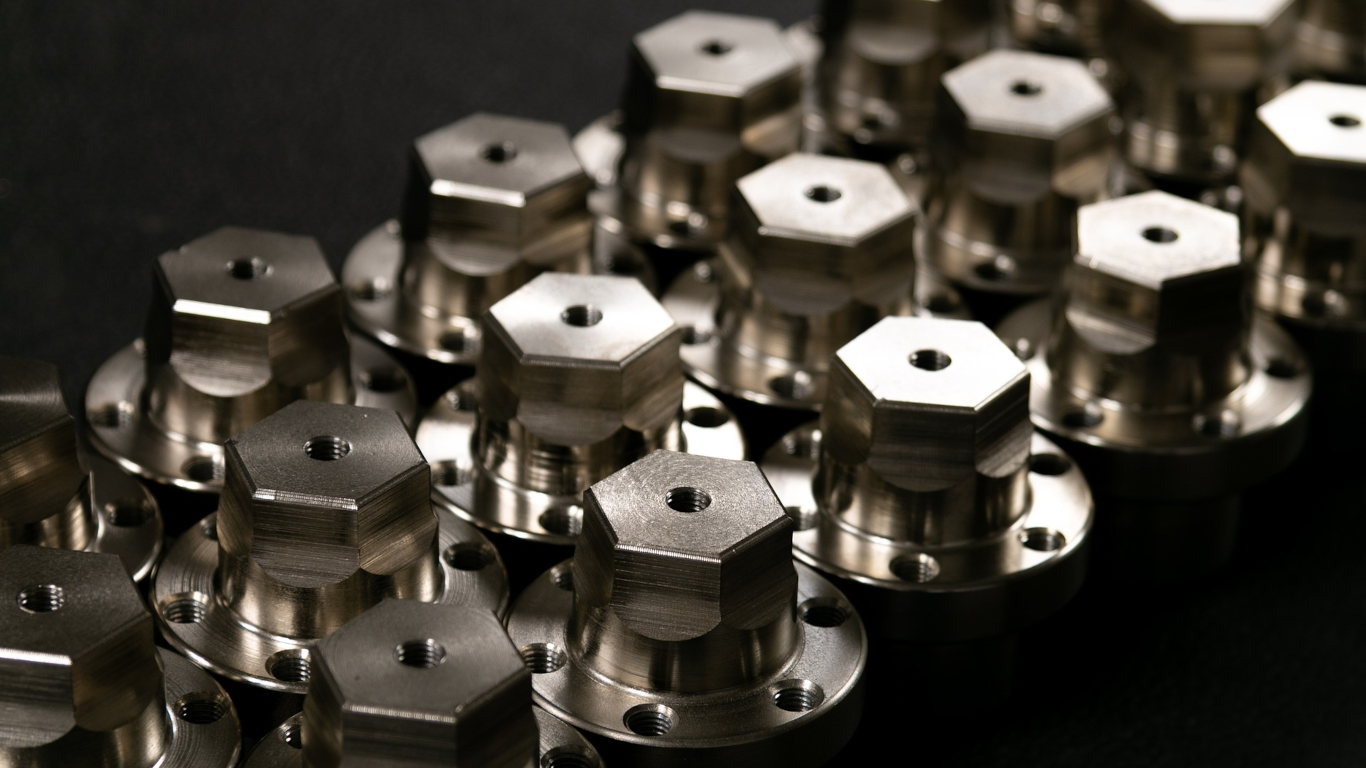
私たちの身の回りにある製品は、一つ一つの部品から組み上げられています。それらの部品を作り出すのが「部品加工」です。スマートフォンから自動車まで、あらゆる製品の製造に欠かせないこの部品加工ですが、その工程や技術は日々進化しています。
本記事では、部品加工の基本から最新のトレンドまでを網羅し、製造業者が押さえておくべき重要ポイントを解説します。製造業に携わる方や、これからこの分野に関心を持つ方にとって必見の内容です。
目次 [hide]
部品加工とは?基本的なプロセスと手法を解説
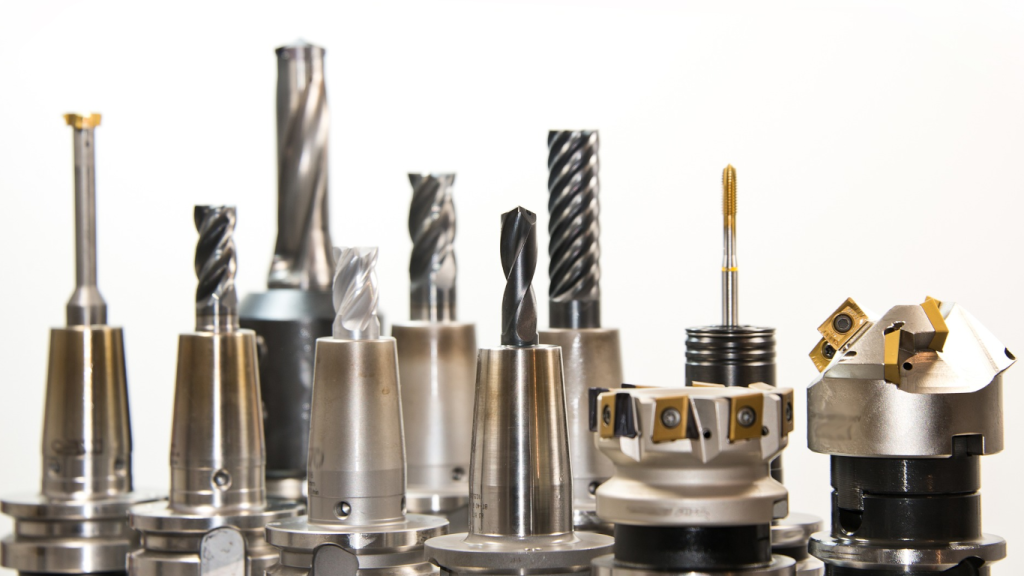
製造業において、部品加工は製品の品質と性能を左右する重要な工程です。技術の進化に伴い、加工方法や品質管理の手法も日々進化しています。部品加工のプロセスや手法は幅広く、多岐にわたります。それぞれの手法には特有の特徴や効果がありますので、理解しておくことが重要です。まずは、部品加工の基礎知識から始めましょう。
部品加工とは何か
部品加工とは、原材料を様々な加工方法を用いて、製品の設計図通りの形状や寸法に仕上げる工程のことです。言い換えれば、製品の骨格となる部品を作り出す工程です。
部品加工のプロセス
部品加工は、一般的に以下のプロセスで行われます。
- 設計段階:製品全体の設計に基づき、部品の形状や寸法、材料などを決定
↓ - 材料調達:設計図に基づいた材料を調達
↓ - 加工:さまざまな加工方法を用いて、材料を設計図通りの形状に加工、粗加工→精密加工
↓ - 検査:加工された部品が設計図通りの品質であるか検査
↓ - 仕上げ:必要に応じて、表面処理や熱処理などの仕上げを実施
主要な加工方法の概要
切削加工
切削加工は、材料を工具で削り取って目的の形状に整える加工方法です。主に金属やプラスチックなどの素材に適用され、旋盤やフライス盤などの機械を使用します。工具が材料表面を削り、余分な部分を取り除くことで、精密な寸法や形状を実現します。
- 特徴: 高精度で複雑形状の加工が可能。材料の無駄が多く、工具の摩耗が早い。
- 用途: 機械部品、自動車部品、航空機部品、金型など幅広い産業分野で使用。
研削加工
研削加工は、砥石を用いて材料の表面を削り、精密な形状や表面状態を得る加工方法です。切削加工では得られないような高精度な寸法や表面粗さが実現できます。熱影響が小さく、硬化材料の加工も可能です。
- 特徴: 高精度・高品質な仕上げが可能。加工速度が遅く、コストが高い傾向がある。
