- 2024/07/29
-
旋盤加工で高精度な精密部品を製作するには?加工の種類・精度・業者選びまで解説
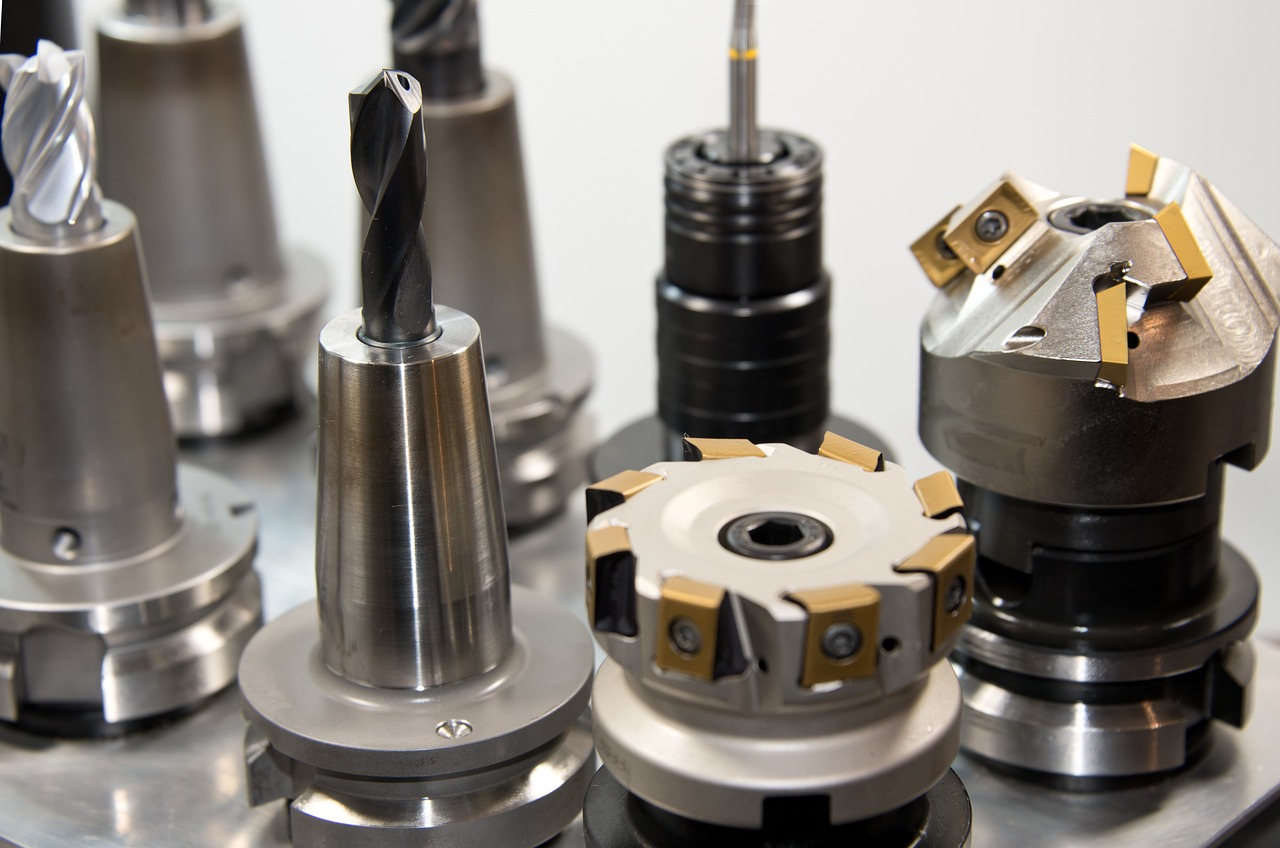
製造現場では、ミクロン単位の精度が求められる部品が数多く存在します。そうした精密部品の加工において、旋盤加工は欠かせない大切な手法です。本記事では、旋盤加工の基礎から、精密部品製作のポイント、さらには加工業者選びのコツまで、わかりやすく解説します。
旋盤加工とは?基本の仕組みと特徴

旋盤加工とは、金属や樹脂などの素材を回転させ、固定した刃物(バイト)で削っていく加工方法です。素材を主軸に固定し、高速で回転させながら、工具を移動させて形状を整えていきます。
この加工法は特に、軸や円筒状の部品製作に適しており、高い同心度と寸法精度が得られるのが特徴です。また、再現性にも優れており、1個ずつの単品加工から、同じ寸法での大量生産まで幅広く対応可能です。
自動車、電子機器、医療機器、航空機、工作機械など、さまざまな分野で活用されています。
汎用旋盤とNC旋盤の違い
旋盤加工には大きく分けて、手動操作が中心の「汎用旋盤」と、コンピューター制御による「NC旋盤」の2種類があります。どちらも用途に応じて使い分けられており、それぞれに明確な強みと特徴があります。
ここでは、それぞれの特徴を詳しく見ていきましょう。
汎用旋盤
汎用旋盤は、作業者が手動でハンドルやレバーを操作しながら加工を行う、いわば職人の技術が活きる伝統的な旋盤です。
その柔軟性により、少量の試作や多品種少量生産、図面のない古い部品の再現などに強みを発揮します。
ただし、寸法の安定性は作業者の技量に大きく左右されるため、高いスキルが必要とされます。
NC旋盤(数値制御旋盤)
NC旋盤は、コンピューターによって制御される自動加工機で、あらかじめプログラムされた動作に従って工具を正確に動かします。
複雑な形状の加工や大量生産に向いており、均一な品質を安定して供給できるのが利点です。最近では、タレット型の刃物台や、自動工具交換装置を備えたモデルも多く、無人運転にも対応しています。
旋盤加工が得意な加工内容
旋盤加工は、その構造上、回転対称の形状を高精度で加工するのにおすすめの工法です。特に、円筒形の部品や内径・外径の仕上げ、さらにはネジやテーパーといった特殊な形状まで、多岐にわたる加工に対応できます。
ここでは、旋盤加工が特に得意とする代表的な加工対象を見ていきましょう。
シャフトやピンなどの軸物部品
旋盤加工の王道ともいえるのが、円柱状の部品です。自動車のドライブシャフト、機械の回転軸、各種ピン類など、同心度や真直度が重要な部品におすすめです。精密さを要求される軸物では、±数ミクロンの精度も求められることがあります。
内径・外径の高精度仕上げ
内径(穴)や外径(外周)の寸法をμm(マイクロメートル)で仕上げることも可能です。内径加工には、専用のボーリングバーや内径バイトを使用し、真円度や面粗度を維持しながら正確に仕上げます。
外径については、段付き形状やストレート形状を滑らかに加工でき、摩擦や摺動が発生する部品の精密仕上げにも対応できます。
ネジやテーパーなどの特殊形状切削
旋盤加工では、ねじ切りやテーパー加工(傾斜のある形状)にも対応可能です。ネジ部は、ボルトやナットに使用されるだけでなく、精密機器の固定や調整にも欠かせません。
また、テーパー加工は、工具や機械部品の圧入・着脱性を高めるために多用されます。NC旋盤を使用すれば、複雑なネジ山や多段テーパーも正確に再現できます。
精密部品に求められる加工精度とは?