- 用途: 工作機械部品、自動車エンジン部品、ベアリング、金型など精密部品の製造。
プレス加工
プレス加工は、金属板などの素材を金型で挟み、圧力を加えて成形する加工方法です。板材の切断、曲げ、絞りなどの加工ができ、複雑な形状も一度の工程で形成できます。精度の高い金型を使用することで、均一な製品を効率的に生産できます。
- 特長: 大量生産に適しており、コスト効率が高い。短時間で大量の部品を成形できる。
- 用途: 自動車部品、家電製品、金属ケースなど、大量に同じ形状の部品が必要な製品に利用。
溶接加工
溶接加工は、熱や圧力を利用して金属部品を接合する加工方法です。アーク溶接、スポット溶接、レーザー溶接など様々な種類があり、それぞれ特性が異なります。金属を溶融させて強固に接合するため、高い強度が得られます。
- 特長: 高い接合強度を実現し、異なる素材の接合も可能。接合部が一体化するため、耐久性が高い。
- 用途: 建築用鋼構造物、自動車フレーム、配管システムなど、強固な接合が必要な場面で使用。
鍛造
鋳造は、金属を溶かして液体状にし、それを目的の形状の鋳型に流し込んで固める加工方法です。複雑な形状や中空構造の製品を一体成形できる利点があります。鋳鉄、アルミニウム、銅合金など様々な金属に適用可能で、大型から小型まで幅広いサイズの製品を製造できます。
- 特長: 複雑な形状や大型の部品を一度に作成可能。鋳造後の強度も高い。
- 用途: エンジンブロック、機械のフレームなど、形状の複雑さやサイズが重要な部品に適している。
鍛造
鍛造は、金属を加熱して圧力をかけ、形状を整える加工方法です。この過程で金属の結晶構造が緻密になり、強度と耐久性が向上します。鍛造は、耐久性が求められる高強度部品の製造に特に有効です。
- 特長: 高い強度と靭性を持つ部品を製造可能。密度が高く、耐久性のある製品が得られる。
- 用途: 車両のクランクシャフト、ギア、航空機の構造部品など、強度と耐久性が求められる製品に使用。
レーザー加工
レーザー加工は、高エネルギー密度のレーザー光を材料に照射し、熱エネルギーによって材料を融解・蒸発させることで、切断、穴あけ、溶接などの加工を行う技術です。従来の加工方法では難しかった微細な加工や複雑な形状の加工が可能です。
- 特長: 細かい加工が可能で、熱影響が少なく、材料の変形を抑えられる。柔軟性が高く、幅広い材料に適用。
- 用途: 精密な電子部品、微細な切断が必要な医療器具、薄い金属板の加工に利用。
これらの主要な加工方法を駆使することで、多様な部品が製造されます。用途に応じて最適な加工方法を選ぶことが、品質と生産効率を高める鍵となります。
各加工方法の選択ポイント
部品の加工方法を選択する際には、以下の表を参考に、製品の要求精度、形状、材料、数量、コストなどを総合的に考慮することが重要です。
加工方法 | 精度 | 生産量 | 材料適性 | コスト | 形状複雑性 |
---|---|---|---|---|---|
切削加工 | 高 | 少~中 | 広い | 中~高 | 高 |
研削加工 | 非常に高 | 少~中 | 硬質材料 | 高 | 低~中 |
プレス加工 | 中~高 | 大 | 板材 | 初期高、量産時低 | 中 |
溶接加工 | 中 | 少~大 | 金属 | 中 | 中~高 |
鋳造 | 低~中 | 中~大 | 金属 | 初期高、量産時中 | 高 |
鍛造 | 中 | 中~大 | 金属 | 初期高、量産時中 | 中 |
レーザー加工 | 高 | 少~中 | 広い | 中~高 | 高 |
高品質な部品を作るための3つのポイント
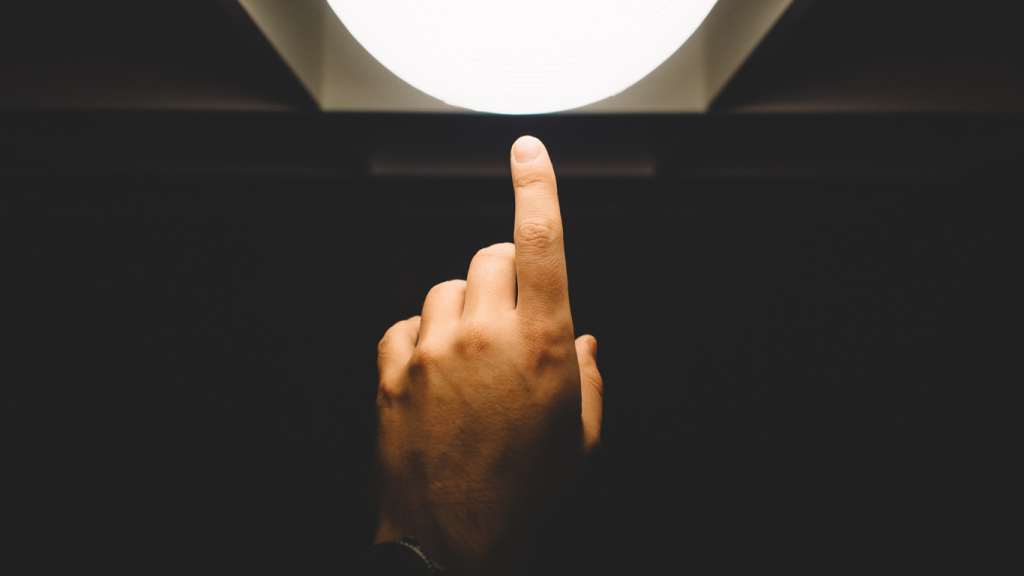
部品加工において、品質は製品の信頼性とパフォーマンスを左右する最も重要な要素です。高品質な製品を作るためには、部品の製造段階から細心の注意を払う必要があります。
ここでは、高品質な部品を作るために押さえておきたい3つの重要ポイントを解説します。
材料選定の重要性
材料選定は、部品加工の最初のステップであり、製品の性能や耐久性を大きく左右します。適切な材料を選定することで、部品の強度、耐熱性、耐腐食性などの特性を最適化することができます。例えば、自動車部品には高強度な合金が求められる一方、電子機器には軽量で熱伝導率の高い材料が必要です。
材料の選定に失敗すると、加工後に問題が発生したり、製品の寿命が短くなったりする可能性があるため、慎重な検討が必要です。材料のコストも重要な要素の一つです。性能とコストのバランスを考慮して、最適な材料を選択することが求められます。
加工精度の確保
高品質な部品を製造するためには、加工精度の確保が不可欠です。加工精度とは、設計図通りの寸法や形状をどれだけ忠実に再現できるかを指します。精密な加工機械や最新のCNC技術を活用することで、ミクロン単位での精度を実現することが可能です。
CNC技術(Computer Numerical Control、コンピュータ数値制御)とは