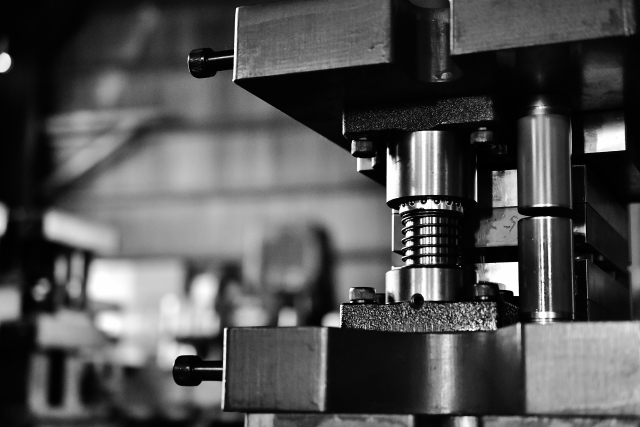
「精密部品」とは、わずかな寸法誤差すら製品機能に影響を与えるような、高精度が求められる部品を指します。
製造誤差の許容範囲(公差)がとても狭く、±1μm(マイクロメートル)以下の寸法精度が必要なケースも多く見られます。このレベルの精度は、たとえば髪の毛の太さ(約70μm)の70分の1程度。目視ではまったく確認できない誤差です。
このような精密加工は、単に機械の性能だけで実現できるものではありません。以下のように、複数の要素が複雑に絡み合っています。
精度を左右する主な要因
精密部品の加工では、わずか数ミクロンの誤差が性能や安全性に直結するため、加工精度に影響する要素を正しく理解し、コントロールすることが大切です。
ここでは、旋盤加工において精度を左右する主なポイントを紹介します。
使用する旋盤設備の性能
高精度なNC旋盤や複合加工機には、微細な送り制御や振動抑制機構が搭載されており、安定した精密加工が可能です。特に近年では、温度補正機能やリアルタイムモニタリング技術も向上しています。
加工材の熱膨張や性質
材質によっては、加工中の熱により微小な伸びや変形が生じます。たとえばアルミは熱膨張率が高く、加工中にサイズが変わりやすいため、材質ごとの特性を理解したうえで適切な条件設定が必要です。
加工環境の温度管理
加工現場の室温が変化するだけでも、部品寸法に影響を与える可能性があります。そのため、精密加工を行う現場では、恒温室での加工や機械の熱変位対策が重視されます。
作業者のノウハウと経験
高精度加工においては、最終的な仕上がりを左右するのは熟練技術者の判断力と調整力です。切削条件の微調整や、工具の摩耗状態の把握など、人の技が必要とされる場面は少なくありません。
このように、精密部品の品質は、設備・材料・環境・技術者のスキルといった複数のファクターが揃って初めて達成されるものです。どれか一つが欠けても、目指す精度には届かないのです。
旋盤加工で対応可能な精密部品の具体例
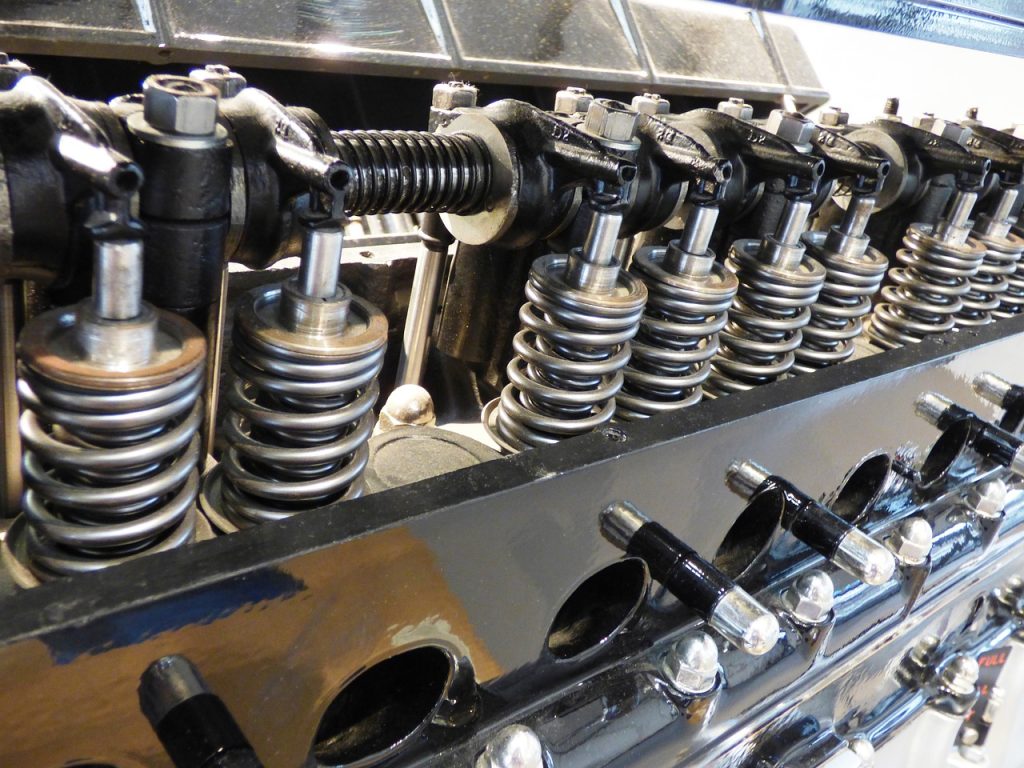
旋盤加工は、高精度かつ均一な加工精度を実現できる精密部品の製作において不可欠な技術です。さまざまな業界で必要とされる微細で複雑な形状の部品にも対応でき、その活用範囲はとても広いのが特徴です。
ここでは、旋盤加工によって製作される代表的な精密部品の例を紹介します。
自動車部品
自動車分野では、エンジンやトランスミッション、ブレーキ周辺の重要保安部品において、高精度な軸物部品が多数使用されています。
たとえば、
- クランクシャフトやカムシャフトなどの回転軸
- スリーブ、ピン、ギアシャフトなどの摺動部品
- 燃料噴射系の精密ノズル部品
これらは、耐摩耗性と真円度、同心度が重要視され、厳しい品質管理のもとで加工が行われます。
医療機器部品
医療分野では、人体に接触するため、寸法精度だけでなく高い清潔性やバリレス(切削残りのない)仕上げが求められます。
- 手術用インスツルメント(ドリル、カニューレなど)
- 内視鏡や注射器の金属構成部品
- 人工関節やインプラント部品の一部構造
これらには、SUS316Lなどの耐腐食性に優れたステンレス材が用いられ、鏡面仕上げや微細形状の加工も行われます。
航空・宇宙分野の部品
航空機や宇宙機器に使用される部品は、極端な軽量化と強度の両立が求められるため、加工難易度が非常に高いです。
- チタンやインコネル合金を使用したタービン部品
- センサー取付け部、配管接続部の高圧用継手
- 精密な取付け穴や段付きシャフトなど
旋盤加工では、耐熱性・耐腐食性素材をμ単位で仕上げる高い切削制御技術が必要になります。
半導体製造装置部品
半導体装置では、ミクロン単位の精密性はもちろん、パーティクル(微粒子)の発生抑制や表面処理の均一性も求められます。
- ウェーハ搬送用シャフト
- 真空配管部の高精度フランジ
- センサー固定具やミニチュアスリーブ部品
これらの部品は、超精密切削加工と、最終工程での高精度測定・洗浄工程を経て製作されます。機械的精度だけでなく、表面の粗さや清浄度も品質に直結します。
このように、旋盤加工は業界を問わず、高い信頼性と耐久性が求められる精密部品の製作に幅広く対応しています。材料や形状、要求精度に応じた柔軟な対応力が、現代のものづくりを支える大切な技術となっています。
精密部品加工を依頼する業者選びのポイント
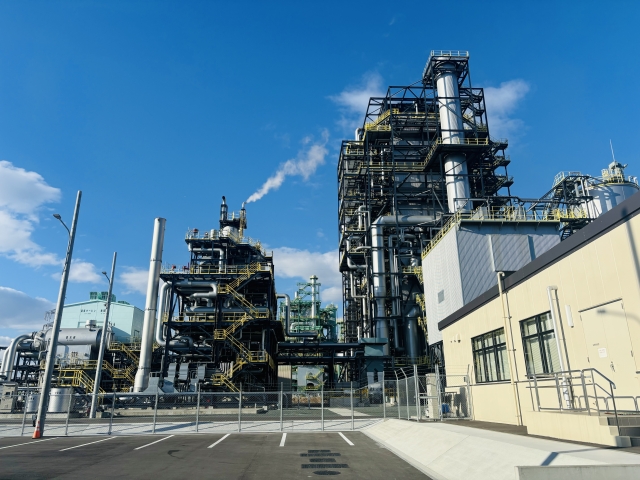
精密部品の加工においては、たとえ図面通りに製作できても、期待通りの品質・納期・コストに応えるには、信頼できる業者選びが大切です。
旋盤加工は一見単純に見えて、実は素材特性・加工条件・精度管理など、複雑な要素が絡み合う繊細な作業。だからこそ、業者選びでは以下のようなポイントをしっかりと見極める必要があります。
実績・対応素材の確認
まず注目すべきは、その業者がどのような業界や部品に対応してきたかという実績です。
自動車・医療・半導体など、用途によって求められる精度や品質基準は異なるため、自社のニーズと近い加工実績があるかは大切なチェックポイントです。
また、加工対応材質の幅広さも技術力の証と言えます。たとえば、アルミや真鍮などの汎用素材だけでなく、チタン・インコネル・POM・PEEKなどの難削材や樹脂に対応できるかどうかも評価基準になります。
最新設備の導入状況
高精度な旋盤加工には、設備の性能が直接品質に影響します。