コンピュータを使用して機械工具の動きを制御し、材料の切削や加工を行う技術です。まず、CADソフトウェアを使用して部品の3Dモデルを設計し、その設計データを基にCAMソフトウェアで加工の工程をプログラムします。このプログラムがCNC機械に送られ、CNC機械は非常に高精度で複雑な形状を加工することができます。
人為的なミスが少なくなり、複雑な工程も自動で処理できるため、少量生産から大量生産まで幅広く対応可能です。また、プログラムを変更するだけで異なる製品の加工に対応できるため、柔軟性にも優れています。
表面処理の役割
表面処理は、部品の耐久性や美観、機能性を向上させるために行われる重要な工程です。例えば、部品の腐食を防ぐためのメッキ加工、摩耗を防ぐための硬化処理、さらには製品の外観を向上させるための塗装などがあります。
表面処理は、単なる仕上げ作業ではなく、部品の性能を長期間にわたり維持するための重要なプロセスです。適切な表面処理を施すことで、製品の寿命が延び、メンテナンスのコストも削減できます。
品質管理の重要性と最新技術
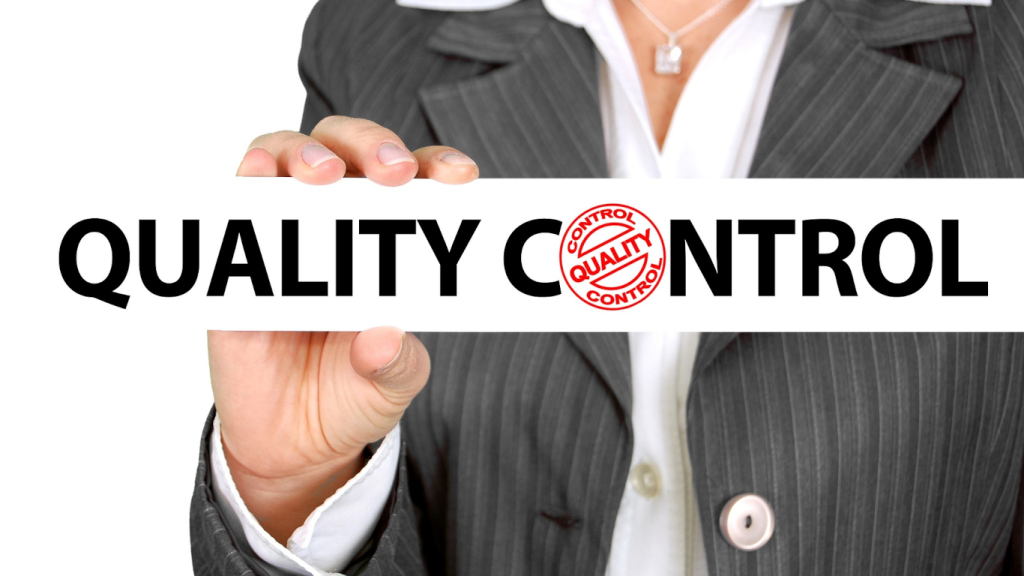
品質管理は、製品やサービスの品質を確保し、顧客満足の向上に寄与する重要なプロセスです。昨今、技術の進歩により品質管理の手法も大きく進化しています。従来の手法だけでなく、新しい技術を駆使することで、より高精度で効率的な品質管理が可能となっています。
品質管理の目的
品質管理の目的は、製品やサービスの一貫した品質を保証することです。そのためには、顧客のニーズと期待を満たすことが不可欠です。具体的には、製造過程や開発プロセスの管理を行い、製品の不良を最小限に抑えることを目指します。
また、品質管理はコスト削減や生産効率の向上にも寄与します。信頼性の高い製品を提供することができれば、顧客からの信頼も得られるようになります。
従来の品質管理手法
従来の品質管理手法としては、以下のものが挙げられます。
- サンプリング検査: 製品の一部を抽出して検査を行う方法です。全数検査に比べてコストを抑えることができますが、サンプリングの誤差が生じる可能性があります。
- 工程管理: 各工程における品質を管理し、不良品の発生を未然に防ぐ方法です。工程図や作業手順書を作成し、作業者に周知徹底することが重要です。
- 統計的品質管理(SQC): 統計学的手法を用いて、製品の品質変動を分析し、品質改善に役立てる方法です。
これらの手法は長年にわたり実績があるものの、全数検査が難しい場合や、リアルタイムでの品質監視が困難な点が課題とされていました。
最新の品質管理技術