CNC旋盤(数値制御旋盤)はもちろん、複合加工機、5軸旋盤、同時加工機などの高度な設備を保有しているかどうかは、対応可能な形状や精度の幅を左右します。
加えて、自動工具交換や無人運転への対応、CAD/CAM連携による高効率加工の実現など、技術の進化を積極的に取り入れている業者は信頼性が高いです。
品質管理体制
どれだけ高性能な設備を使っていても、検査体制が甘ければ精密部品としての信頼性は確保できません。
国際標準であるISO9001やIATF16949の取得は、品質マネジメントが体系化されている証拠です。
また、三次元測定機、形状測定機、粗さ測定機、画像寸法測定器など、検査機器の保有状況を確認することで、どこまでの品質保証が可能かが見えてきます。
小ロットや試作への柔軟性
量産前の製品開発段階では、「まずは試作をして形状や性能を検証したい」というニーズが多くあります。
このような場合、小ロット・短納期対応が可能か、個別相談に応じてもらえるかといった柔軟性があるかどうかも業者選びの大切な基準です。
最近では、設計段階からの技術提案(DFM:Design for Manufacturability)を行ってくれる業者もあり、開発スピードの向上に寄与するケースも増えています。
このように、旋盤加工業者を選定する際には、「設備」「実績」「品質」「対応力」の4つの軸で総合的に判断することが、失敗しないポイントです。
信頼できる業者を見つけることが、製品の性能・コスト・開発スピードすべてに良い影響をもたらします。
旋盤加工の精度を高める最新技術
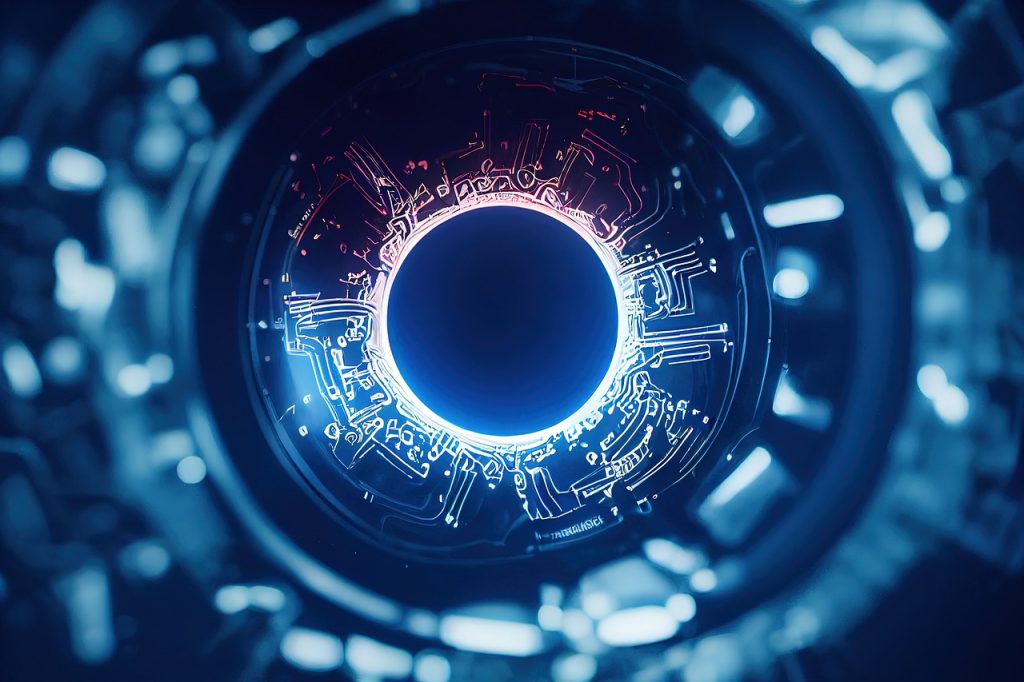
近年、製造業における技術革新はめざましく、旋盤加工の分野においても、IoT、AI、複合加工、自動化技術などの導入が進み、より高精度・高効率な加工体制が構築されつつあります。
従来の人の勘や経験に依存した加工から、デジタル制御・データ活用による安定した品質の確保へと進化しており、以下のような技術が注目されています。
5軸制御・複合加工機の活用
従来の旋盤加工では、複数の工程(旋削・フライス・穴あけなど)を別々の機械で行い、段取り替えが必要でした。これには精度劣化のリスクが伴います。
しかし、5軸制御旋盤や複合加工機(ミーリングと旋削が一体化された設備)を活用することで、1台で複数の工程をシームレスに処理できるようになり、以下のようなメリットが得られます。
- ワンチャッキング(一度の取り付け)で完結するため、段取りズレや芯ずれによる誤差をできる限り抑えられる
- 工程集約によって納期短縮や人件費の削減にもつながる
- 複雑な3次元形状や自由曲面にも対応し、設計自由度が拡大