近年では、IT技術の進歩に伴い、品質管理の分野でも様々な新しい技術が登場しています。
IoTセンサーとリアルタイムモニタリング
- IoTセンサーを生産設備に取り付けることで、温度、振動、湿度などのデータをリアルタイムで収集できます。これにより、異常発生を早期に検知し、品質問題の発生を防止できます。また、生産状況を可視化することで、生産効率の向上にも繋がります。
AIによるデータ分析と予測保全
- 加工中に収集されたデータをAIが解析し、不良品が発生しそうなパターンや傾向を予測。これにより、事前に対策を講じることができ、製品の品質向上とコスト削減を実現しています。また、予測保全により、設備のメンテナンスを最適化し、ダウンタイムを減少させます。
デジタルツイン
- デジタルツインは、物理的な部品加工ラインをデジタル上に再現し、リアルタイムでシミュレーションを行う技術です。これにより、加工工程の最適化や問題発生時の迅速な対策が可能になります。デジタルツインは、品質向上とともに、製造プロセス全体の効率化を図るツールとして注目されています。
クラウドベースの品質管理システム
- クラウド上に品質管理システムを構築することで、場所やデバイスに縛られずに、いつでもどこからでも品質データを閲覧・分析できます。また、複数の拠点やサプライヤーとのデータ連携も容易になり、サプライチェーン全体の品質管理を強化できます。
これらの最新技術を導入することで、従来では困難だった全数検査や予測的保全が現実のものとなり、品質のさらなる向上と生産効率の改善が期待されています。
品質保証のための国際規格
製品の品質を保証し、顧客の信頼を獲得するために、多くの国際規格が制定されています。これらの規格は、製品の設計、製造、販売に至るまでのプロセス全体を網羅し、品質管理システムの構築を支援します。
ISO 9001
代表的な規格としては、ISO 9001があります。この規格は、品質マネジメントシステム(QMS)の要求事項を定めたもので、全世界で広く採用されています。ISO 9001に準拠することで、企業は標準化された品質管理を行うことができます。
その他の国際規格
規格名 | 内容 |
---|---|
ISO 13485 | 医療機器に関する品質マネジメントシステム規格 |
IATF 16949 | 自動車産業向けの品質マネジメントシステム規格 |
AS9100 | 航空宇宙産業向けの品質マネジメントシステム規格 |
グローバルなビジネス環境で競争力を維持するためには、これらの国際規格を遵守し、継続的な改善を行うことが重要です。品質保証のための国際規格は、製造業における品質管理の基盤を築く鍵となります。
部品加工の未来と最新トレンド
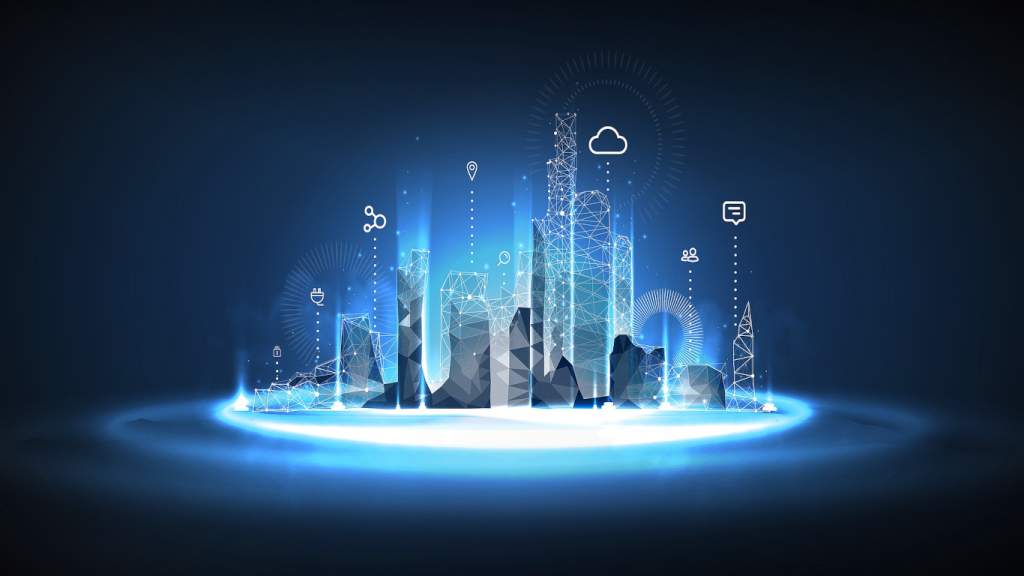
製造業の基盤となる部品加工は、技術革新の波に乗って大きな変革を遂げています。AIやIoT、3Dプリンティングなどの新技術の登場により、効率性や精度が飛躍的に向上し、持続可能な社会への取り組みも進展しています。ここでは、部品加工の未来を見据えた最新トレンドと今後の展望について詳しく解説します。
部品加工におけるDX技術の今後の展望
部品加工分野におけるDXは、生産現場の革新をもたらし、企業の競争力強化に大きく貢献しています。今後も、様々なDX技術が融合し、より高度な生産システムが構築されていくことが期待されます。
エッジコンピューティング
- エッジコンピューティングは、データ処理をクラウドではなく現場で行う技術です。これにより、部品加工におけるリアルタイムの品質管理や設備の監視が可能になり、遅延を最小限に抑えた迅速な対応が実現します。今後、IoTセンサーと組み合わせることで、加工ラインの効率化や異常検知の精度向上が期待されます。
量子コンピューティング
- 量子コンピューティングは、従来のコンピュータを超える処理能力を持つ技術で、複雑な部品加工の最適化やデータ解析を瞬時に行うことが可能です。特に、多変量のデータをリアルタイムで処理し、最適な加工条件を導き出すことが期待されています。これにより、加工の精度と効率が劇的に向上すると考えられています。
拡張現実(AR)と仮想現実(VR)技術の活用
- ARは、リアルタイムで加工状況を視覚化し、作業の精度を高める手助けをします。一方、VRは、仮想環境での訓練を可能にし、複雑な加工手順を習得する際のリスクを低減します。今後、さらなる技術進化により、現場作業の効率が飛躍的に向上するでしょう。
自律型ロボットの普及
- 自律型ロボットは、AIとセンサー技術を駆使して、部品加工の自動化と精度向上を実現します。これらのロボットは、人間の手を借りずに複雑な加工や検査を行い、製造プロセス全体の効率を大幅に改善します。今後、より多くの工場で導入が進み、労働力不足の解消や製品品質の向上が期待されています。
ブロックチェーンによるトレーサビリティの強化
- ブロックチェーン技術は、部品の製造履歴や品質データを分散型ネットワークで管理し、データの改ざんを防ぎます。これにより、製造工程全体の透明性が向上し、品質保証の信頼性が高まります。今後、サプライチェーン全体での導入が進むことで、部品のトレーサビリティが一層強化され、不良品のリスクが低減されると考えられます。