とくに試作や小ロット生産においては、段取り時間の削減が全体効率に大きく影響するため、導入のメリットは大きいです。
IoT・自動化技術の導入
旋盤加工においても、IoT技術を活用したリアルタイム監視や予知保全が進んでいます。
たとえば、
- 加工中の工具摩耗状態の自動検知
- スピンドルや送り装置の振動・温度・負荷のモニタリング
- 異常時のアラート通知や、不良傾向の分析・予測
これにより、加工中のわずかな変化を捉えて不良の発生を事前に防止できるだけでなく、稼働率の向上や品質の均一化にも貢献します。
また、ロボットと連携した無人運転・自動供給システムの導入も進み、夜間稼働や24時間対応によって、さらなる生産性向上が期待されています。
CAD/CAMとの連携
設計段階から製造までをスムーズにつなぐためには、CAD/CAM(Computer-Aided Design / Computer-Aided Manufacturing)との統合が欠かせません。
- CADで作成した3Dモデルから直接CAMソフトに加工指示を転送し、自動でより良い工具パスを生成
- ヒューマンエラーを減らし、プログラムミスや段取りミスの低減
- 工程シミュレーションによる干渉チェック・加工時間の効率化
これにより、試作から量産への立ち上げスピードが大幅に短縮されるとともに、設計者と加工現場との情報共有が円滑になり、トータルでの精度管理が向上します。
このように、最新技術の導入は、単に生産効率を高めるだけでなく、寸法精度・再現性・品質保証という精密加工における根幹部分の向上にも直結しています。
これからの旋盤加工では、「熟練技術 × デジタル技術」の融合が、さらなる進化を支えるキーワードとなるでしょう。
まとめ
旋盤加工は、ミクロン単位の寸法精度や滑らかな仕上がりを実現できる、高精度加工に適した手法です。
円筒形状を中心とした部品加工において、さまざまな素材や形状に対応できる柔軟性もあり、自動車・医療・航空・半導体など、幅広い分野で活用されています。
高精度な精密部品を実現するためには、旋盤の種類や性能だけでなく、加工環境・素材の特性・作業者の技術力・品質管理体制といった複数の要素が組み合わさることが大切です。
さらに近年では、5軸加工機やIoT、自動化、CAD/CAMとの連携など、新しい技術の導入によって、より精密で効率的な加工が可能となっています。
これらを踏まえて、旋盤加工の基礎から応用までを理解することが、品質向上と製品開発の成功に直結する第一歩となるでしょう。
お問い合わせ
弊社製品、加工についてのお問い合わせは、こちらで受付しております。
各部門のスペシャリストが、ご質問にお応えします。
電話
0574-54-2231
(平日 8:15~17:15)
FAX
0574-54-2235