3Dプリンティングの進展
3Dプリンティングの技術が進展することで、部品加工の可能性が広がっています。3Dプリンターを用いることで、従来は難しかった形状や複雑な構造も短時間で作成することが可能になります。さらに、3Dプリンティングは、試作から量産まで一貫して行えるため、製品開発のスピードが大幅に向上します。
また、この技術は、必要な部分だけをプリントするため、材料の無駄を減らすことができます。これにより、コスト削減と持続可能な生産が同時に達成できます。未来の部品加工において、3Dプリンティングは欠かせない技術と位置づけられるでしょう。
3Dプリンティングのメリット
- 試作期間の短縮: 従来の製造方法に比べて、試作期間を大幅に短縮することができます。
- 多品種少量生産への対応: 少量の部品を短納期で製造できるため、多品種少量生産に適しています。
- カスタマイズ製品の製造: 個々の顧客のニーズに合わせたカスタマイズ製品の製造が可能になります。
- 新素材の活用: 金属やセラミックなど、様々な素材を用いた3Dプリンティングが可能になり、新たな製品開発の可能性が広がっています。
持続可能な社会の実現に向けた取り組み
現在、多くの企業が環境負荷を軽減するために積極的な取り組みを行っています。例えば、再生可能エネルギーを利用した工場の稼働や、リサイクル可能な材料の使用が進められています。さらに、廃棄物を最小限に抑えるための生産プロセスの最適化も行われています。
これらの取り組みにより、環境への負荷を最小限に抑えながら、高品質な製品を提供することが期待されています。今後も、環境と経済のバランスを保ちながら、持続可能な製造プロセスの実現に向けた取り組みが加速していくでしょう。
まとめ
AIやIoT、3Dプリンティングといった最先端技術が、部品加工の常識を覆し、新たな可能性を切り開いています。かつては想像もできなかったような高度な自動化、多様な材料の活用、そして持続可能な生産が現実となりつつあります。この変化の波に乗り遅れることなく、技術革新を積極的に取り入れる姿勢が、製造業の成功への鍵となります。常に進化する加工技術を学び、現場での実践に活かしていきましょう。
お問い合わせ
弊社製品、加工についてのお問い合わせは、こちらで受付しております。
各部門のスペシャリストが、ご質問にお応えします。
電話
0574-54-2231
(平日 8:15~17:15)
FAX
0574-54-2235